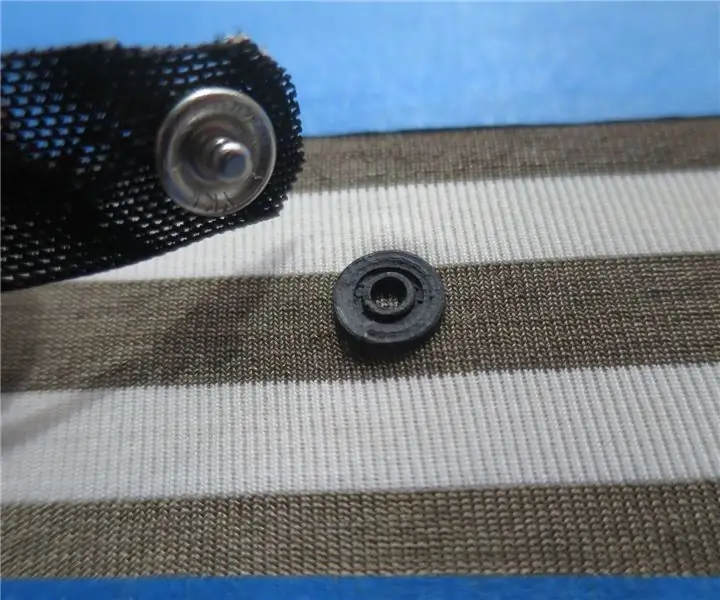
Inhoudsopgave:
- Stap 1: Fusion360-bestanden
- Stap 2: Test afdrukken en instellen
- Stap 3: 3D-printen op een geleidend weefselspoor
- Stap 4: Geleidbaarheid testen
- Stap 5: Afdrukken op verschillende oppervlakken
- Stap 6: Test meerdere afdrukken
- Stap 7: Weerstand lezen
- Stap 8: Snaps opnieuw bevestigen met geleidende epoxy
- Stap 9: Conclusie en volgende stappen
2025 Auteur: John Day | [email protected]. Laatst gewijzigd: 2025-01-23 15:01
Door rachelfreirewww.rachelfreire.comVolg meer van de auteur:
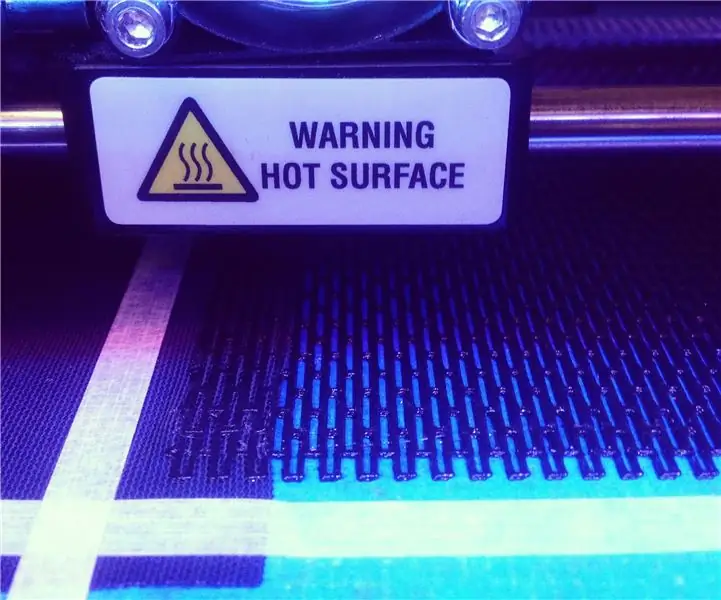
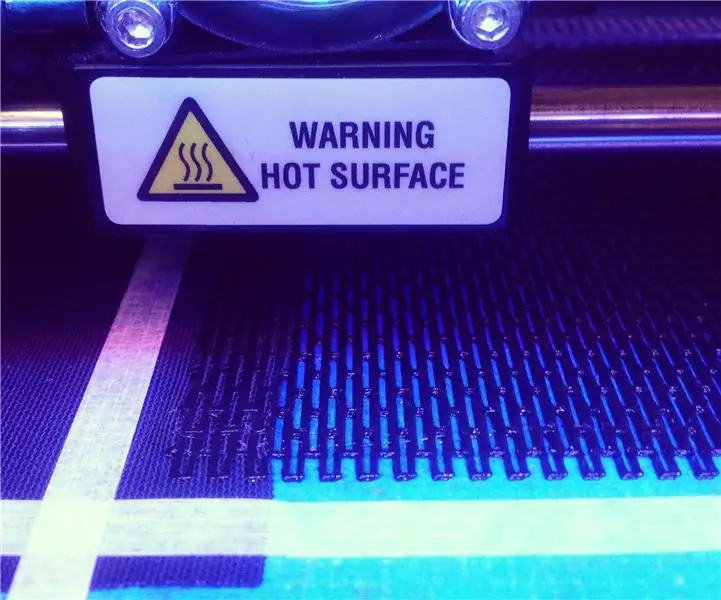
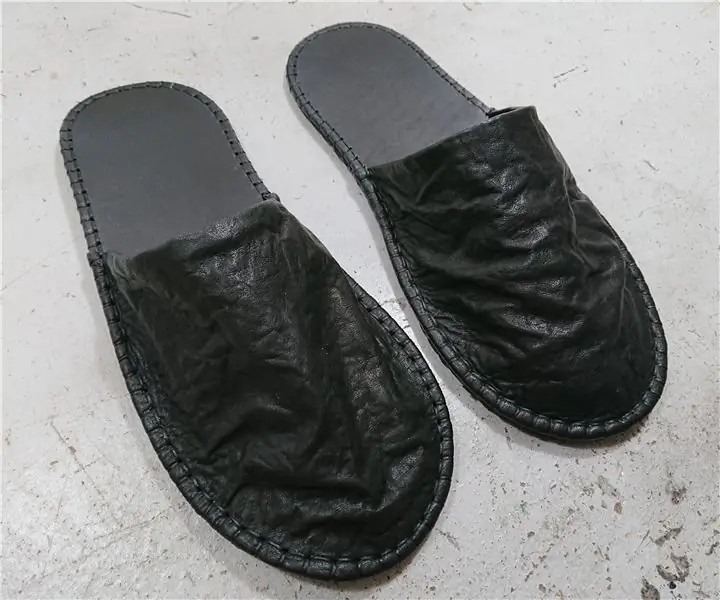
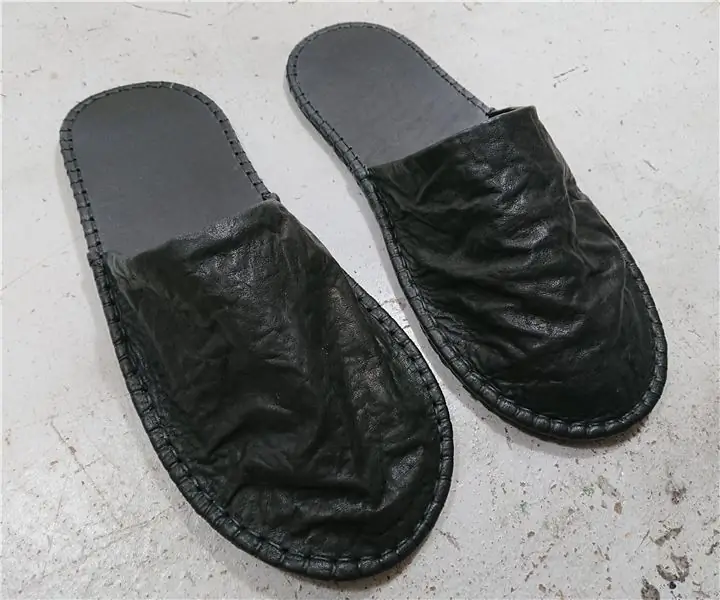
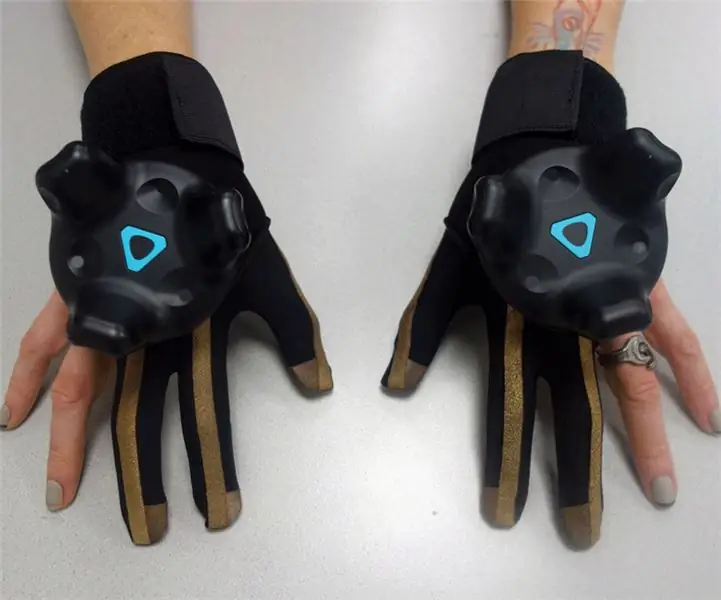
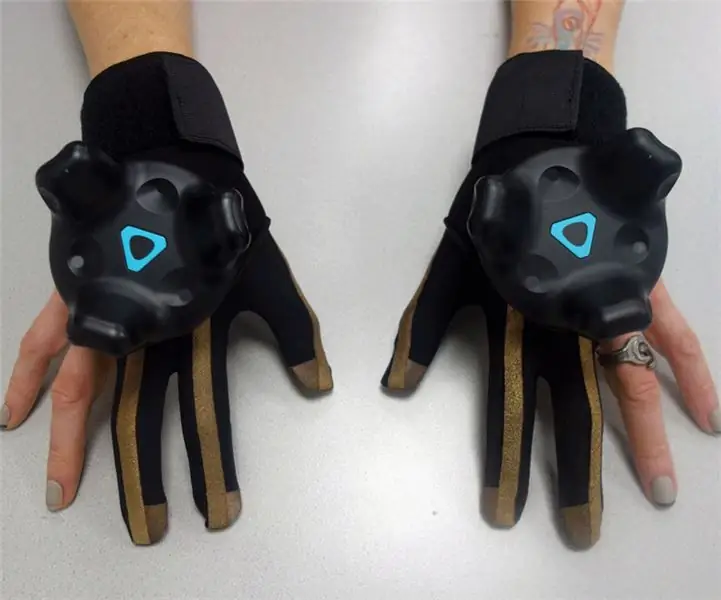
Over: designer, leren ninja, tech explorer, ruïneer van manicures Meer over rachelfreire »
Dit instructable documenteert mijn eerste poging om geleidende snaps op stof 3D te printen. Ik wilde een vrouwelijke snap 3D printen die zou aansluiten op een gewone metalen mannelijke snap.
Het bestand is gemodelleerd in Fusion360 en afgedrukt op een Makerbot Rep2 en een Dremel met behulp van Black Magic 3D geleidend grafeen PLA.
De snaps zijn YKK 'Snapet' open prong snaps (maat 12L) en hebben een diameter van 7,5 mm. Ze worden vaak gebruikt door eTextiles-beoefenaars omdat ze de kleinste zijn die beschikbaar zijn. Je kunt ze in verschillende maten kopen bij verschillende leveranciers, maar ze lijken een gestandaardiseerd ontwerp te zijn. Koop hier maat 12.
Mijn doel is om manieren te onderzoeken om een kledingstuk te maken dat geleidend en rekbaar is en bij voorkeur geen hardmetalen onderdelen gebruikt. Door connectoren te maken die compatibel zijn met bestaande verkrijgbare snaps, wordt het gemakkelijker om te testen en te herhalen.
Deze test werkte verrassend goed en het bestand is het waard om af te drukken, maar er moet zeker nog veel aan worden aangepast. Voorlopig kan het worden afgedrukt en getest zoals het is, maar het is zeker een proof of concept in plaats van een volledig functionerende module die betrouwbaar kan worden afgedrukt, b.v. het PLA heeft de neiging te krimpen en de drukknopen hebben een beperkte levensduur.
Als je dit bestand afdrukt, laat dan een reactie achter en vertel me je bevindingen!!
Meer afbeeldingen hier:
Deze verkenningen maken deel uit van een groter project genaamd Second Skin, een prototyping-pak voor eTextiles. Ik zal alle bestanden, patronen en documentatie uploaden zodra ze zijn voltooid. Je kunt het project hier volgen, of via mijn website:
Bekijk ook eens Rewear van Lara Grant. Ze heeft gewerkt aan een modulair systeem voor wearables op basis van een breadboard van 3D-drukknopen op stof. Ze heeft ook een focus op de duurzaamheid van deze technieken, iets wat ik ook als een integraal onderdeel van hun toekomstige ontwikkeling zie. We zullen onze experimenten binnenkort integreren in een speciale website voor etextile connectoren, dus zorg ervoor dat je ook een kijkje neemt op Lara's website en Instructables!
Stap 1: Fusion360-bestanden
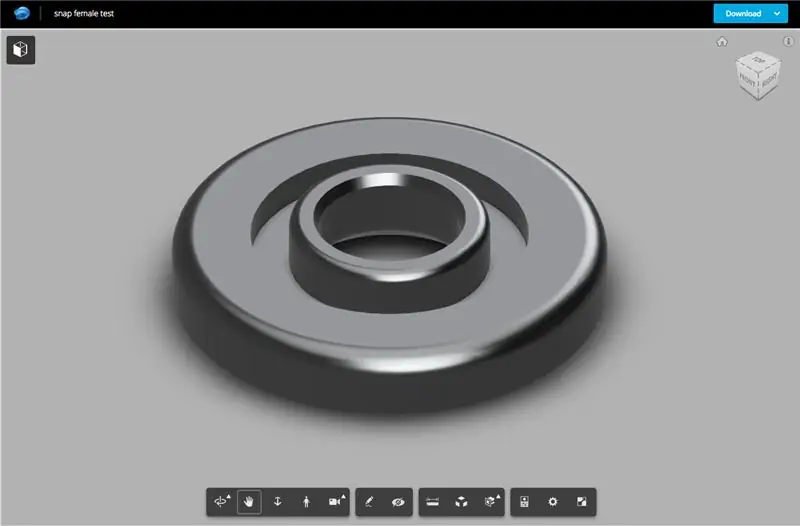
Het bestand was vrij snel gemodelleerd met Fusion360.
Ik nam zoveel mogelijk metingen van een bestaande module en maakte een ruw ontwerp. Omdat de snap zo klein is, zijn sommige van de binnenste proporties gemaakt met giswerk en daarom moet er meer worden gespeeld.
Link om de huidige versie hier te downloaden:
Het bestand dat aan deze Instructable is gekoppeld, was mijn eerste poging. Het werkte best goed. Het gekoppelde bestand (hierboven) is aangepast, waardoor de basis van de module steviger is geworden. het idee is dat het zou helpen om beter aan de stof te blijven plakken. Hoewel dit enigszins hielp, zijn beide bestanden nog steeds het testen waard als je een versie hiervan wilt afdrukken. Met beide had ik succes en mislukkingen.
Ik zal er ook op wijzen dat ik een totale Fusion-beginner ben en hulp van ninja's heb gehad bij het aanpassen van het bestand van JON-A-TRON. Je moet zijn lessen in 3D-printen helemaal bekijken!
Als je grotere snaps wilt gebruiken (zoals 15 mm die vaker voorkomen), zou ik verwachten dat dit bestand kan worden verkleind en afgedrukt met de juiste afmetingen en dat het ook op grotere versies van dit snap-ontwerp zal klikken. Ik heb dit nog niet geprobeerd omdat ik probeer alles zo klein mogelijk te maken.
Deze metalen snapets zijn geweldig, maar vaak zijn de dobbelstenen moeilijk te vinden. Ik gebruik de Prym-variotang voor het met de hand aanbrengen van snaps en het is moeilijk om de snap-die te vinden die past. Dus maakte ik een afdrukbaar fusiebestand voor de 12L Snapets;) Nogmaals, het is niet perfect omdat 3D-prints de neiging hebben te krimpen en kromtrekken en uiteindelijk breken. Maar ik heb net nieuwe geprint als dit gebeurt! Vijlen zijn bijgevoegd voor de binnen (verbindingsdeel) en buiten (ringbevestiging) matrijs. De een is een fractie groter dan de ander. Gebruik je ze verkeerd om, dan blijft de snap in de dobbelsteen steken.
Stap 2: Test afdrukken en instellen
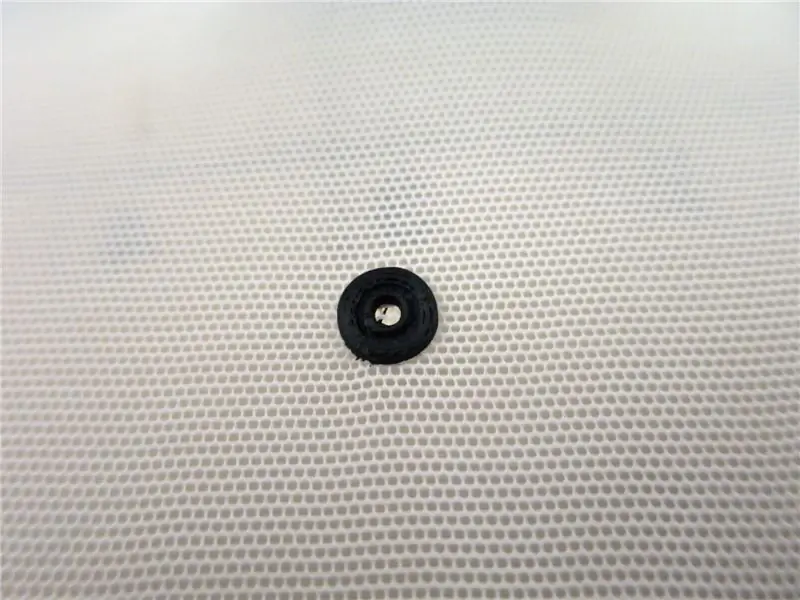
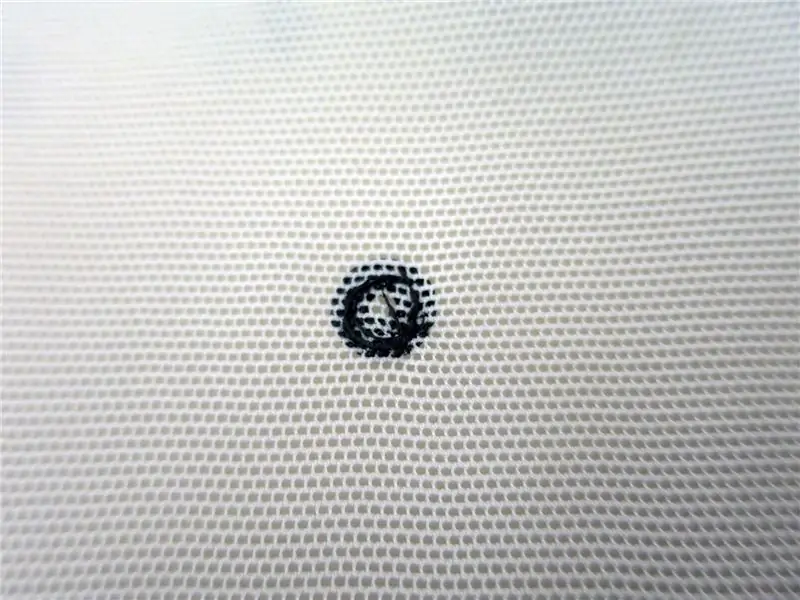
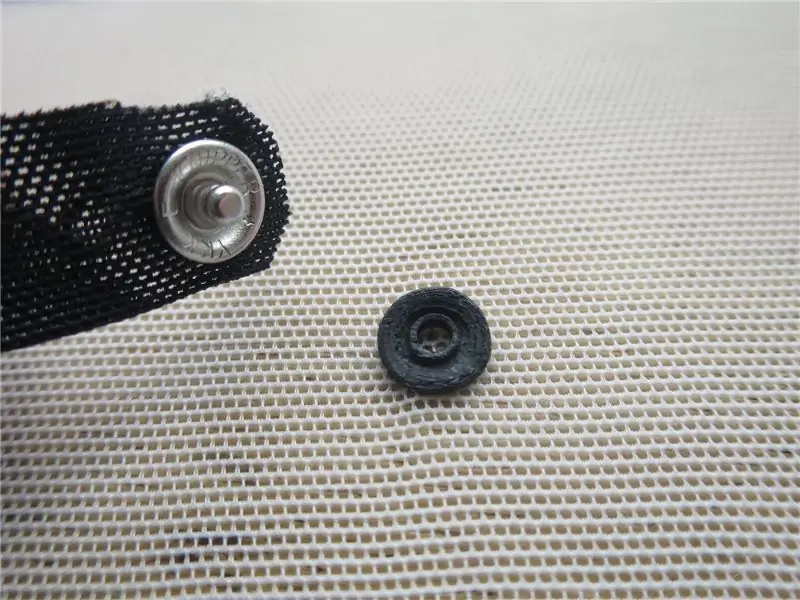
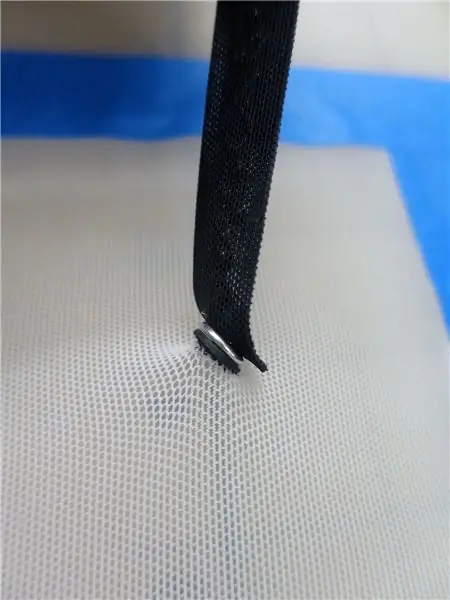
Deze eerste snap is gedrukt door Lara Grant. Ze werkt aan een soortgelijk project om een snap-stof te maken en heeft een geweldige Instructable over 3D-printen op stof. Bekijk ook eens haar wearables lessen
Het is Black Magic 3D grafeenfilament en is geprint op een Makerbot Rep 2 met de printtemperatuur en extruder ingesteld op 220 °
We hebben allebei een techniek getest waarbij je een basislaag van filament print, de machine pauzeert om stof in te voegen en dan verder gaat met printen. Dit betekent dat het filament rond de stof zal smelten en een afdichting zal creëren. Je kunt dit zien in de tweede afbeelding; er zit filament aan de onderkant van de stof. Deze laag werd eerst op het bed gedrukt, daarna werd de printer gepauzeerd en werd de stof ingebracht. De printer werd vervolgens weer onderbroken en het afdrukken ging door.
Het werkte wonderbaarlijk! Eerste poging met het bestand dat ik 10 minuten eerder had gemaakt.. En het brak zelfs heel goed!
Deze module die je hier ziet, is op powernet gedrukt. Het is een materiaal dat ik veel gebruik en gebruik voor het gerelateerde project Second Skin dat gebruik maakt van stretchcircuits. Het is 4-way stretch en wordt gebruikt voor lingerie en danskleding. Het werkt goed omdat het een fijn synthetisch gaas is. Het is meestal gemaakt van polyamide, zodat het filament het oppervlak smelt en er goed aan hecht. Het filament kan ook in en rond het oppervlak van het microfijne gaas zelf smelten.
Powernet heeft een goede treksterkte en als het met tape wordt gespannen wanneer je het op het bed legt, blijft het niet haken door de extruder.
Stap 3: 3D-printen op een geleidend weefselspoor
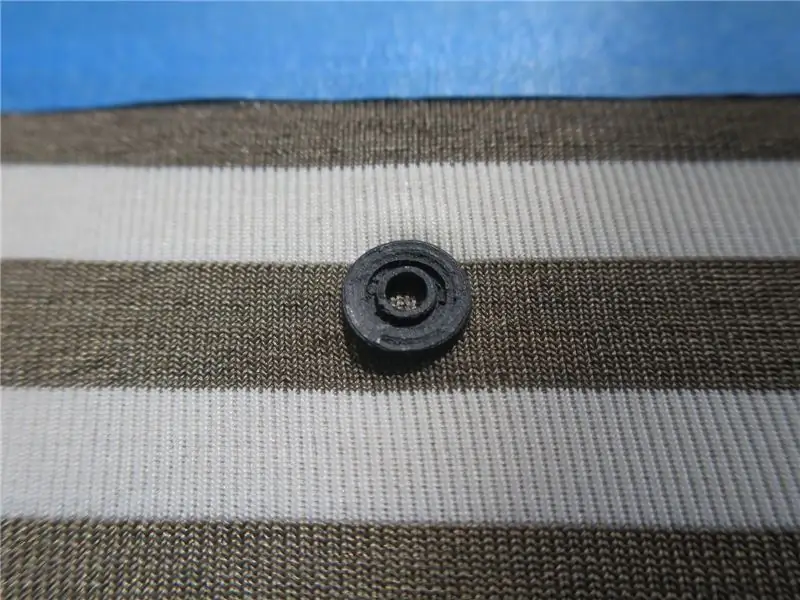
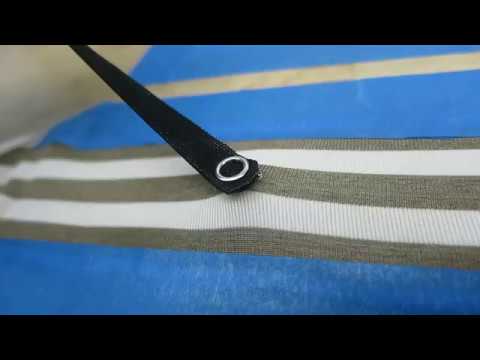
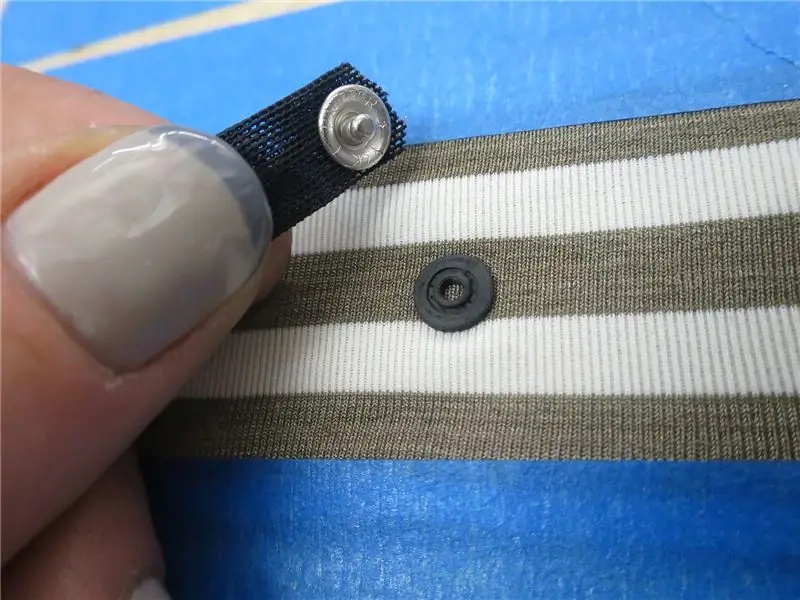
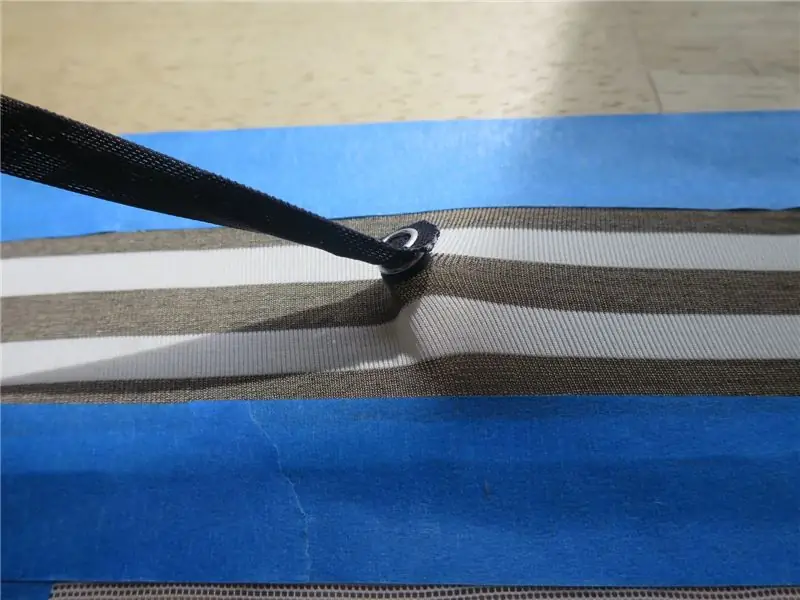
Deze briljante stof is een stretch jersey gebreid met geleidende sporen. Ik geloof dat het de tovenarij is van Hannah Perner-Wilson en Mika Satomi van Kobakant en op maat is gemaakt. Ik kreeg er wat van tijdens het zomerkamp van eTextiles en we besloten dat dit een goede zaak zou zijn om de elektrische verbinding tussen stof en print te testen.
Het is jerseystof en het lijkt alsof de vezels zijn gecoat voordat ze werden geweven, in plaats van dat de geleidende coating na de fabricage wordt bedrukt. Het is te dik om door het oppervlak te printen (zoals in de eerdere test) omdat het filament niet op dezelfde manier zou aansluiten als door de gaten in het powernet.
We hebben de Makerbot ingesteld om recht op de stof af te drukken. wat je hierboven ziet is de eerste proefafdruk op dit materiaal.
Veel verschillende mensen hebben 3D-printen op stof getest en het lijkt te verschillen afhankelijk van de aard van de print, de gebruikte materialen en machines. De meeste successen lijken mazen te hebben, omdat het weefsel los is en het filament door de stof kan zakken om een binding te creëren.
Sommige mensen laten het mondstuk van de printer zakken. Dit slaat de extruder in de stof en dwingt filament in de vezels, maar kan het materiaal slepen. Een andere optie is om het startpunt van de extruder omhoog te brengen om de print te starten, wat betekent dat je de print zo snijdt dat deze net boven de dikte van de stof begint. Ik kan me voorstellen dat dit goed zou werken als je stof dik was. Omdat die van ons vrij dun en plat zijn, hebben we rechtstreeks op het materiaal geprint met de standaardinstellingen, waarbij we gewoon de vlotten en eventuele ondersteuning hebben uitgeschakeld.
Het werkte prachtig! Dit kan te wijten zijn aan verschillende factoren: - het oppervlak van deze specifieke stof was ideaal om de afdruk te laten hechten - de extruder was op dit moment toevallig op de perfecte temperatuur (dit filament kan erg inconsistent zijn) - de goden van 3D-printen waren in een goed humeur en we hadden super veel geluk
Het is duidelijk dat dit meer moet worden getest.
Stap 4: Geleidbaarheid testen

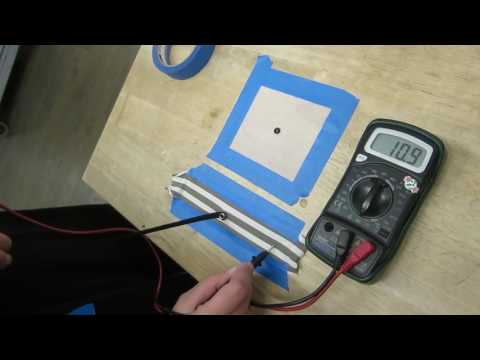
Deze test maakte gebruik van een stretch eTextile-connector gemaakt met geleidende Karl Grimm-draad. Binnen de zwarte connector is er een zigzag van geleidende draad geïsoleerd door stoflagen aan weerszijden. Elk uiteinde heeft een mannelijke snapet. Al deze materialen hebben een vrij lage weerstand.
De weerstand over de 30 cm connector, door de snap en over ongeveer 8 cm geleidende stof lijkt ongeveer 10 ohm te zijn. Dit was verrassend en leek behoorlijk stabiel te blijven, zelfs als het uitgerekt was. Ik weet niet zeker of dit een nauwkeurige en herhaalbare lezing is!
Stap 5: Afdrukken op verschillende oppervlakken
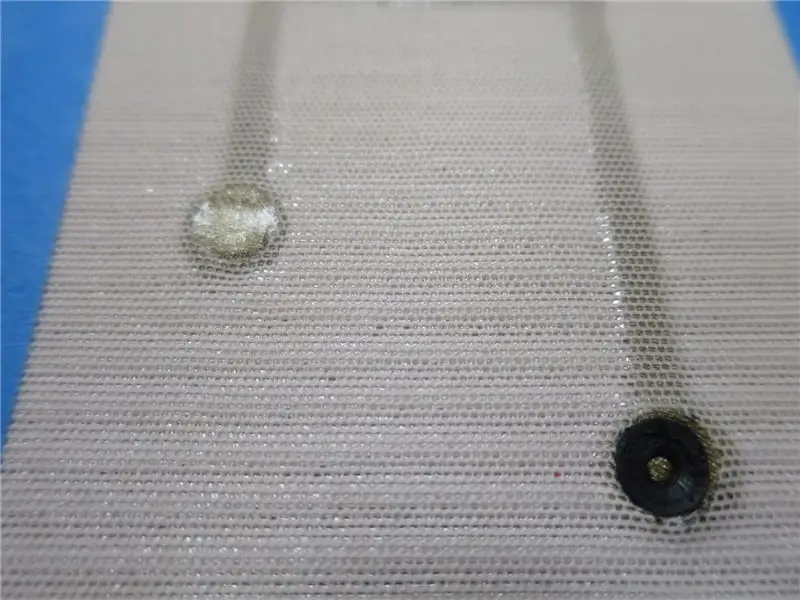
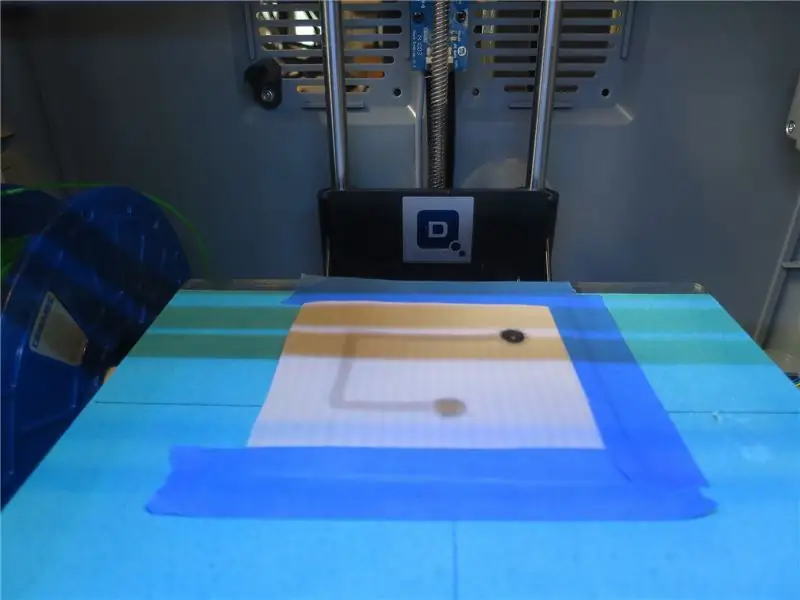
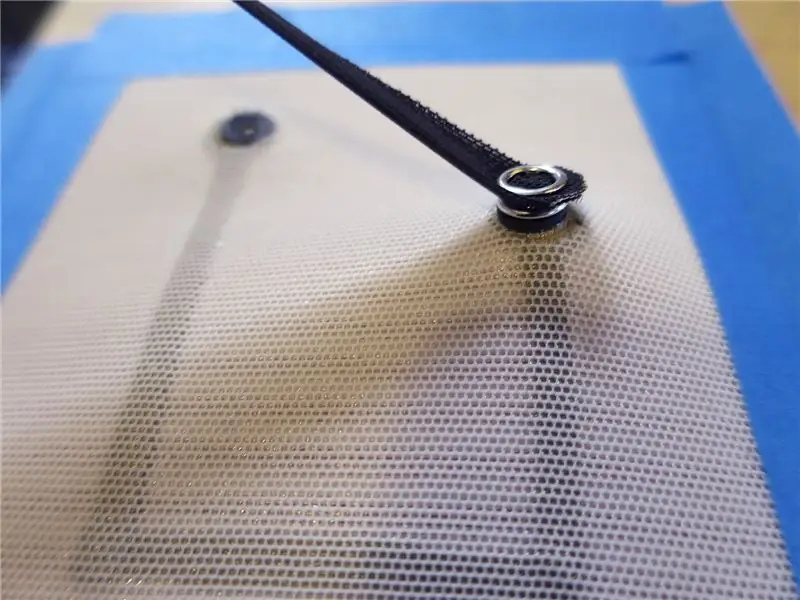
Vervolgens besloot ik om te proberen op een Dremel te printen. Dit komt vooral omdat de Makerbot een sissende fit had, maar afwisseling is altijd goed. Nogmaals, de printtemperatuur en extruder waren ingesteld op 220°
Ik heb gewerkt aan gebonden, geïsoleerde, rekbare geleidende sporen voor eTextiles. Deze stoffen maken gebruik van gebonden textiellagen met Bemis SewFree fusing, een superfijne warmtebindende film. Dit betekent dat de stofmonsters dikker waren dan de vorige tests. De geleidende sporen zijn geïsoleerd in de powernet-stof en hebben alleen de uiteinden als ronde kussens.
Toen ik het bestand voor het eerst afdrukte met de standaardinstellingen, sloeg het in het oppervlak van de stof en vervormde de afdruk. Het resultaat zie je op de eerste afbeelding. De snap werkte deze keer niet.
Jonathon liet me zien hoe je de vijl in Cura snijdt en de startpositie van de extruder met 0,4 mm verhoogt.
Voor de volgende test heb ik ook een laag SewFree bonding aangebracht op het oppervlak waarop ik zou gaan printen. Dit was om te zien of dit enig verschil maakte voor de hechting van de afdruk.
Het werkte aanvankelijk heel goed, zoals je kunt zien in de laatste afbeelding. Helaas, na een paar drukknopen, kwam de druk los van de stof en viel eraf.
Stap 6: Test meerdere afdrukken
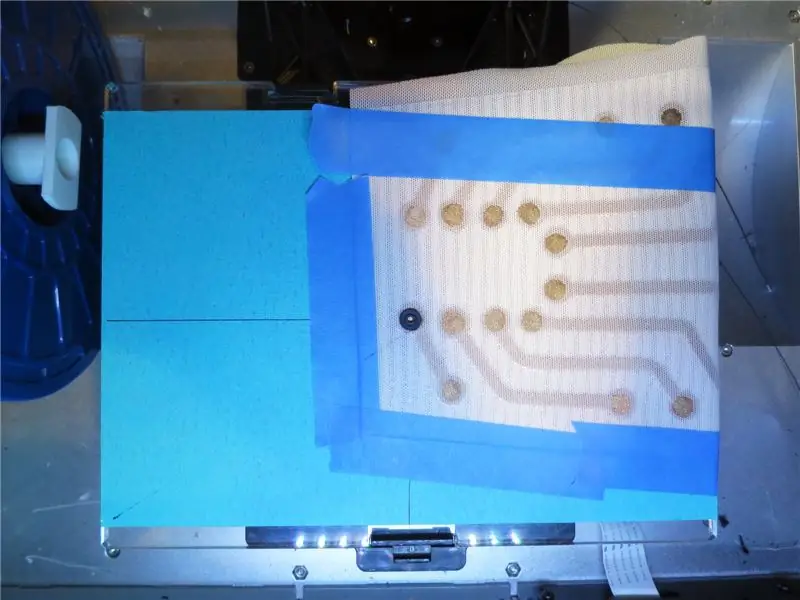
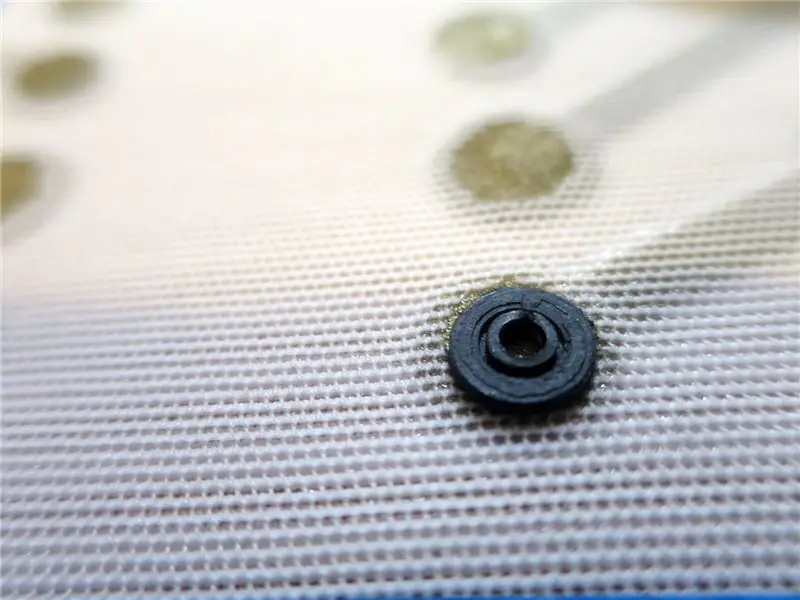
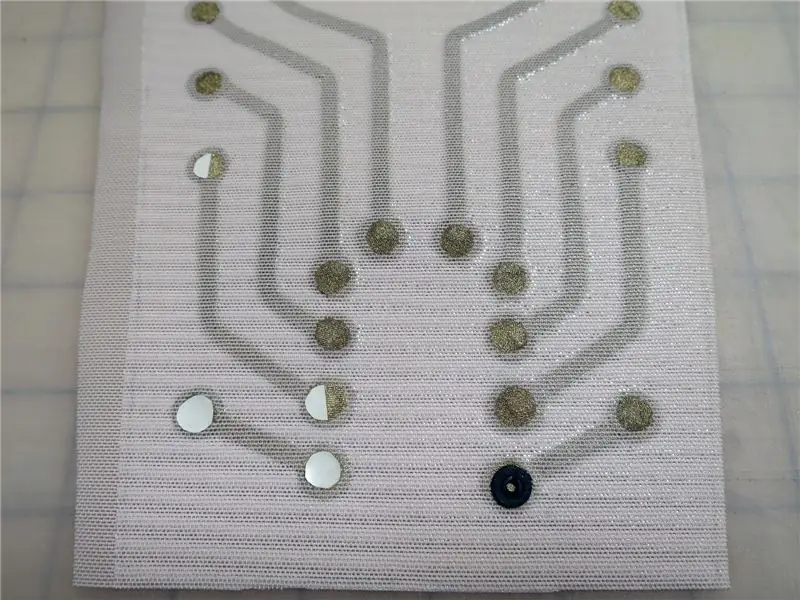
Vervolgens probeerde ik meerdere snaps af te drukken om te zien hoe de stroom door twee snaps aan beide uiteinden van een geleidend spoor stroomde. Omdat ik bij de vorige test maar één werkende snap had, kon ik het niet controleren. Misschien was de afdruk die Lara eerder had gemaakt een toevalstreffer. Ik heb een snel paneel gemaakt om meerdere afdrukken te proberen.
Omdat dit een test was, besloot ik dat ik elke module afzonderlijk zou afdrukken, in plaats van te proberen meerdere snaps op één stuk stof af te drukken.
Drie redenen: 1. Ik wilde geen tijd investeren in het maken van een lay-outbestand omdat het weefselcircuit waarop ik aan het printen was onnauwkeurig was gemaakt2. De prints mislukken vaak 3. Ik wilde niet dat malafide filament over de stof sleepte
Ik heb elke module uitgelijnd tot een gecentraliseerd punt en heb ze een voor een afgedrukt. Elk kwam perfect uit.
Ik heb SewFree fusing toegevoegd aan sommige geleidende pads. Je kunt dit in de afbeeldingen zien als witte cirkels en halve cirkels. Dit is de papieren achterkant die wordt afgepeld. Ik heb het erop gelaten zodat het beter te zien is op de afbeeldingen. Ik dacht dat het goed zou zijn om te zien hoe het samensmelten de hechting over dezelfde afdruk beïnvloedde. Ze bleken allemaal behoorlijk op elkaar te lijken. De meeste bleven hangen en een paar vielen eraf. Ik weet niet zeker waarom, maar ik neem aan dat het komt door minieme verschillen in de dikte van de stoflagen. Ze werden allemaal snel achter elkaar afgedrukt op dezelfde printer met dezelfde instellingen.
de weerstand over een geleidend spoor van 15 cm door twee resistieve drukknopen was ongeveer 50 ohm. Dit gebeurde direct na het printen en leek supergeleidend, dus we hadden meer tests nodig.
Stap 7: Weerstand lezen
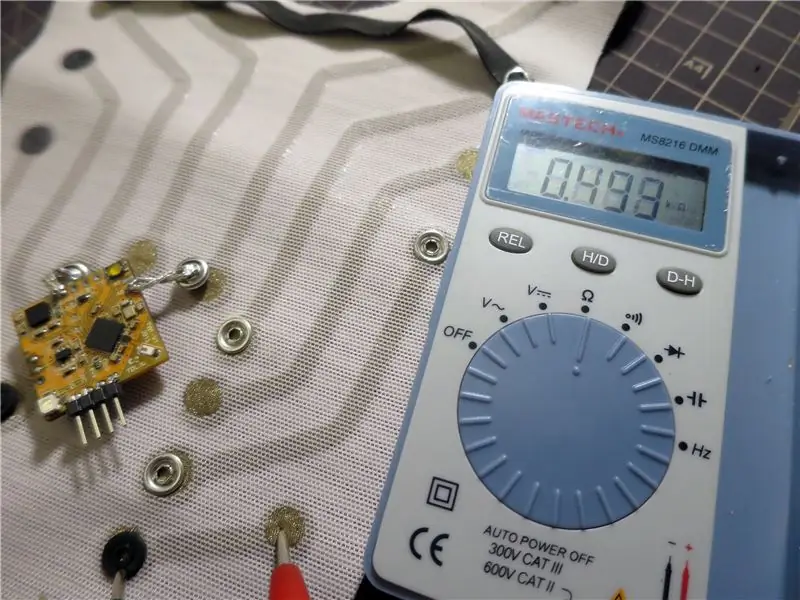
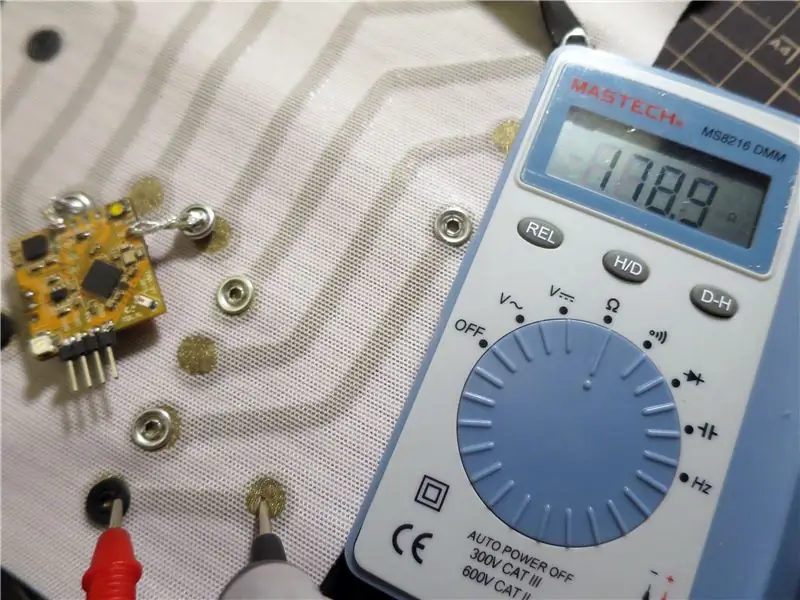
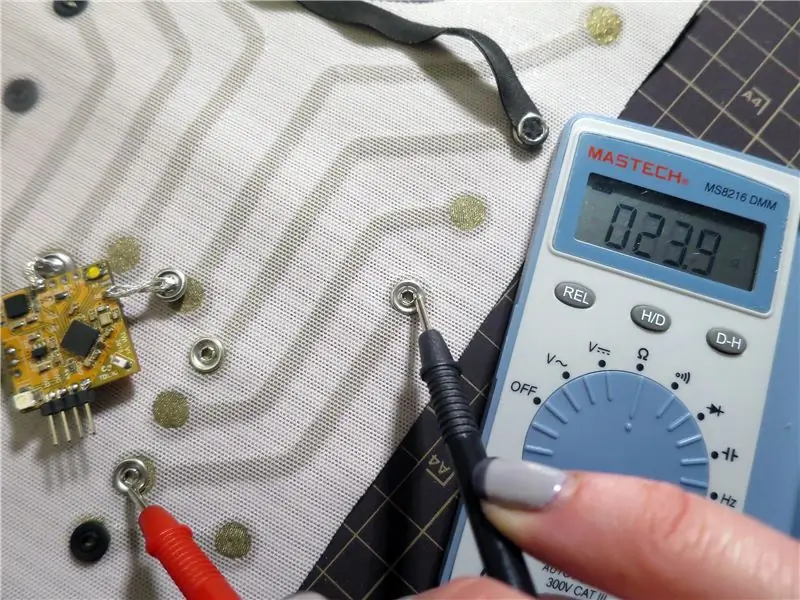
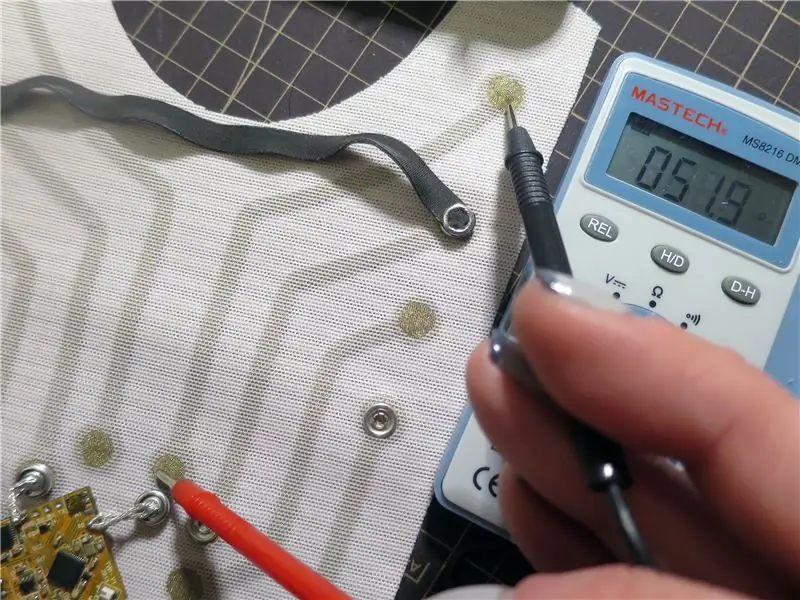
De metingen die ik van de snaps nam, leken veel te verschillen. Ook dit veranderde in de loop van de tijd.
Stap 8: Snaps opnieuw bevestigen met geleidende epoxy
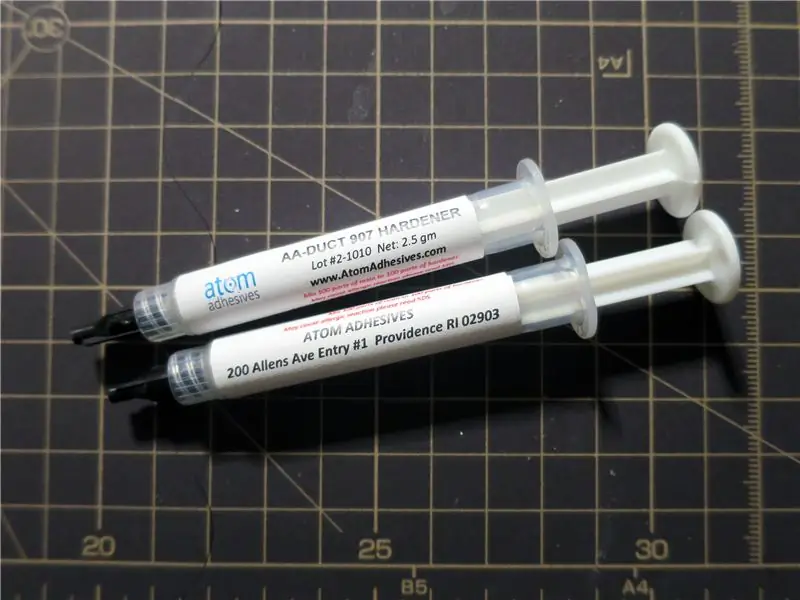
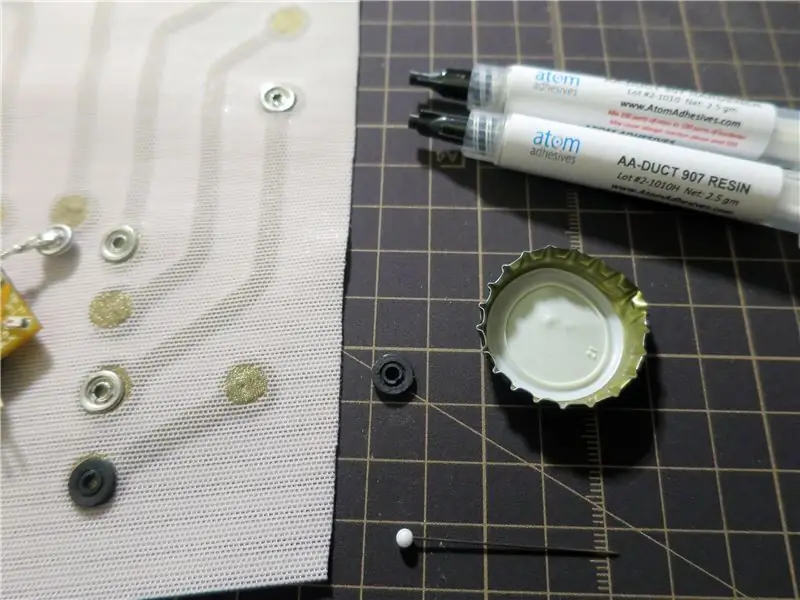
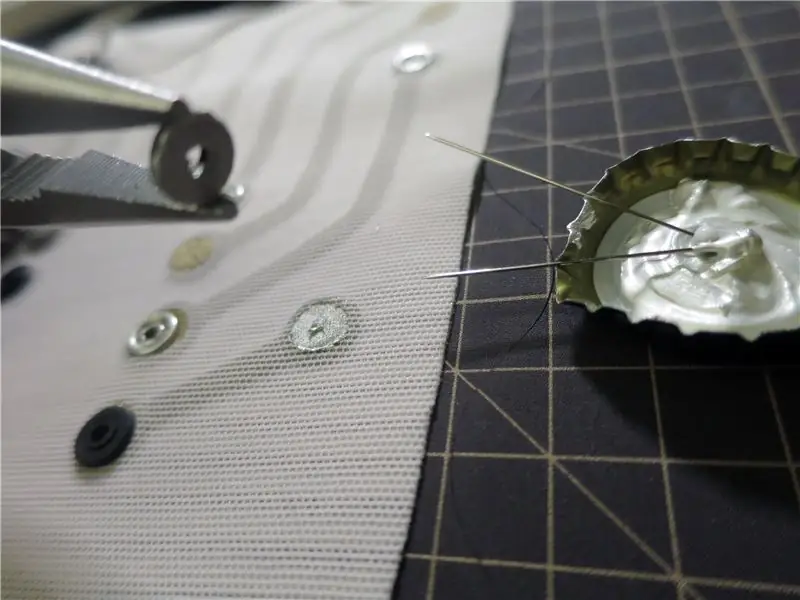
Sommige drukknopen vielen er na een beetje gebruik af. Ze hechtten niet zo goed aan het strak gebonden materiaal als bij de eerdere tests.
Op dit punt is het de moeite waard om een andere optie te onderzoeken: kunnen de drukknopen worden afgedrukt en daarna op de stof worden geplakt.
Het kan waar zijn dat drukkers op bepaalde stoffen kunnen worden gedrukt, maar op andere moeten worden gelijmd. Dit zou nog een werkbare optie kunnen zijn.
Ik heb geleidende epoxy gebruikt en twee van de drukknopen weer op hun plaats gelijmd om te zien of de lijm een hechting kan maken en betrouwbaar kan geleiden.
Helaas hechtte deze helemaal niet goed aan de stof. De epoxy is vrij kalkachtig en houdt niet van het dichte synthetische materiaal. Hoewel de lijm een kleine hoeveelheid stroom toestond, vielen de snaps er na één snap af.
Stap 9: Conclusie en volgende stappen
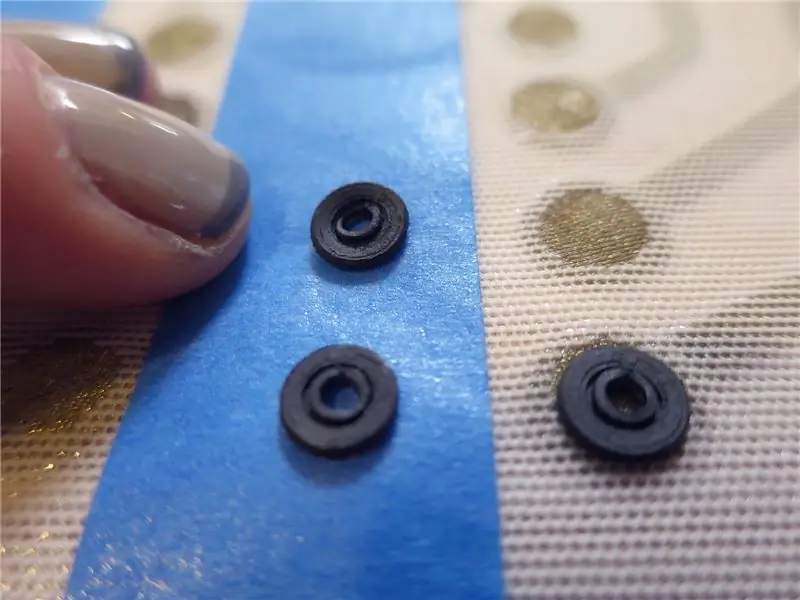
Dit snap-ontwerp werkte heel goed voor een eerste test. Hij klikt stevig vast, kan een kleine hoeveelheid stroom geleiden en is een goede proof of concept.
Helaas gaven ze geen consistente geleidbaarheid. Sommige waren ok en andere werkten helemaal niet. Het lijkt erop dat het gebruik van strak geweven stof een probleem is, dus dit werkt niet zo goed voor mijn gebonden stoffen. Het gebruik van meer open weefsel zoals de trui, en vooral het powernet, lijkt de beste optie. Het probleem daarmee is dat hoe minder dicht een stof is, hoe slechter de geleidbaarheid is voor etextielen.
Er zijn nogal wat praktische problemen met de PLA. Het heeft de neiging te vervormen en te krimpen. Sommige drukknopen werkten onmiddellijk, sommige hadden een paar eerste geforceerde sluitingen nodig voordat ze voldeden, schijnbaar om de afdruk een beetje uit te rekken. Sommige leken te klein om helemaal te snappen. Het was allemaal een beetje onsamenhangend.
Ik heb ook gelezen dat de geleidbaarheid van deze materialen in de loop van de tijd kan veranderen. In dit geval zou ik zeggen dat de druk van het klikken zelf hier invloed op kan hebben. Ook het laten lopen van stroom door de snap kan de weerstand permanent verhogen. Dit zal zeker meer testen met zich meebrengen.
er is een redelijk goed overzicht van Black Magic 3D-filamenten hier
Ik wil dit snap-idee gebruiken in een handschoenontwerp. Ik wil een manier vinden om afneembare connectoren voor reksensoren te maken. Het idee zou zijn dat dit snap-bestand rechtstreeks in een 3D-geprinte sensor kan worden geïntegreerd om het op een circuit aan te sluiten.
In de review vond ik dit proces interessant en informatief. Het is niet stabiel genoeg om consistente meetbare resultaten te produceren en ik zou het graag verder onderzoeken in meer gecontroleerde experimenten.
Als je een van deze prints probeert, laat dan een reactie achter!
Aanbevolen:
Geleidende lijm en geleidende draad: maak een LED-display en een stoffen circuit dat oprolt. 7 stappen (met afbeeldingen) Antwoorden op al uw "Hoe?"
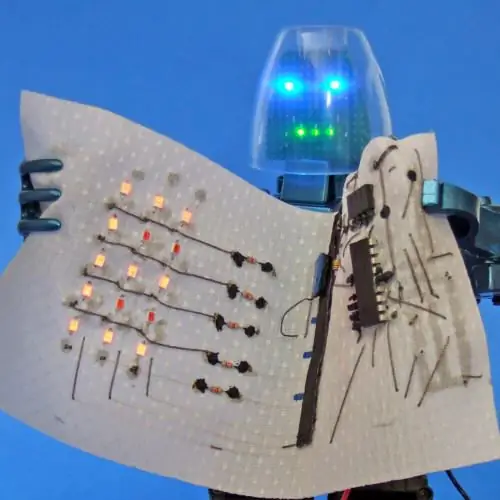
Geleidende lijm en geleidende draad: maak een LED-display en een stoffen circuit dat oprolt: maak uw eigen geleidende stoffen, draad, lijm en tape en gebruik ze om potentiometers, weerstanden, schakelaars, LED-displays en circuits te maken. en geleidende draad kunt u LED-displays en circuits maken op elke flexibele stof
Geleidende stof: maak flexibele circuits met een inkjetprinter: 4 stappen (met afbeeldingen)

Geleidende stof: maak flexibele circuits met behulp van een inkjetprinter.: Extreem flexibele en bijna transparante circuits kunnen worden gemaakt met behulp van geleidende stoffen. Hier zijn enkele van de experimenten die ik heb gedaan met geleidende stoffen. Ze kunnen worden geverfd of getekend met resist en vervolgens worden geëtst als een standaard printplaat. C
Hoe u gebruikersniveaus van NUMA toevoegt aan uw exemplaar van N met behulp van NumADD Firefox AddOn: 4 stappen
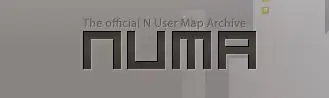
Gebruikersniveaus van NUMA toevoegen aan uw exemplaar van N NumADD Firefox-add-on gebruiken: Elke gebruiker van Metanet's N-database op gebruikersniveau NUMA weet hoe onhandig de interface is voor het kopiëren van door gebruikers gemaakte niveaus naar uw exemplaar van het spel. NumADD, elimineert de noodzaak van kopiëren en plakken en maakt het overzetten van niveaus het werk van één muisklik
Geleidende draad opwinden: 5 stappen (met afbeeldingen)
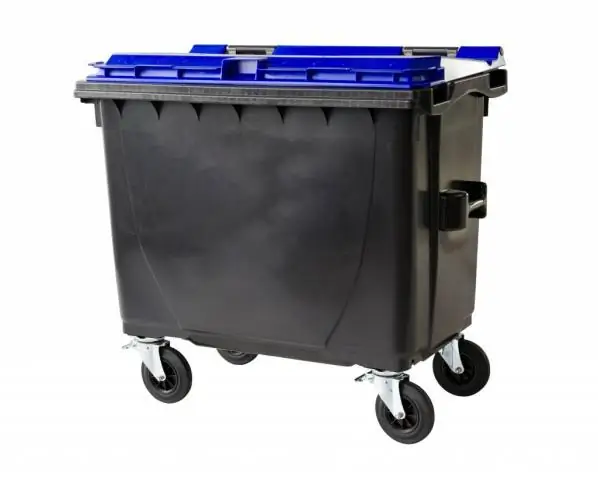
Geleidende draadopwinder: heb je wat draad maar te veel weerstand? Heb je een draad die te dun is? Een speciale mode-look nodig om uw eTextile-ontwerp te voltooien? In een snuifje om wat zachte circuits af te maken? Wind eenvoudig uw eigen geleidende draad/draad op met een beweging van uw pols
Instructies voor het voltooien van de mock-up van het ontwerp van de rupsschuif voor het heffen/verlagen van in het midden gemonteerde voetsteunen op elektrische rolstoelen - Ajarn
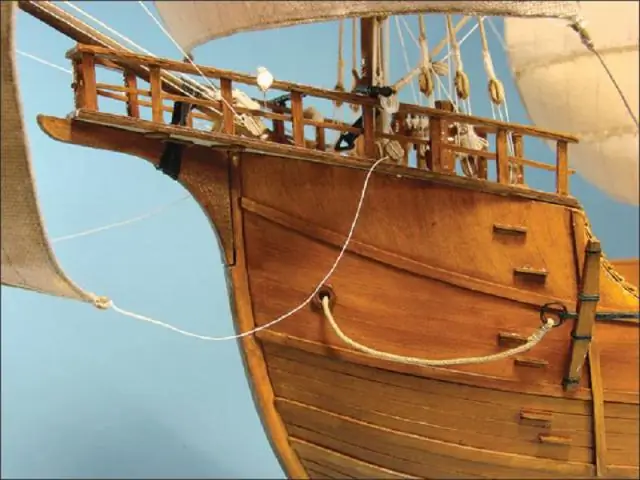
Instructies voor het voltooien van de mock-up van het ontwerp van de rupsschuif voor het omhoog/omlaag brengen van in het midden gemonteerde voetsteunen op elektrische rolstoelen: in het midden gemonteerde voetsteunen kunnen omhoog worden gebracht om onder de zitting goed te worden opgeborgen en omlaag om te worden ingezet. Een mechanisme voor onafhankelijke bediening van het opbergen en plaatsen van de voetsteun is niet inbegrepen in elektrische rolstoelen op de markt, en PWC-gebruikers hebben de behoefte geuit