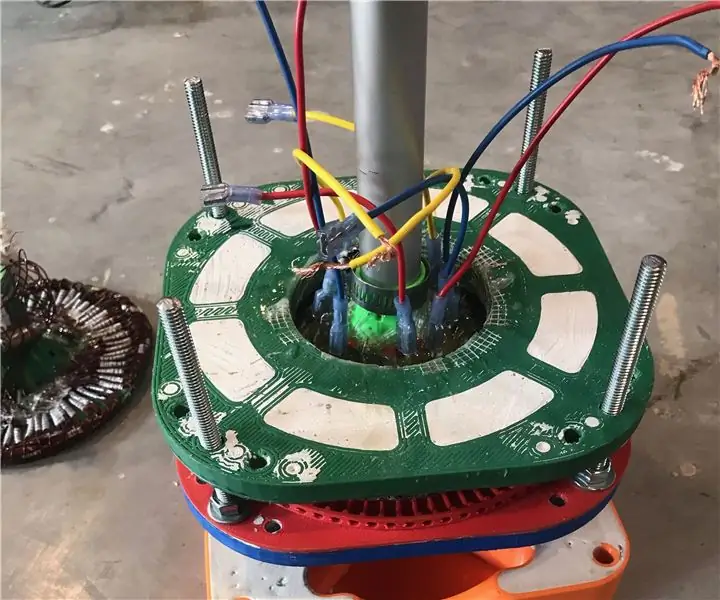
Inhoudsopgave:
2025 Auteur: John Day | [email protected]. Laatst gewijzigd: 2025-01-23 15:01
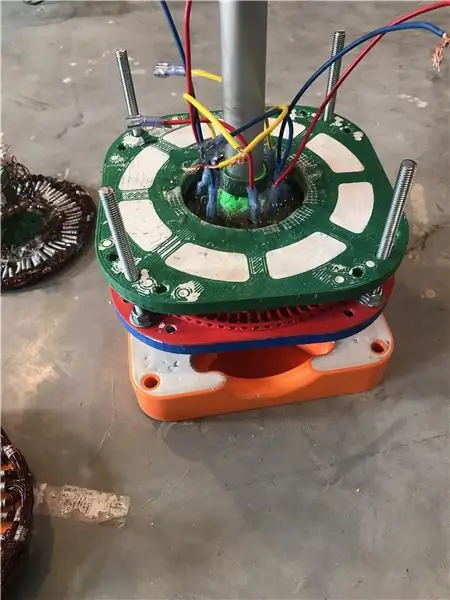
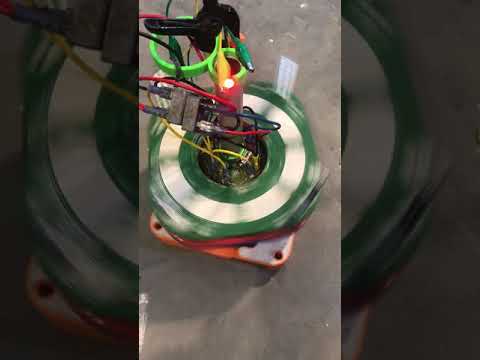
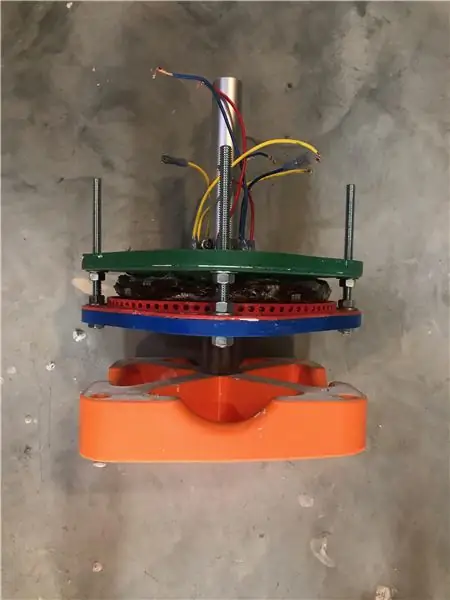
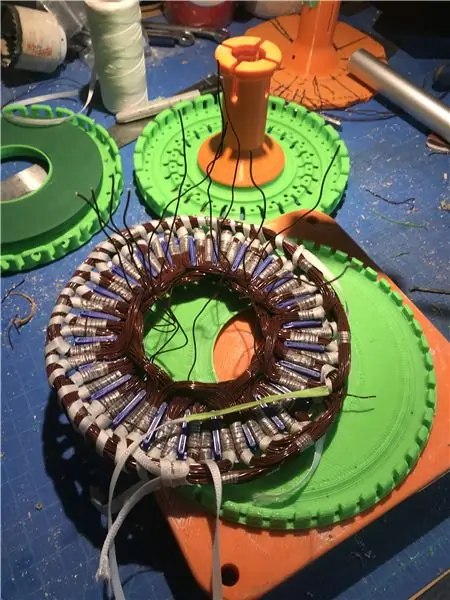
STOP!! LEES DIT EERST!!! Dit is een verslag van een project dat nog in ontwikkeling is, aarzel niet om ondersteuning te bieden.
Mijn uiteindelijke doel is dat dit type motor/dynamo een geparametriseerd open source ontwerp kan worden. Een gebruiker moet een aantal parameters kunnen invoeren, zoals koppel, snelheid, stroom, volt/rpm, gangbare magneetgroottes en misschien beschikbare ruimte, en er moet een reeks 3D-afdrukbare.stl's en.dxf-bestanden worden gegenereerd.
Wat ik heb gedaan, is een platform creëren dat een gesimuleerd ontwerp kan valideren, dat vervolgens door de gemeenschap kan worden ontwikkeld tot een meer optimaal apparaat.
Dit is gedeeltelijk een reden dat ik dit heb opgezet met een rollenbank. Een dynamometer meet het koppel en de snelheid om pk's of as Watt's te kunnen meten. In dit geval heb ik de dynamo gebouwd met een doorgaande, stationaire as, wat het opzetten van een dynamometersysteem eenvoudiger maakt, en dus kan worden geconfigureerd om te worden aangedreven als een motor door een RC ESC (hoop ik), en het gemeten koppel op de output, evenals snelheid, V en Amps, waardoor het motorrendement kan worden bepaald.
Voor mijn doeleinden kan het worden aangedreven door een motor met variabel toerental (overschot van accuboormachine, met traploze overbrenging), en gemeten askoppelinvoer, evenals V en Ampère uit, waardoor echte efficiëntie kan worden gegenereerd en de verwachte turbinebelastingen te simuleren.
In deze modus hoop ik een RC ESC te gebruiken die regeneratief kan remmen, en misschien een Arduino om de belasting te regelen die mijn VAWT draagt om MPPT (Multi Power Point Tracking) te bereiken.
MPPT wordt gebruikt in zowel zonne- als windturbinebesturing, maar voor wind is het een beetje anders. Met windenergie is een groot probleem dat als de windsnelheid 10 km/u verdubbelt tot 20 km/u, de beschikbare energie uit de wind met de kubus toeneemt, dus met 8 keer. Als 10W beschikbaar zou zijn bij 10km/u, dan is 80W beschikbaar bij 20km/u. Het is geweldig om meer energie te hebben, maar de output van de dynamo verdubbelt alleen als de snelheid verdubbelt. Dus als je de perfecte dynamo hebt voor een wind van 20 km/uur, kan zijn belasting zo sterk zijn dat hij bij 10 km/uur niet eens start.
Wat MPPT doet, is een heavy-duty solid-state schakelaar gebruiken om een dynamo zeer snel los te koppelen en vervolgens weer aan te sluiten. Hiermee kunt u aanpassen hoeveel belasting een dynamo draagt, en de Multi van de MPPT betekent dat u verschillende belastingen voor verschillende snelheden kunt instellen.
Dit is erg handig, omdat alle soorten turbines hun maximale energie verzamelen wanneer de belasting wordt afgestemd op de beschikbare energie of windsnelheid.
DUS
Dit is geen recept, hoewel ik denk dat het kan worden gekopieerd van wat ik heb gepost, en ik zou graag meer informatie verstrekken, maar ik stel voor dat de beste optie zou zijn om me verbeteringen voor te stellen, voordat de Circuits and Sensors-wedstrijd eindigt, zodat ik deze instructable kan overwegen, beantwoorden en misschien kan verbeteren.
Ik zal doorgaan met het bijwerken, herzien en toevoegen van informatie, dus als het nu interessant is, wil je misschien nog een keer inchecken, maar ik hoop nogal wat gedaan te hebben voordat de Sensors-wedstrijd op 29/19 juli afloopt.
Ik ben ook niet bepaald een sociaal beest, maar ik hou wel van een schouderklopje af en toe, en dat is een van de redenen waarom ik hier ben:-) Vertel me of je het leuk vindt om mijn werk te zien, en wil zien meer alstublieft:-)
Dit project kwam tot stand omdat ik een regelbare belasting wilde voor het testen van mijn turbineontwerpen, en ik wilde dat het gemakkelijk reproduceerbaar was, zodat anderen het ook konden gebruiken. Hiertoe beperkte ik mezelf tot het ontwerpen van iets dat kon worden gebouwd met alleen een FDM-printer, zonder dat andere werktuigmachines nodig waren. Er lijken niet veel commerciële producten te zijn die voldoen aan de behoefte aan een dynamo met een hoog koppel, een lage snelheid en een niet-cogging, hoewel er een paar uit China zijn. Over het algemeen is er niet veel vraag omdat tandwielsystemen zo goedkoop zijn en elektriciteit zo goedkoop.
Wat ik wilde was iets dat ongeveer 12V produceerde bij 40-120 tpm en ongeveer 600-750W bij 120-200 tpm. Ik wilde ook dat het compatibel zou zijn met goedkope 3-fase PMA-controllers uit de RC-wereld (ESC's Electronic Speed Controllers). Een laatste vereiste was dat het een uitloper moest zijn (behuizing of schaal met magneten roteert, terwijl as met stator stilstaat), met een as die helemaal door de behuizing gaat, en een stator die op de as klemt.
Dit instructable is een werk in uitvoering, en ik plaats het zodat mensen een beeld van het proces kunnen krijgen, niet zozeer omdat ik denk dat ze het moeten kopiëren. Een belangrijk ding dat ik zou veranderen, is dat de draadsteunplaat die ik heb gebouwd lang niet sterk genoeg is om de magneetvelden rond de ring goed te kanaliseren, dus een groot deel van de magnetische flux die in die magneten wordt betaald, wordt aan de achterkant verspild. Als ik het ontwerp opnieuw doe, wat ik binnenkort zal doen, zou ik het waarschijnlijk de magnetische achterplaten doen als cnc-gesneden stalen platen. Staal zou redelijk goedkoop zijn, veel sterker en zou het grootste deel van deze constructie vereenvoudigen. Het was interessant om de FDM/draad/gipscomposieten te maken zoals ik hier heb geïllustreerd, en met met ijzer beladen PLA zouden de dingen ook anders zijn geweest. Ik besloot echter dat ik iets wilde dat echt lang mee zou gaan, dus stalen platen.
Ik heb goede vorderingen gemaakt met deze versie, die ik zal gebruiken voor het testen van deze VAWT. Ik ben er nog niet helemaal in termen van laagspanningsprestaties. Ik denk dat mijn Wattage / Koppel in de juiste marge zit, ik zal updaten naarmate de dingen vorderen, maar op dit moment heeft wat ik heb een goede kans om de beheersbare belasting te zijn die ik nodig heb. Wanneer het kortgesloten is, lijkt het behoorlijk wat koppelweerstand te kunnen bieden, meer dan genoeg om de turbine te testen. Ik moet alleen een gecontroleerde verzetsbank opzetten, en ik heb een vriend die me daarbij helpt.
Een ding dat ik kort zal bespreken, is dat ik, zoals veel mensen nu, een paar jaar een 3D-printer (FDM-gebruikende PLA) heb gehad, waar ik 20-30 kg van heb genoten. Ik vind het echter vaak frustrerend omdat onderdelen van elke grootte/sterkte ofwel duur zijn en erg traag om te printen, ofwel goedkoop, snel en zwak zijn.
Ik weet hoeveel duizenden van deze 3D-printers er zijn, vaak niets doen omdat het te lang duurt of te veel kost om bruikbare onderdelen te maken. Ik heb een interessante oplossing bedacht voor sterkere, snellere onderdelen van dezelfde printer en PLA.
Ik noem het een "gegoten structuur", waarbij het geprinte object (bestaande uit 1 of meer geprinte delen, en soms lagers en assen), gemaakt is met holtes die ontworpen zijn om gevuld te worden met een uithardende vloeibare vulstof. Natuurlijk zijn enkele van de voor de hand liggende keuzes voor een gegoten vulling zoiets als epoxy geladen met korte streng gehakte glasvezel, die zou kunnen worden gebruikt voor zeer sterke en lichtgewicht assemblages. Ik probeer ook wat goedkopere, meer milieuvriendelijke ideeën uit. De andere kant van deze "gegoten structuur" assemblage, is dat de holte of leegte die u gaat vullen, elementen met een kleine diameter en hoge treksterkte kan hebben, voorgespannen op de gedrukte "mal/plug", wat de resulterende structuur maakt een composiet in materialen en in structuur, deels Stressed Skin (de PLA-mantel), maar met een kern met hoge druksterkte die ook elementen met hoge treksterkte bevat. Ik zal een tweede instructable maken met dit, dus zal er hier over praten, alleen om te bespreken hoe het betrekking heeft op deze build.
Stap 1: Materialenlijst en proces
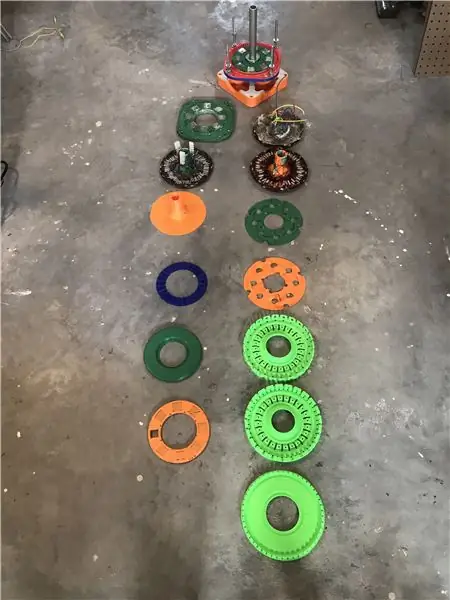
De PMA bestaat uit 3 assemblages, waarbij elke assemblage een verscheidenheid aan onderdelen en materialen bevat of gebruikt.
Van boven (lagerzijde) naar beneden (statorzijde), 1. Lagerdrager en bovenste lagerarray
2. Stator
3. Lagere magneetarray
1. De lagerdrager en bovenste magneetarray
Hiervoor heb ik de hierboven genoemde 3D-geprinte onderdelen gebruikt
- 150mm8pole bovenste mag en lagersteun CV5.stl,
- binnenste plaat aan de lagerzijde:
- buitenste plaat aan de lagerzijde:
- 1 "ID zelfinstellende lager (zoals gebruikt in standaard kussenblokken + internetlink toevoegen),
- 25' van 24g gegalvaniseerd staaldraad
- 15' van 10g gegalvaniseerd staaldraad
- 2 rollen grove staalwol
Optioneel kan de zware staaldraad en staalwol worden vervangen door stalen steunplaten, laser-/waterstraalsnijden, of een 3D-geprinte magnetische steunplaat is mogelijk (maar zwaar staaldraad is nog steeds een goed idee omdat het bestand is tegen plastische vervorming over tijd). Ik heb geprobeerd een achterplaat te gieten met epoxy geladen met ijzeroxidepoeder en had enig succes. Verbetering van de fluxkoppeling tussen magneten in de array zijdelings door een effectievere steunplaat te gebruiken, zou de Volt bij lagere toerentallen moeten verhogen. Het is ook goed om in gedachten te houden dat dit het belangrijkste structurele onderdeel is en dat de achterplaat de krachten van de magneten naar de vijzelpalen overbrengt. De magnetische krachten die de platen naar elkaar toe trekken kunnen honderden lbs zijn, en de krachten nemen exponentieel toe (in blokjes, tot de derde macht) naarmate de platen dicht bij elkaar komen. Dit kan erg gevaarlijk zijn en wees voorzichtig met gereedschap en andere voorwerpen die aangetrokken kunnen worden door de gemonteerde plaat of terug!
Ik gebruikte ongeveer 300ft van 24g gecoate magneetdraad in de wikkelingen die ik later in detail zal behandelen.
Stap 2: Fabricage van de magneetplaten
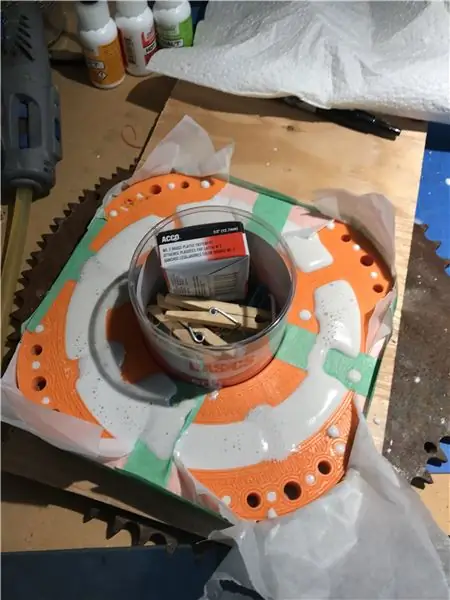
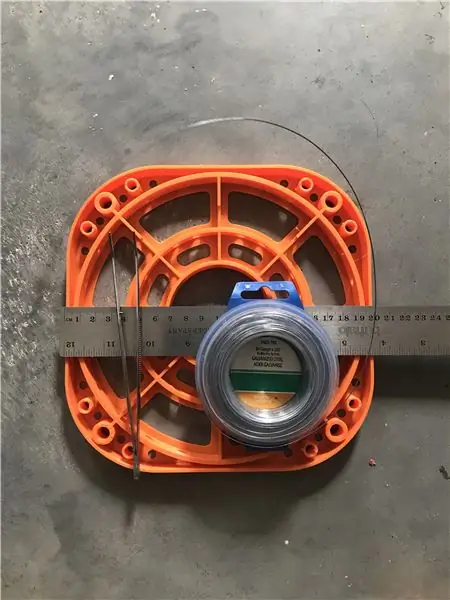
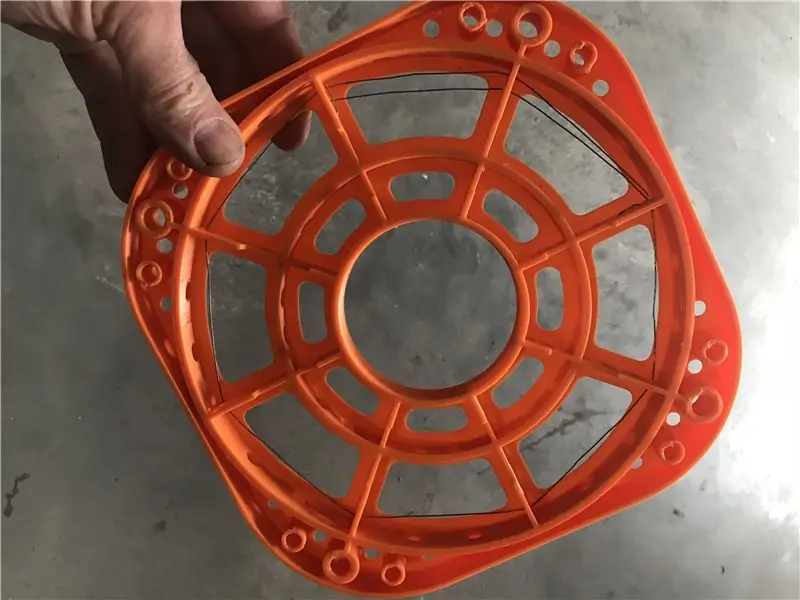
In deze axiale flux-alternator, om cogging te minimaliseren en de output te maximaliseren, gebruik ik twee magneetarrays, één aan elke kant van de statorspoelen. Dit betekent dat er geen magnetische kern nodig is om het magnetische veld door de koperen wikkelingen te trekken, zoals de meeste motor/alt-geometrieën doen. Er zijn een aantal ontwerpen voor axiale flux die gebruik maken van ferriskernen, en ik zal in de toekomst misschien wat experimenten op die manier proberen. Ik wil graag wat 3D-afdrukbaar ijzer geladen materiaal proberen.
In dit geval heb ik een 8-polige magneetarray gekozen in een cirkel van ongeveer 150 mm, met behulp van zeldzame-aardmagneten van 1 "x1" x 0,25 ". Deze maat was om ervoor te zorgen dat alle onderdelen op een printbed van 210 mm x 210 mm zouden passen. Over het algemeen heb ik deze dynamo eerst op maat gemaakt door te begrijpen dat hoe groter de diameter, hoe beter in termen van volt per tpm, dus maakte ik hem zo groot als comfortabel in mijn printbed zou passen. Ter info, er is meer dan één reden waarom groter beter is: meer ruimte voor magneten, hoe verder de magneten van het midden zijn, hoe sneller ze reizen, en er is ook meer ruimte voor koper! Al deze dingen kunnen snel oplopen! Maar een conclusie die ik ben gekomen is dat in dit maatbereik een conventionele flux-systeem is misschien een betere huisbouw. Kleine rotoren hebben niet veel ruimte, en dingen kunnen behoorlijk krap worden, vooral als je een doorgaande as doet zoals ik in dit ontwerp heb gedaan. Ook als je magneet (radiale lengte) klein is in verhouding tot je rotordiameter, zoals in deze, (ongeveer 6 "diameter tot 1" magneet), dan is de windi ng wordt een beetje vreemd met de binnenste eindwikkeling die slechts ongeveer de helft van de lengte van de buitenste is.
Terug naar de instructie! De manier waarop ik de magneetplaten van deze dynamo heb gemonteerd, is door eerst de magneetplaat (groen) op de rode flens/achterplaat te lijmen. Vervolgens plaatste ik de magneetplaat op een paar dunne lagen multiplex (ongeveer.75 dik) en plaatste beide op een zware stalen plaat, zodat de magneten het geheel op zijn plaats konden klemmen. Daarna wond ik staaldraad op de achterkant van de magneetplaten. Dit ging niet helemaal zoals ik had gehoopt. Het sterke magnetische veld trok de draad naar het midden van de magneten en het lukte me niet om elke rij draad perfect te buigen op de volgende plek, zonder de eerste wikkel te verdringen. Ik had gehoopt dat ik de draad er gewoon in kon opspoelen, en de magnetische flux zou hem vastzetten. Vervolgens probeerde ik draadringen door te knippen, en dit was beter, maar nog steeds verre van wat ik had gedaan. hoopte in termen van het verkrijgen van een mooie consistente steunplaat van draad. Complexere manieren om dit voor elkaar te krijgen zijn mogelijk, en misschien de moeite waard om in de toekomst te experimenteren. Ik heb ook geprobeerd staalwol te gebruiken, verdicht in het magnetische veld, als een steunplaat of flux Dit leek te werken, maar de werkelijke ijzerdichtheid leek niet erg hoog te zijn, dus ik heb test de effectiviteit niet, deels omdat ik geloofde dat de draadstructuur belangrijk was voor de mechanische belastingen op de magneetplaten. De staalwol kan ook toekomstig onderzoek waard zijn, maar waterstraalgesneden stalen platen zijn waarschijnlijk de volgende optie die ik zal proberen.
Vervolgens nam ik het oranje 3D-geprinte onderdeel en weefde er draad doorheen en eromheen, langs wat mij de richtingen van de hoogste belasting leek te zijn, bout tegen bout en bout om een paar keer op elke hoek te centreren. Ik heb het ook rond de boutgaten gewikkeld waar de draadstang passeert als vijzelpalen om de afstand tussen de platen te behouden en instelbaar te maken.
Nadat ik er zeker van was dat de magneetplaat en flens goed genoeg waren, en de oranje steunplaat naar tevredenheid was voorzien van versterkingsdraad, heb ik de twee met lijm verbonden. Voorzichtigheid is geboden, aangezien deze lijmverbinding waterdicht of dicht moet zijn. Ik had de eerste twee keer lekkage, en het is een puinhoop, verspilt veel gips en is meer stress dan je nodig hebt. Ik raad aan om wat blauwe tack of andere kauwgom zoals niet-permanente lijm in de buurt te houden om lekken snel op te lossen. Nadat de onderdelen zijn samengevoegd, vult u het met het versterkende materiaal van uw keuze. Ik gebruikte een harde pleister, bewerkt met PVA-lijm. Het gips wordt verondersteld een druk van 10.000 psi te bereiken, maar niet veel onder spanning (dus de draad). Ik zou graag epoxy proberen met gehakt glas, en cabosil, of beton en hulpstoffen.
Een handig ding van de pleister is dat als het eenmaal schopt, je nogal wat tijd hebt waar het hard, maar kwetsbaar is en lekken of klodders gemakkelijk kunnen worden geschraapt of eraf geslagen.
In dit ontwerp zijn er twee magneetplaten. De ene heeft een lager, een standaard 1 kussenblok zelfuitlijnende eenheid. Ik heb de mijne al vroeg in de magneetarray gedrukt. Voor de toepassing waarvoor ik hem heb ontworpen, bevindt een tweede lager zich in de turbine boven de dynamo, dus ik alleen die ene zelfinstellende lager gebruikt. Dit was uiteindelijk een beetje lastig. Deze onderdelen zouden ook kunnen worden geassembleerd met elke magneetplaat met een lager, als de uitgangsdraden van de stator intern door de gemonteerde as zouden worden geleid. Dit zou zorgen ervoor dat contra-roterende propellers kunnen worden gemonteerd op een gemeenschappelijke, niet-roterende as/buis.
Stap 3: De stator maken

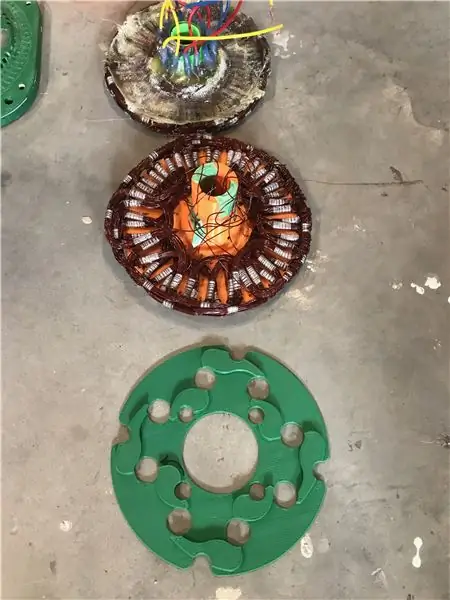
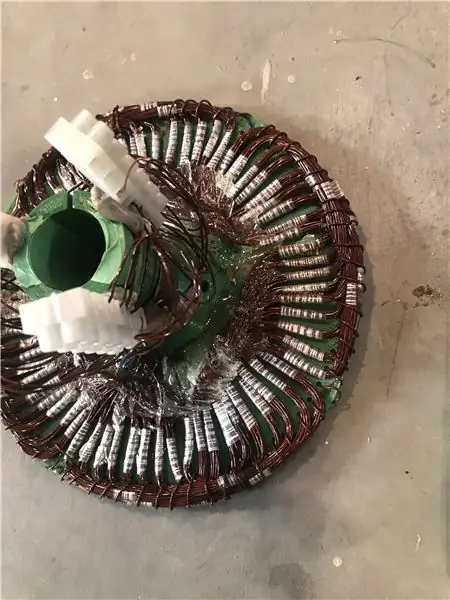
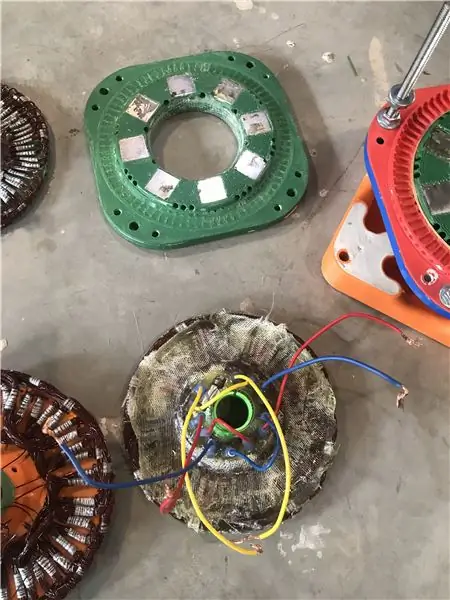
In overeenstemming met mijn thema om uit te leggen wat ik heb gedaan en waarom het toen een goed idee leek, zal de stator wat meer ruimte nodig hebben.
In een PMA zijn de wikkelingen over het algemeen stationair, terwijl de magnetische assemblages roteren. Dit is niet altijd het geval, maar bijna altijd. In een axiale fluxassemblage, met begrip van de fundamentele "rechterhandregel", is het duidelijk dat elke geleider die een roterend magnetisch veld tegenkomt, stroom en spanning zal hebben tussen de uiteinden van de draad, waarbij de hoeveelheid bruikbare stroom evenredig is naar de richting van het veld. Als het veld evenwijdig aan de draad beweegt (bijvoorbeeld in een cirkel rond de rotatie-as), wordt er geen bruikbare stroom gegenereerd, maar wel significante wervelstromen die de beweging van de magneten weerstaan. Als de draad loodrecht loopt, wordt de hoogste spanning en stroomuitgang bereikt.
Een andere veralgemening is dat de ruimte in de stator, waar de magnetische flux doorheen gaat tijdens het draaien, voor een maximaal wattage-output, moet worden gevuld met zoveel mogelijk koper, allemaal radiaal gelegd, als mogelijk. Dit is een probleem voor axiale fluxsystemen met een kleine diameter, aangezien in dit geval het gebied dat beschikbaar is voor koper nabij de schacht een fractie is van het gebied aan de buitenrand. Het is mogelijk om 100% koper te krijgen in het binnenste gebied dat het magnetische veld tegenkomt, maar binnen deze geometrie krijg je misschien maar 50% aan de buitenrand. Dit is een van de sterkste redenen om weg te blijven van te kleine axiale fluxontwerpen.
Zoals ik eerder heb gezegd, gaat dit instructable niet over hoe ik het opnieuw zou doen, het is meer om in een aantal richtingen te wijzen die veelbelovend lijken, en te pronken met enkele van de kuilen die op dit pad kunnen worden bereikt.
Bij het ontwerpen van de stator wilde ik hem zo flexibel mogelijk maken in termen van uitgangsspanning per tpm, en ik wilde dat deze driefasig was. Voor maximale efficiëntie, door het minimaliseren van gegenereerde wervelstromen, mag elk "been" (elke zijde van een spoel moet worden gezien als een "been") slechts één magneet tegelijk tegenkomen. Als magneten dicht bij elkaar zijn, of elkaar raken, zoals het geval is bij veel hoogvermogen rc-motoren, zullen gedurende de tijd dat het "been" door de magnetische fluxomkering gaat, aanzienlijke wervelstromen worden ontwikkeld. In motortoepassingen maakt dit niet zoveel uit, omdat de spoel wordt bekrachtigd door de controller wanneer deze zich op de juiste locatie bevindt.
Ik heb de magneetarray op maat gemaakt met deze concepten in gedachten. De acht magneten in de array zijn elk 1 "breed en de ruimte ertussen is 1/2". Dit betekent dat een magnetisch segment 1,5" lang is en ruimte heeft voor 3 x 1/2" "poten". Elk "been" is een fase, dus op elk punt ziet één been een neutrale flux, terwijl de andere twee stijgende flux en afnemende flux zien. Perfecte 3-fase output, maar door het neutrale punt zoveel ruimte te geven (om wervelstromen te minimaliseren), en door vierkante (of taartvormige) magneten te gebruiken, piekt de flux bijna vroeg, blijft hoog en daalt dan snel naar nul. Dit type uitvoer wordt volgens mij trapeziumvormig genoemd en kan voor sommige controllers, die ik begrijp, moeilijk zijn. Ronde magneten van 1" in hetzelfde apparaat zouden meer een echte sinusgolf geven.
Over het algemeen zijn deze zelfgebouwde dynamo's gebouwd met behulp van "spoelen", donutvormige draadbundels, waarbij elke zijde van de donut een "poot" is en een aantal spoelen aan elkaar kunnen worden bevestigd, in serie of parallel. De donuts zijn gerangschikt in een cirkel, met hun middelpunten uitgelijnd met het midden van het magneetpad. Dit werkt, maar er zijn enkele problemen. Een probleem is dat, aangezien de geleiders niet radiaal zijn, een groot deel van de geleider niet onder een hoek van 90 graden naar het magnetische veld gaat, zodat er wervelstromen worden gegenereerd, die verschijnen als warmte in de spoel, en weerstand tegen rotatie in de magnetische array's. Een ander probleem is dat omdat de geleiders niet radiaal zijn, ze niet zo mooi in elkaar passen. De output is recht evenredig met de hoeveelheid draad die in deze ruimte past, dus de output wordt verminderd door niet-radiale "benen". Hoewel het mogelijk zou zijn en soms wordt gedaan in commerciële ontwerpen, vereist het opwinden van een spoel met radiale "benen, verbonden boven en onder, 2x zoveel eindwikkeling als een serpentinewikkeling waarbij de bovenkant van een been is verbonden met de bovenkant van de volgende geschikte been, en dan wordt de onderkant van dat been verbonden met het volgende geschikte been, en zo verder.
De andere grote factor in axiale flux-alternators van dit type (roterende magneten boven en onder de stator), is de opening tussen de platen. Dit is een relatie met een kubuswet, aangezien u de afstand tussen platen met 1/2 verkleint, neemt de magnetische fluxdichtheid toe met 8x. Hoe dunner u uw stator kunt maken, hoe beter!
Met dit in gedachten heb ik een 4-lobbige opwindmal gemaakt, een systeem opgezet voor het afmeten van ongeveer 50ft draadstrengen en de mal 6 keer gewikkeld, waardoor draadbundels met een diameter van ongeveer 6 mm ontstaan. Deze pas ik op de blauwe afstandsring en knoopte ze vast door de gaten zodat de draadeinden aan de achterkant naar buiten kwamen. Dit was niet gemakkelijk. Het werd een beetje geholpen door de bundels zorgvuldig af te plakken zodat ze niet los zaten, en door mijn tijd te nemen en een glad houten vormgereedschap te gebruiken om de draden op hun plaats te duwen. Toen ze allemaal op hun plaats waren vastgebonden, werd de blauwe afstandsring in de grootste van de lichtgroene vormkuipen geplaatst en met behulp van het donkergroene donutvormgereedschap, aan de andere kant van de lichtgroene kuip, voorzichtig platgedrukt met een bankschroef. Deze vormkuip heeft een groef waar de kronkels van de binddraad in kunnen zitten. Dit kost tijd en geduld als je voorzichtig ongeveer 1/5 slag draait, drukt, draait en doorgaat. Hierdoor wordt de schijf plat en dun, terwijl de eindwikkelingen zich kunnen opstapelen. Het zal je misschien opvallen dat mijn 4-lobbige wikkeling rechte "benen" heeft, maar de binnen- en buitenverbindingen zijn niet rond. Dit was bedoeld om het voor hen gemakkelijker te maken om te stapelen. Het lukte niet zo goed. Als ik het opnieuw zou doen, zou ik ervoor zorgen dat de binnen- en buitenwindingen cirkelvormige paden volgen.
Nadat ik het plat en dun had gemaakt en de randen naar beneden waren gepakt, heb ik een plat lint rond de rand gewikkeld om het te verdichten, en nog een op, neer en rond elke poot en dan ook naar die ernaast. Nadat dit is gebeurd, kunt u de binddraden verwijderen en overschakelen naar de kleinere perskuip, en teruggaan naar de bankschroef en deze zo dun en plat mogelijk drukken. Als het plat is, verwijder het dan uit de perskuip. In plaats van het complexe proces van het zorgvuldig waxen en coaten van mallen zoals deze met lossingsmiddelen, gebruik ik over het algemeen gewoon een paar lagen stretchfolie (uit de keuken). Leg een paar lagen op de bodem van de mal en leg de glasvezel op de stretchfolie. Voeg vervolgens de statormontagebuis toe, die op de bovenkant van de lichtgroene vormkuip past, maar de laag rekfolie en glasvezel ertussen heeft. Voeg vervolgens de statorwikkeling weer op zijn plaats toe om zowel de rekfolie als de glasvezel naar beneden te duwen en de statormontagebuis op zijn plaats te vergrendelen. Keer dan terug naar de bankschroef en druk opnieuw plat. Zodra het goed in de kuip past, met de rekfolie en glasvezel ingeklemd, wordt glasvezeldoek toegevoegd (met een gat in het midden voor de statormontagebuis).
Nu is het klaar om het hechtmateriaal te gieten, epoxy of polyesterhars wordt vaak gebruikt. Voordat dit is gedaan, is een zorgvuldige voorbereiding belangrijk, want als je eenmaal aan dit proces bent begonnen, kun je niet echt stoppen. Ik gebruikte een 3D-geprinte basisplaat die ik eerder had gemaakt, met een gat van 1 "in het midden en een vlakke plaat eromheen. Ik gebruikte een 16" stuk van 1" aluminium buis, waar de statormontagebuis overheen zou passen en loodrecht op de vlakke plaat gehouden. De groene vormkuip, statorwikkeling en statormontagebuis werden naar beneden geschoven om op de vlakke plaat te zitten. Voordat ik epoxy mengde, maakte ik eerst 4 stukken krimpfolie klaar en plaatste voorzichtig een 5e stuk op de donkergroen vormende donut, zodat het de minimale rimpels op het gezicht tegen de statorwikkeling zou hebben. Nadat ik de epoxy had gemengd en op de glasvezeldoek had gegoten, legde ik voorzichtig de rekfolie rond de 1 "buis en plaatste de groene er bovenop een ring vormen. Ik had ook een paar oude remschijven voorbereid, die wat gewicht gaven, en mooi op de groenvormende donut zaten. Hierna plaatste ik een omgekeerde pot bovenop de remschijven en bovenop de pot stapelde ik ongeveer 100 pond aan spullen. Ik liet dit 12 uur staan en het kwam ongeveer 4-6 mm dik uit.
Stap 4: Testen en sensoren
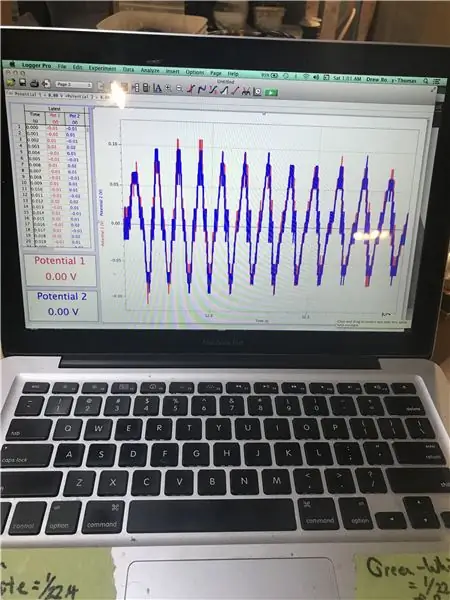
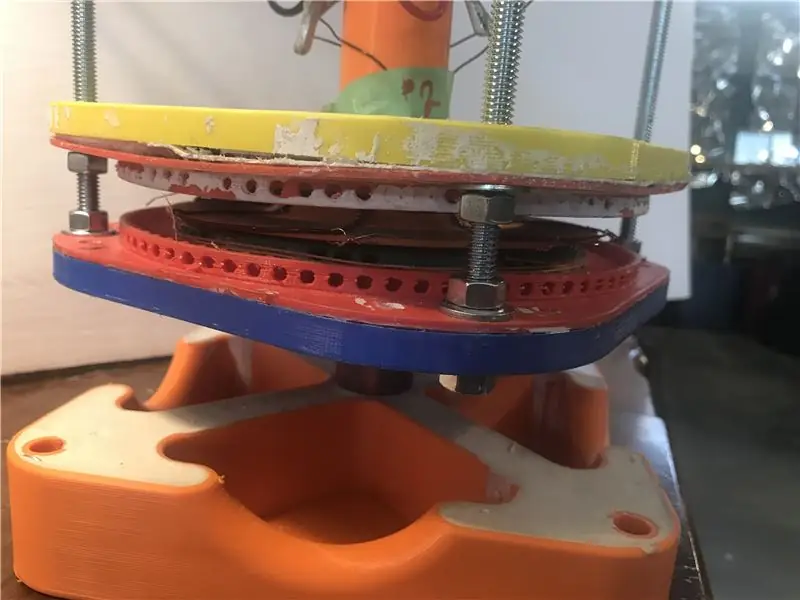
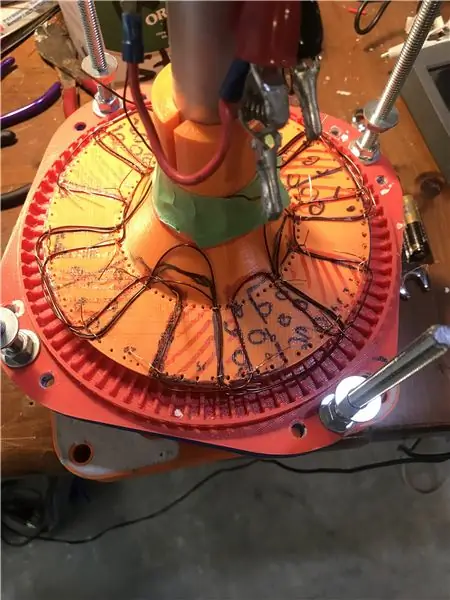
Er zijn een aantal meetbare in- en uitgangen van de dynamo, en het is niet eenvoudig om ze allemaal tegelijkertijd te meten. Ik heb het geluk dat ik een aantal tools van Vernier heb die dit veel gemakkelijker maken. Vernier maakt producten op educatief niveau, niet gecertificeerd voor industrieel gebruik, maar zeer nuttig voor onderzoekers zoals ikzelf. Ik gebruik een Vernier datalogger, met een verscheidenheid aan plug-and-play sensoren. Voor dit project gebruik ik hall-gebaseerde stroom- en spanningssondes om de output van de dynamo te meten, een optische sensor om de snelheid van de dynamo te geven en een loadcel om de koppelinvoer te meten. Al deze instrumenten worden ongeveer 1000 keer per seconde gesampled en opgenomen op mijn laptop, met behulp van de Vernier-logger als AD-doorvoerapparaat. Op mijn laptop kan de bijbehorende software realtime berekeningen uitvoeren op basis van de invoer, waarbij koppel- en snelheidsgegevens worden gecombineerd om realtime invoerasvermogen in Watt en realtime uitvoergegevens in elektrische Watts te geven. Ik ben nog niet klaar met dit testen, en input van iemand met een beter begrip zou nuttig zijn.
Een probleem dat ik heb is dat deze dynamo echt een zijproject is, en dus wil ik er niet te veel tijd aan besteden. Zoals het is, denk ik dat ik het kan gebruiken voor een regelbare belasting voor mijn VAWT-onderzoek, maar uiteindelijk zou ik graag met mensen willen werken om het te verfijnen, zodat het een efficiënte match is voor mijn turbine.
Toen ik ongeveer 15 jaar geleden met VAWT-onderzoek begon, realiseerde ik me dat het testen van VAWT's en andere prime movers complexer is dan de meeste mensen beseffen.
Een primair probleem is dat de energie die wordt weergegeven in een bewegende vloeistof, exponentieel is aan de bewegingssnelheid. Dit betekent dat als je de snelheid van een stroom verdubbelt, de energie in de stroom 8x toeneemt (het is in blokjes). Dit is een probleem, aangezien dynamo's meer lineair zijn en in het algemeen, als u het toerental van een dynamo verdubbelt, krijgt u ongeveer 2x de watt.
Deze fundamentele mismatch tussen de turbine (apparaat voor het verzamelen van energie) en de dynamo (asvermogen tot nuttig elektrisch vermogen) maakt het moeilijk om een dynamo voor een windturbine te kiezen. Als u een dynamo kiest die past bij uw windturbine die het meeste beschikbare vermogen genereert bij wind van 20 km/u, zal deze waarschijnlijk niet eens beginnen te draaien tot 20-25 km/u omdat de belasting van de turbine van de dynamo te hoog zal zijn. Met die dynamo match, als de wind eenmaal boven de 20 km is, zal de turbine niet alleen maar een fractie van de energie opnemen die beschikbaar is in de wind met hogere snelheid, de turbine kan te snel draaien en beschadigd raken omdat de belasting die door de dynamo wordt geleverd niet hoog is genoeg.
In het laatste decennium is een oplossing zuiniger geworden door de prijsdaling van besturingselektronica. In plaats van te proberen een reeks snelheden aan te passen, berekent de ontwerper de maximale snelheid waarmee het apparaat moet werken, en kiest hij een dynamo op basis van de hoeveelheid energie en de ideale snelheid voor de turbine bij die snelheid, of iets daarboven.. Deze dynamo, indien aangesloten op zijn belasting, zou normaal gesproken te veel koppel leveren bij het lage toerentalbereik, en de overbelaste turbine zal niet alle energie opnemen die hij zou kunnen hebben als hij correct zou worden geladen. Om de juiste belasting te creëren, wordt een controller toegevoegd die de dynamo tijdelijk loskoppelt van de elektrische belasting, waardoor de turbine op de juiste snelheid kan komen en de dynamo en belasting opnieuw worden aangesloten. Dit wordt MPPT (Multi Power Point Tracking) genoemd. De regelaar is zo geprogrammeerd dat als de turbinesnelheid verandert (of de spanning van de dynamo stijgt), de dynamo ongeveer duizend keer per seconde wordt aangesloten of losgekoppeld om overeen te komen met de belasting die voor die snelheid of spanning is geprogrammeerd.
Aanbevolen:
Flux - . gebruiken Basisprincipes van solderen: 5 stappen
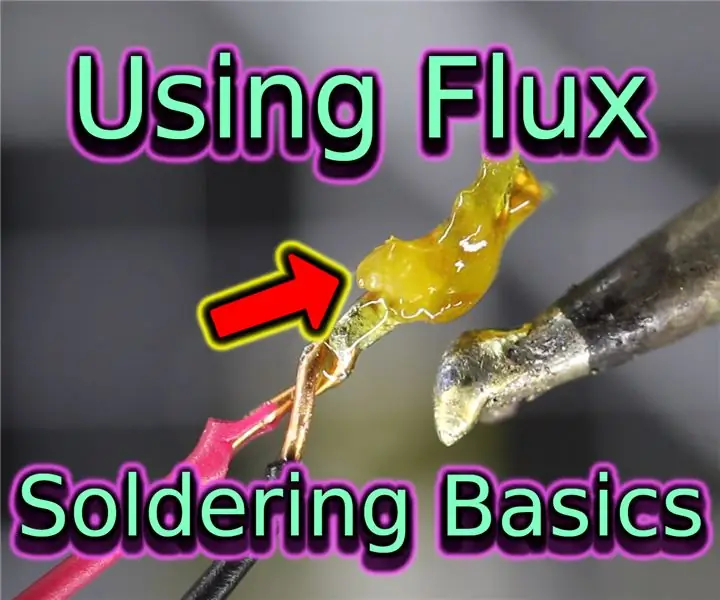
Flux | . gebruiken Basisprincipes van solderen: wanneer u soldeert, moet het soldeer goed hechten aan de onderdelen waarop u soldeert. Het metaal van de onderdelen en het metaal van het soldeer moeten direct met elkaar in contact komen om een goede hechting te creëren. Maar sinds ik