
Inhoudsopgave:
2025 Auteur: John Day | [email protected]. Laatst gewijzigd: 2025-01-23 15:01
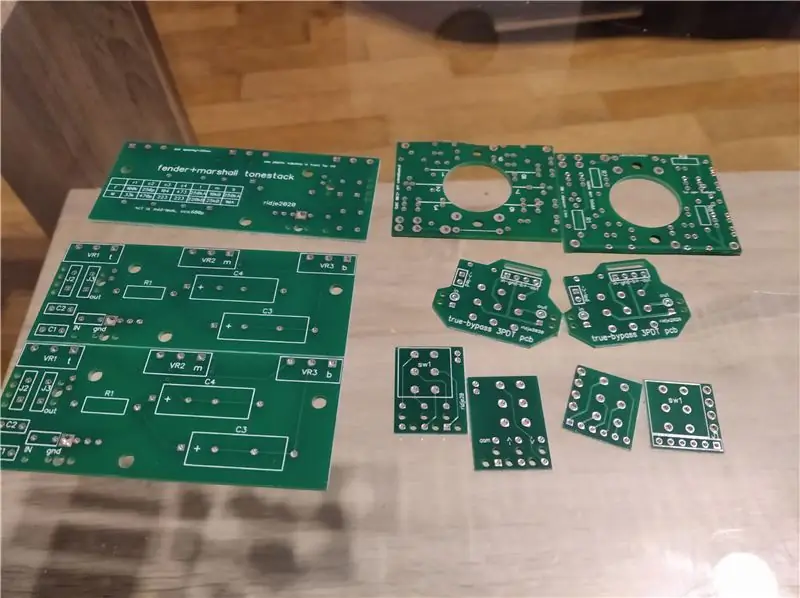
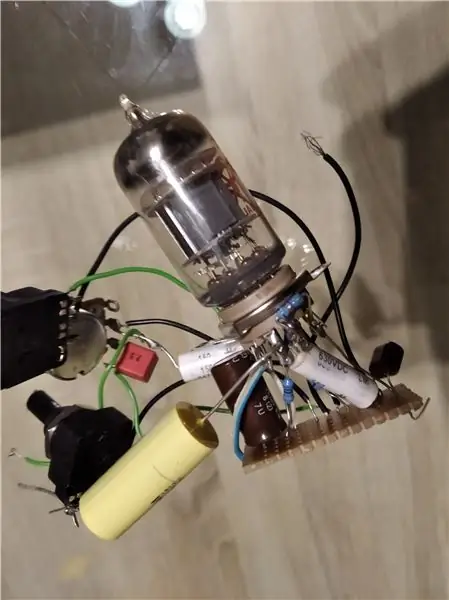
Buizencircuits waren een cruciale stap in de ontwikkeling van de elektronica. In de meeste gebieden raakten ze volledig achterhaald in vergelijking met goedkopere, kleinere en efficiëntere solid-state-technologieën. Met uitzondering van audio - zowel reproductie als live. Omdat buizencircuits relatief eenvoudig zijn en meestal mechanisch werk, verbonden met het maken van een buizenversterker, zijn ze ideaal voor zelfbouw - doe-het-zelf. Ze zijn zeker verbonden met hoogspanning en kunnen dus gevaarlijk zijn, maar als enkele basisrichtlijnen worden gevolgd, kan het grootste deel van het gevaar worden vermeden.
De eerste benadering van het bouwen van buizencircuits was zogenaamd point-to-point, waarbij elementkabels direct werden bevestigd aan buisvoeten, potten, jacks … met behulp van verschillende terminals. Om massaproductie te vergemakkelijken, begonnen bedrijven de elementen op verschillende borden te plaatsen (sommige benaderingen werden nog steeds point-to-point genoemd, hoewel dat niet echt zo was). Tegenwoordig wordt de meeste elektronica gemaakt als PCB's - printplaten. Zelfs de meeste in massa geproduceerde buisontwerpen worden tegenwoordig op PCB's gemaakt. Maar PCB's hebben bepaalde nadelen voor de buizenwereld: - buizen produceren veel warmte wanneer ze aan staan, dus zelfs bij normaal functioneren zijn ze geneigd de levensduur van de PCB aanzienlijk te verkorten - meestal zijn buiscircuits zo eenvoudig en ongecompliceerd, en de gebruikte (hoge voltage) elementen zo groot dat het niet echt zin heeft om buizencircuits op hele borden te produceren - er zou meestal lege ruimte en weinig sporen zijn met sommige pads - echt een verspilling van FR4-materiaal - veel componenten van het buizencircuit zijn te zwaar of te volumineus om direct op de print te monteren (transformatoren, smoorspoelen), andere zijn ongeschikt voor print vanwege mechanische belasting (buizen waarvan de sockets direct op de print zijn gemonteerd, moeten voorzichtig worden vervangen)
Aan de andere kant is het soms moeilijk om rechtstreeks op de versterkeronderdelen te solderen, en sommige hebben de neiging om tijdens het proces beschadigd te raken (ik ben erin geslaagd een flink aantal schakelaars te verpesten als ik eraan soldeer). Het is ook moeilijk om problemen op te lossen en te onderhouden met klassieke point-to-point gebouwde apparaten, vooral als ze niet met een extreem goede planning zijn gebouwd. PCB geeft een solide en van het chassis afneembare manier om elementen te bevestigen.
Dus de situatie vraagt om een manier van half-punt-naar-punt bedrading, vergelijkbaar met wat ze deden in bekende gitaarversterkers zoals Marshall of Fender. Veel bouwers gebruiken hun aanpak nog steeds met geweldige resultaten. Maar de Fender - Marshall-aanpak heeft enkele nadelen:
- ze gebruiken meestal axiale componenten, die zeldzaam en dus minder betaalbaar zijn - de meeste circuitelementen zijn parallel, wat ruimteverspilling veroorzaakt en kan leiden tot ruis, oscillaties en elementkoppeling - er zijn lange blootliggende draden op de borden - dit bord wordt dan vaak in het midden van het chassis gemonteerd, waardoor alle plaatsing van de buizen eruit wordt geduwd, wat weer suboptimaal is
Een eenvoudig en vrij gelijkaardig ontwerp van de meeste hifi- en gitaarcircuits stelt ons in staat om een modulaire benadering te gebruiken bij het bouwen van buizenversterkers, met behulp van PCB-modules. Het bestuderen van de schema's helpt ons bij het ontwerpen van PCB's, waarbij er geen ruimte wordt verspild met parallelle elementen, maar de regels van traceringsroutering volgen. Dubbelzijdig ontwerp stelt ons in staat om modules kleiner te maken en beide zijden van het bord te gebruiken. We kunnen connectoren op PCB's solderen, wat het nog eenvoudiger maakt om problemen met apparaten op te lossen en te onderhouden.
Voor een doe-het-zelver is het niet praktisch om voor elk project een printje te ontwerpen, dat zou behoorlijk duur zijn! Maar eenvoud en gelijkenis van gemeenschappelijke buisontwerpen stelt ons in staat PCB's te ontwerpen, die voor de meeste toepassingen bruikbaar zijn.
Hier is een "verzameling" van enkele PCB's die ik heb ontworpen om het maken van buizenversterkers te vergemakkelijken.
- dubbele triode point-to-point PCB
- toonstapel PCB
- stompschakelaar PCB
- twee schakelprintplaten
Stap 1: Dubbele Triode / Noval / Preamp PCB
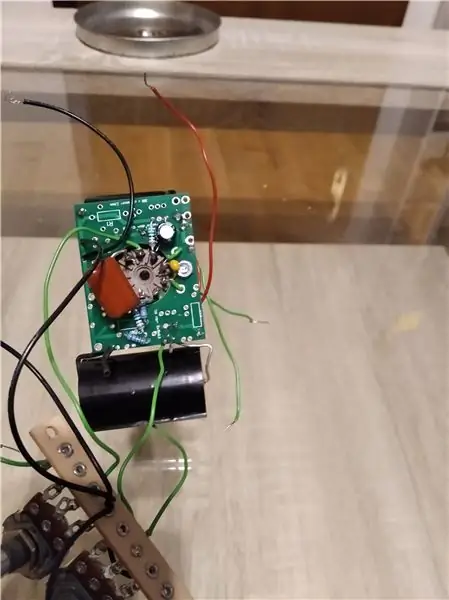
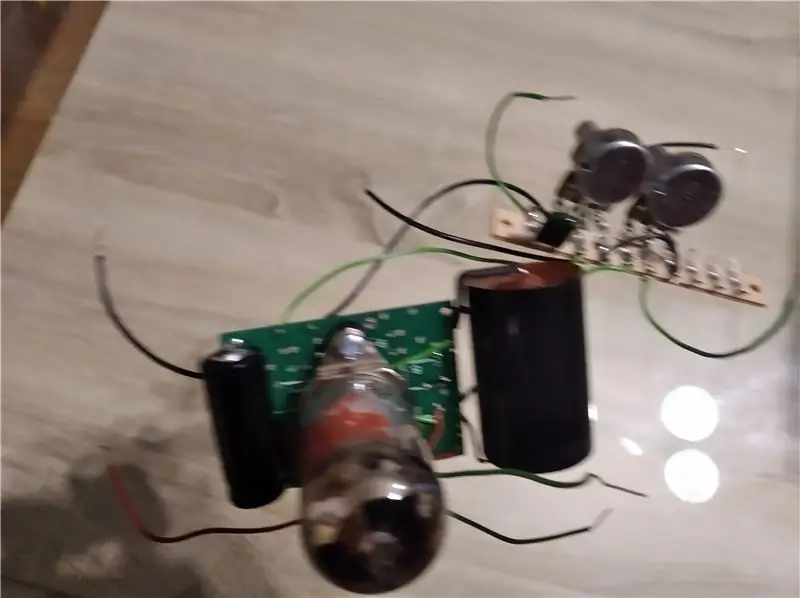
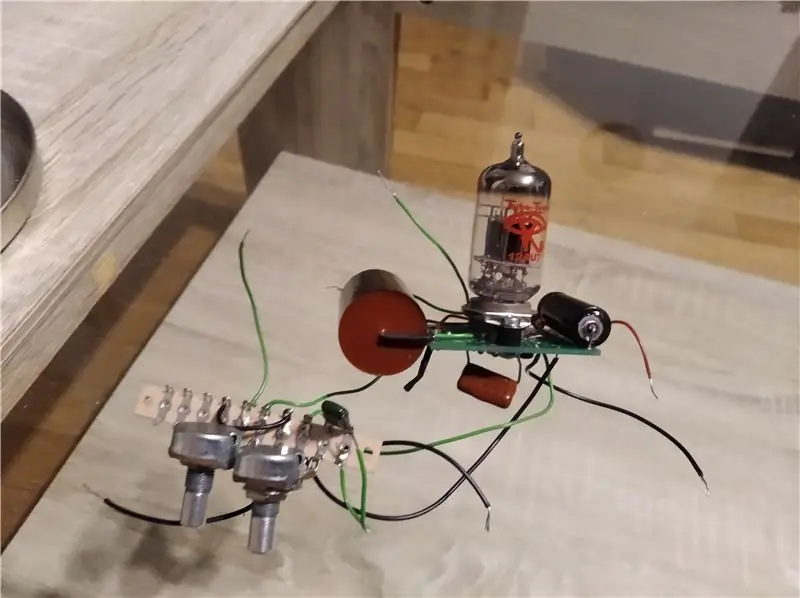
De voorversterkersectie is vrij gelijkaardig in de meeste buizentoepassingen en bestaat meestal uit reeksen dubbele triodes in nieuwe pakketten, vaak 12AX7-buizen. Soms is er een kathodevolgeropstelling, maar meestal zijn er alleen verschillende combinaties van rasterstop + plaatweerstand + kathode-bypass-kap + voorspanningsweerstand + koppelkapwaarden. Het is dus niet zo'n veeleisende taak om een pcb te ontwerpen, die vrij universeel zou zijn voor het voorversterkergedeelte van het versterkercircuit - of voor de novale buis (netten zijn zo gemaakt dat ook de meeste novale niet-dubbele triode buizen kunnen gemakkelijk worden gebruikt). PCB is ontworpen om in een 1U-rackbehuizing te passen (buis is horizontaal) - anders zou het nuttig zijn om het een beetje groter te maken. Het is aan de gebruiker welke elementen naar welke kant van de PCB gaan. Zeefdruk is hier alleen als hulpmiddel bij de oriëntatie.
De print is ontworpen om samen te gaan met de noval Belton socket. Het zit vast via de socket (dus het verwisselen van de buizen is geen belasting voor de printplaat). Het moet aan de sockets worden bevestigd met enkele afstandhouders ertussen. Het ene uiteinde van bepaalde elementdraden wordt rechtstreeks op de socket gesoldeerd, andere worden op de PCB gesoldeerd. Er zijn enkele extra pad-trace-groepen (algemene naam is net) op het bord om te helpen bij verschillende instellingen. Om de print verder uit te leggen is het waarschijnlijk het beste om door de buispinnen te gaan. _
- op het "zuiden" van de print zit een "grondbus" met weinig sporen die naar de corresponderende plaatsen op het printje gaan - op het "noorden" zijn twee netten voorzien voor B+ - er moet een jumper zijn (witte lijn) geïnstalleerd om ze aan te sluiten (dat detail maakt deze PCB ook bruikbaar voor novale buizen zonder dubbele triode)
1 - plate1 - (witte lijn gemarkeerd met 1 aan de andere kant) - zo gemaakt dat de draad naar het gemarkeerde net op de pcb gaat, dan is er de plaats voor de plaatweerstand (gemarkeerd met R7) en de trapkoppeling kap kan worden gesoldeerd in een van de "reserve" netten2 - is grid1 (witte lijn gemarkeerd met 2) - koppeldop of roosterstop kan indien nodig rechtstreeks op de soldeerlip van de socket worden gemonteerd - R1 is getekend als een roosterlek weerstand - R1-pad naar aarde kan ook worden gebruikt om de afscherming van de afgeschermde kabel aan te sluiten3 - is kathode1 (witte lijn gemarkeerd met 3) - zo ontworpen dat er een kathodeweerstand en een bypass-kap op het aansluitpunt en in het aardingspad zijn gesoldeerd aan het andere uiteinde zijn 4 en 5 niet gemarkeerd, 9 is gemarkeerd maar heeft geen speciaal net - 4, 5 en 9 zijn verwarmingspinnen - als een groot voorstander van DC-verwarming, sluit ik altijd alleen 4 en 5 aan in mijn dubbele triodes en suplly 12, 6V - draden voor verwarming gaan rechtstreeks naar de soldeerbouten van de socket, maar passeren twee grote pads als een vorm van spanningsreli ef6 - is plaat2 - dezelfde functie als 1 - is gemaakt om een draad naar het speciale net te laten gaan, dan is er R9 als plaatweerstand en je kunt een van de "reserve" netten gebruiken om de fasekoppelingscondensator vast te maken7 - is raster2 - dezelfde functie als pin2, maar in plaats daarvan is R8 getekend als plaats voor roosterlekweerstand8 - is kathode2 - dezelfde functie als pin3(9 - is centrale aftakking van de verwarming in dubbele triode-opstelling, in sommige novale buizen met de andere functie. Meestal laat ik deze pin weg of breek ik zelfs de soldeerlip van de socket)
Van de Alembic heb ik de gewoonte gekregen om een vermogensfiltercondensator toe te voegen als onderdeel van het circuit, dus ik heb hiervoor een aantal grote pads toegevoegd die zijn verbonden met zowel aarde als B+ aan de oostelijke rand..
Stap 2: Toonstapel-PCB
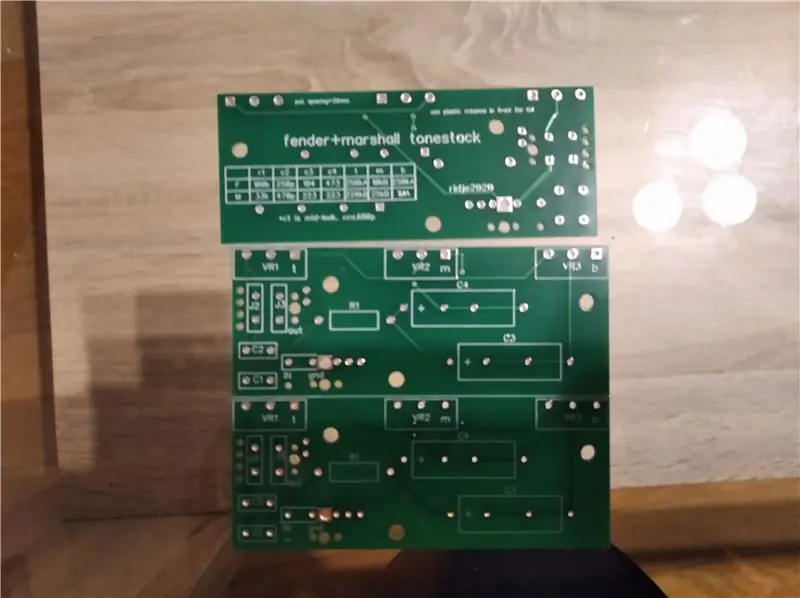
In de schema's van de meeste buizengitaarversterkers zie je dat "tone stacks" behoorlijk op elkaar lijken. Afhankelijk van de uitgangsimpedantie van de vorige trap zijn er twee hoofdontwerpen (met kleine variaties, bekend als Fender en Marshall). Ik heb ze beide gecombineerd in één PCB. Ik heb ook de meest voorkomende waarden van de gebruikte elementen in zeefdruktabel op de onderste laag geschreven. (De reden dat ik een aparte print voor de tone-stack heb ontworpen, is dat alle andere voorversterkerdelen rond de buis zijn verzameld, maar de tone-stack rond de potentiometers is gemaakt. Uit mijn ervaring is er een behoorlijke mogelijkheid om de bedrading in dit deel van de schakeling. Elementen die worden gebruikt in de toonstapel van buizen zijn hoogspanning en hebben daarom de neiging om te groot te zijn om praktisch op de potsoldeerlippen te worden bevestigd. Ook omdat het een hoge spanning is, voel ik me niet moedig om ze tegen de (geleidende) voorplaat te laten bungelen Aan de andere kant brengt het samen met andere voorversterkerelementen rond de buis lange stukken onnodige bedrading met zich mee. PCB is gemaakt voor PCB-montage potentiometers - sommige puristen zijn daar tegen, maar deze print is zo klein en licht dat er geen kans is om te draaien de potten zouden de verbinding omhoog schroeven. Voor de bangeriken zijn er drie montagegaten voorzien. De kleinere niet-geplateerde gaten op de print zijn bedoeld als trekontlasting voor de draden. R1, C1, C3 en C4, samen met de potten VR1-3 zijn gewone onderdelen van het circuit, potten op TMB-manier gerangschikt. Er is geen volumepotplaats - ik was beperkt tot 10 cm breedte tot het bord om het tegen de verkoopprijs te krijgen … En volumepot is niet altijd direct na de toonstapel - er is J3 om het aan te sluiten, noord het signaal, zuid de grond. C2 is er om C1 te overbruggen met extra capaciteit, waardoor de middentonen wat hoger worden - het kan op de J2 worden geschakeld. Het grote vierkante pad in het grondnet is er om verbinding met het invoerscherm mogelijk te maken
Stap 3: Schakel kop-PCB
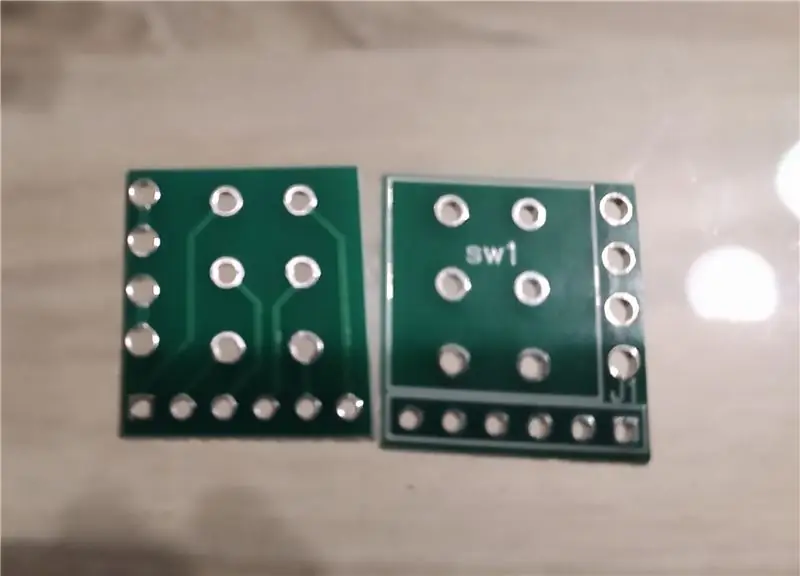
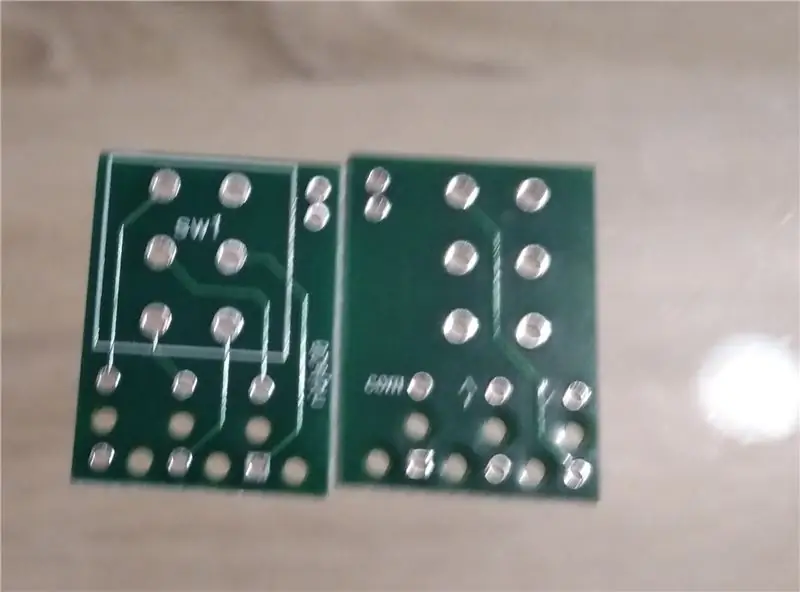
Ik geloof niet dat ik ooit een enkel elektronisch element heb gebakken met soldeerwarmte, en iedereen waarschuwt er zoveel voor. IC's, transistors, diodes enzovoort kunnen behoorlijk wat thermisch misbruik vergen voordat ze stoppen. Met uitzondering van schakelaars en potmeters (plastic Piher exemplaren). De draad plakt niet goed, je legt je soldeerbout nog een keer op de nok… en de nok beweegt op zijn plaats, je hebt er zacht plastic omheen gesmolten. De kans is groot dat de schakelaar vroeg of laat gaat plakken en barsten. Met alle elementen, waarvoor het het meest praktisch is om ze rechtstreeks op de schakelaar te laten solderen (vergeet niet om een onderdeel in serie met de schakelaar te solderen), is de kans veel groter dat u het verpest. Of maak een rommelig nest op zijn nokken. Het volgende probleem is draadspanning - u voltooit uw project, plaatst alle draden in een mooie scherpe volgorde en grijpt dan per ongeluk aan een van de schakeldraden en deze breekt - adieu inspanningen van het laatste uur, u moet hem uit de voorkant schroeven plaat (of een pedaal) en soldeer de draden opnieuw. Soms is het praktisch om een gewone connector op een schakelaar te gebruiken, en niet elke keer dat hij moet worden verwijderd, los te solderen. En als er overmatige kracht op de draad wordt uitgeoefend, breekt deze niet, maar laat de connector los - en u sluit hem gewoon weer aan.
Dus in plaats van een soldeerlipschakelaar gebruik je een PCB-montage. Je kunt alle draden op hun plaats solderen en ook schakelaarpinnen solderen zonder bang te zijn dat je de schakelaar vernietigt. De verbinding is aangebracht in de vorm van een bekende kop van 2,54 mm met één rij - u kunt deze gebruiken om interne verbindingen te maken of een connector te installeren. Er zijn vier grote geplateerde doorgaande gaten, die kunnen worden gebruikt als trekontlasting voor de inkomende draad of om extra benodigde verbindingen te maken.
Er zijn twee varianten van deze print, laag- en hoogspanning. HV is niet gemaakt met het 2,54 mm-patroon, omdat dit de vereiste gestandaardiseerde kruip- / isolatieafstand schendt. Ik heb die PCB's besteld om alleen te scoren, niet te knippen, zodat ik moeiteloos hele rijen of kolommen kan maken als het gebruik van meer schakelaars gewenst is. Gemaakt voor de (meest gebruikte) DPDT schakelaar.
Stap 4: TB Stompswitch-printplaat
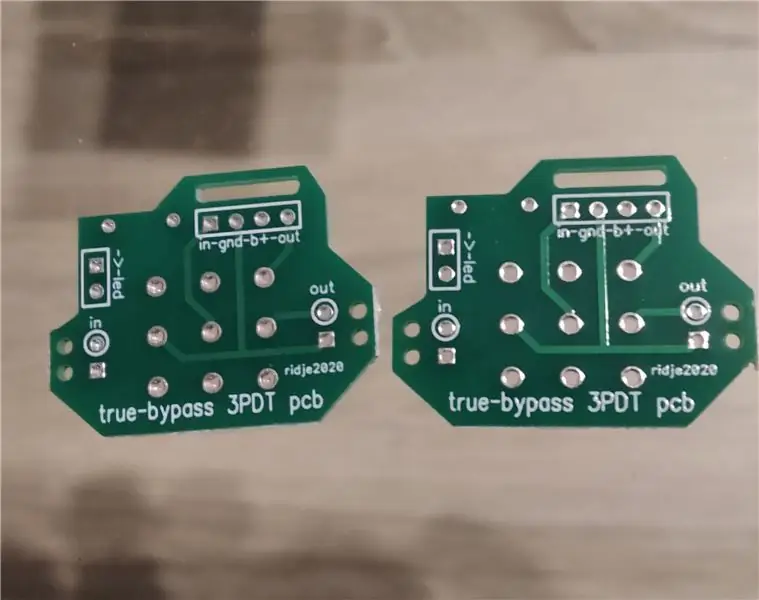
Ik weet dat niemand stompschakelaars gebruikt bij het bouwen van buizenversterkers, maar deze PCB zat in dezelfde batch - en maakte deel uit van dezelfde mentaliteit. Laten we zeggen een upgrade van de vorige DPDT-switch scherts. Het is gewoon mijn weergave van de kleine PCB die elke verkoper van pedaalkits aanbiedt voor een misselijkmakende prijs.
Als bedradingsschakelaars over het algemeen hinderlijk kunnen zijn, is het twee keer zo vervelend om een 3PDT-stompschakelaar netjes te bedraden voor true bypass. Het kan evenveel tijd kosten om het hele pedaalcircuit te solderen als voor het maken van de aansluitingen en de bedrading van de stompschakelaar. En het is elke keer dezelfde pasta, niet het leuke avontuur van het maken van een nieuw circuit.
Deze PCB beschikt over: - pads voor een PCB-montage 3PDT stompswitch - gescheiden in en uit jack-verbindingspads met trekontlastingsgaten - de jacks worden eindelijk netjes bedraad en de draad zal niet afbreken, zelfs niet nadat het circuit voor de 10e keer is verwijderd de behuizing - 4-draads enkele lijn 2,54 mm pin header pads. Hiermee kunt u een connector aan de ene of andere kant van de verbinding met de hoofdeffectprint plaatsen. De trekontlasting is hier één grote rechthoek omdat ik voor deze verbinding graag lintkabel gebruik. De pinout (I-gnd-B+-O) past bij mijn standaard pinout bij het maken van pedalen vanaf nul. - voorwaarde voor LED-druppelweerstand en LED om die verbindingen niet tot een ongezonde puinhoop te maken die in uw pedaalbehuizing hangt - nul afstand tot de omtrek van de schakelaar aan de zuidrand zodat u de schakelaar zo dicht mogelijk bij de muur van de behuizing kunt monteren - om te geven plaats andere belangrijke segmenten.
Stap 5: Ik wil ze ook maken …
Google me voor gerbers of PCB's als je ze nodig hebt.
---
Degenen die om de schema's vragen, begrijpen het concept van die PCB's zeker niet. Ze zijn gemaakt om universeel, multi-toepasbaar of hoe je het ook noemt te zijn. Je neemt het schema dat je wilt gebruiken, analyseert het en kiest vervolgens welk element waar in mijn bord komt om het optimaal te maken. Je vraagt niet waar je je sokken moet laten als je de la koopt.
Aanbevolen:
Handleiding voor het bouwen van een computer: 8 stappen
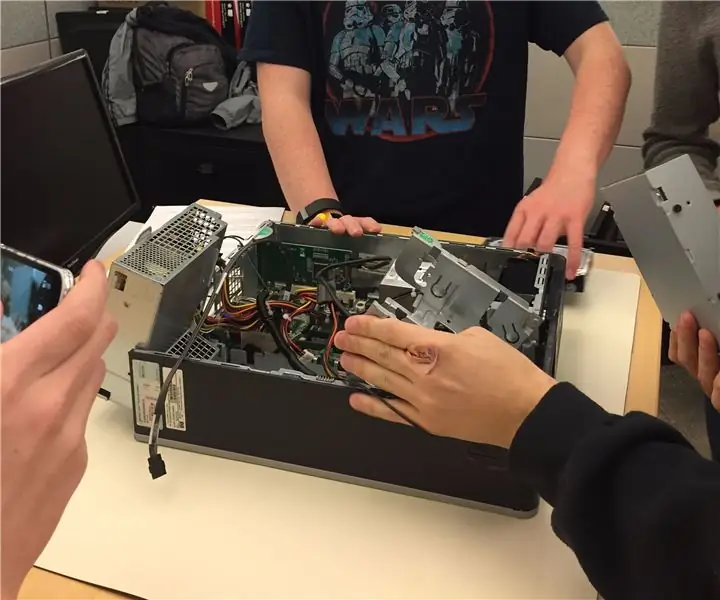
Handleiding voor het bouwen van een computer: dit is een instructiegids over hoe iemand zijn eigen, aangepaste personal computer zou bouwen. Hoewel sommigen misschien denken dat het gewoon goedkoper en handiger is om een vooraf gebouwde pc te kopen, zouden de meeste gebruikers merken dat het eigenlijk minder duur is om t
Instructies voor het bouwen van een computer: 12 stappen
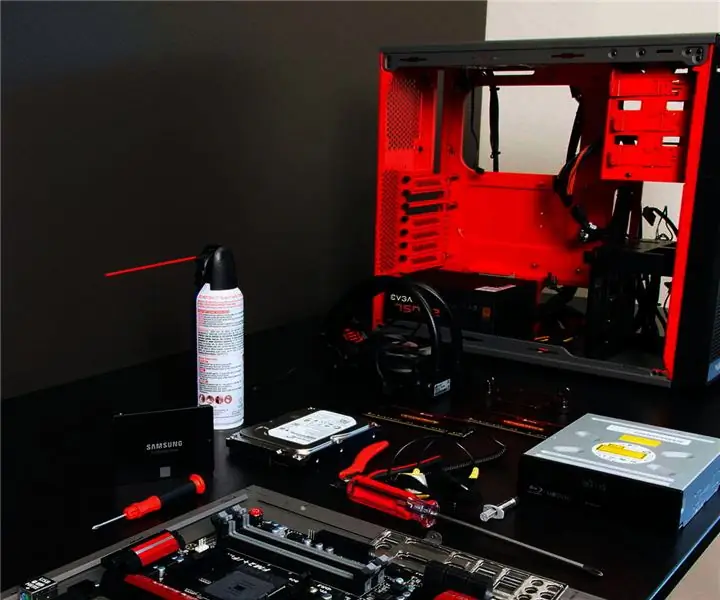
Instructies voor het bouwen van een computer: Welkom, zo bouw je een computer in 12 stappen. De reden dat u uw eigen computer moet bouwen, is om te leren hoe het werkt, zodat u kunt leren hoe u het kunt repareren
[HASS.IO] Begin met het bouwen van uw Smart Home zonder codering, voor minder dan $ 100: 6 stappen
![[HASS.IO] Begin met het bouwen van uw Smart Home zonder codering, voor minder dan $ 100: 6 stappen [HASS.IO] Begin met het bouwen van uw Smart Home zonder codering, voor minder dan $ 100: 6 stappen](https://i.howwhatproduce.com/images/003/image-8860-20-j.webp)
[HASS.IO] Begin met het bouwen van je slimme huis zonder codering, voor minder dan $ 100: de laatste tijd ben ik aan het rommelen en heb ik met succes mijn huis minder "idioot" gemaakt. Dus ik ga delen hoe je een smart home-systeem maakt met een laag prijskaartje, hoge compatibiliteit dat naadloos en stabiel zou werken
Hoe een USB-kabel voor de universele PCB te bouwen: 11 stappen
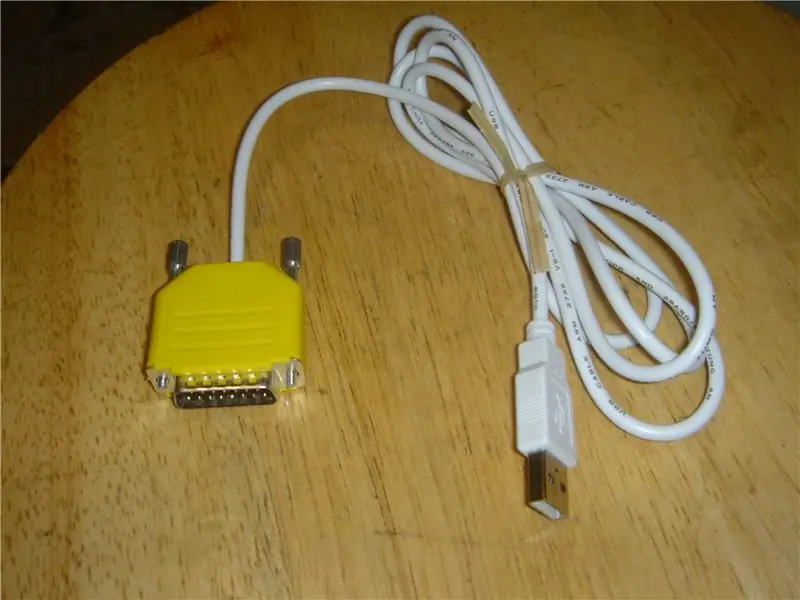
Hoe maak je een USB-kabel voor de universele PCB: Het Universal PCB-project (kortweg UPCB) is gestart om een enkele gamecontroller, met name vechtsticks, op zoveel mogelijk verschillende consoles mogelijk te maken. Informatie over het project is te vinden in de volgende thread op Shoryuken.com
Instructies voor het voltooien van de mock-up van het ontwerp van de rupsschuif voor het heffen/verlagen van in het midden gemonteerde voetsteunen op elektrische rolstoelen - Ajarn
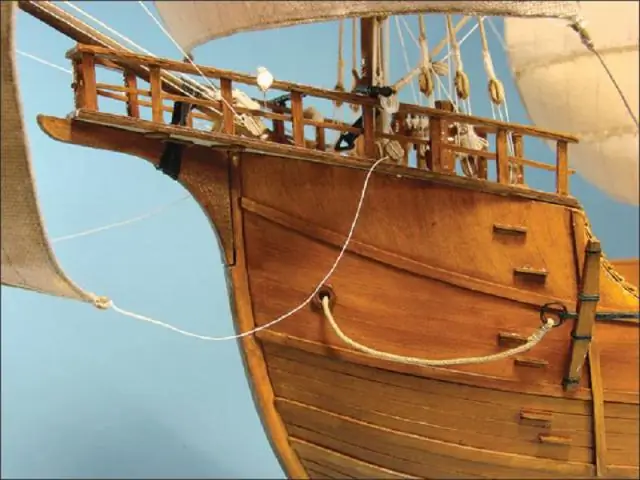
Instructies voor het voltooien van de mock-up van het ontwerp van de rupsschuif voor het omhoog/omlaag brengen van in het midden gemonteerde voetsteunen op elektrische rolstoelen: in het midden gemonteerde voetsteunen kunnen omhoog worden gebracht om onder de zitting goed te worden opgeborgen en omlaag om te worden ingezet. Een mechanisme voor onafhankelijke bediening van het opbergen en plaatsen van de voetsteun is niet inbegrepen in elektrische rolstoelen op de markt, en PWC-gebruikers hebben de behoefte geuit