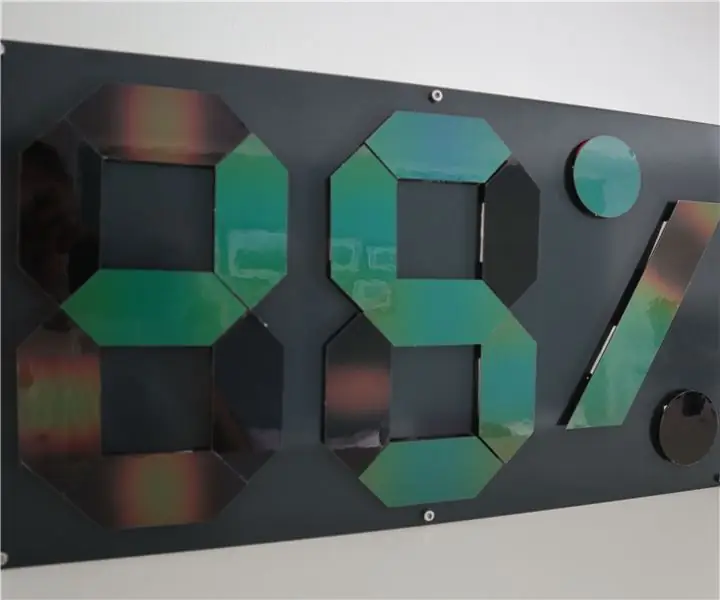
Inhoudsopgave:
- Benodigdheden
- Stap 1: Het maken van de koperen platen
- Stap 2: Vloeibaar kristalblad bevestigen
- Stap 3: TEC-element bevestigen
- Stap 4: Aluminiumplaat voorbereiden
- Stap 5: Segmenten koppelen
- Stap 6: Heatsinks en houders bevestigen
- Stap 7: Code uploaden
- Stap 8: Bedrading Waanzin
- Stap 9: Acrylplaat voorbereiden
- Stap 10: Voltooid project
2025 Auteur: John Day | [email protected]. Laatst gewijzigd: 2025-01-23 15:01
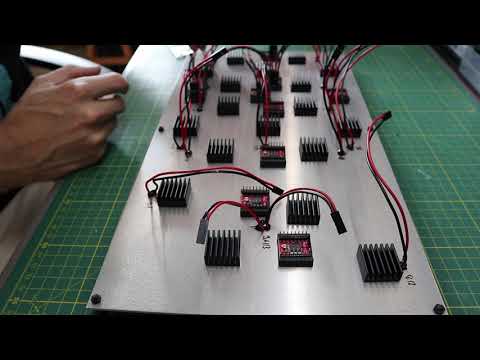
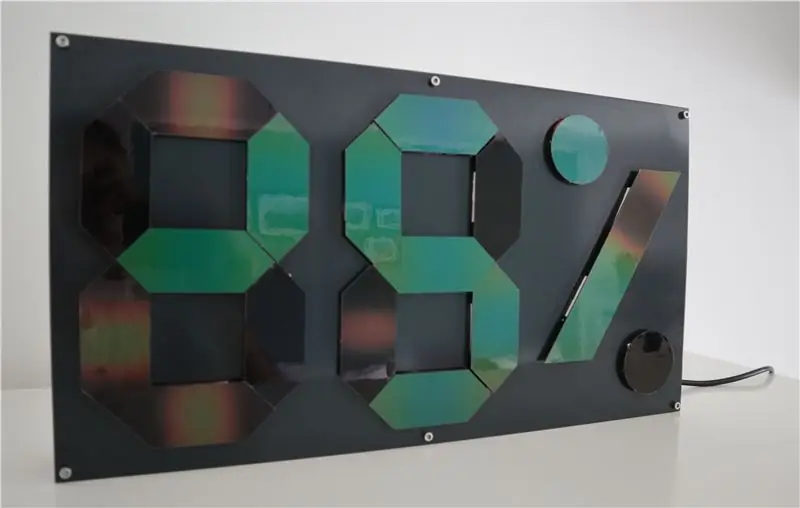

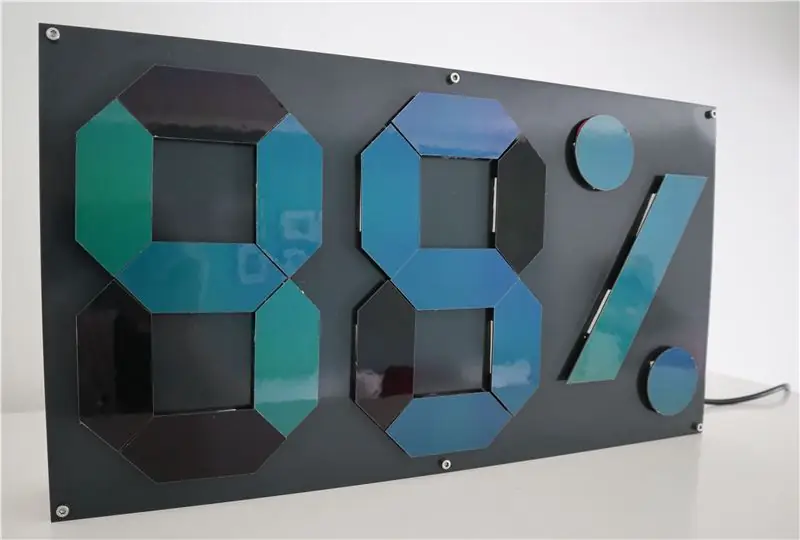
Ik ben al geruime tijd bezig met dit project. Het oorspronkelijke idee kwam bij mij op na het bouwen van een TEC-controllerdemonstrator op het werk voor een handelsbeurs. Om de verwarmings- en koelmogelijkheden van de TEC te laten zien, gebruikten we thermochrome verf die van zwart naar transparant verandert.
In dit project heb ik het idee verder ontwikkeld en een tweecijferig 7-segments display gebouwd met behulp van koperen platen die zijn bedekt met thermochrome platen op basis van vloeibare kristallen. Achter elke koperen plaat zit een TEC-element dat de temperatuur regelt en daardoor de kleur van de vloeibare kristalplaat verandert. De cijfers tonen de temperatuur en vochtigheid van een DHT22-sensor.
Misschien waardeer je de ironie van het hebben van een apparaat dat de omgevingstemperatuur weergeeft door zijn eigen temperatuur te veranderen;-)
Benodigdheden
- 3 stuks, 150x150 mm vloeibare kristallen plaat (29-33°C) (zie hier).
- 17 stuks, koperen platen, 1 mm dik (afmetingen zie hieronder)
- 401 x 220 x 2 mm aluminium plaat (grijs/zwart geanodiseerd)
- 401 x 220 x 2 mm acrylplaat (wit)
- 18 stuks, TES1-12704 peltier-element
- 9 stuks, TB6612FNG dubbele motordriver
- 6 stuks, Arduino Nano
- 2 stuks, 40x40x10 mm koelventilator
- 18 stuks, 25x25x10 mm koellichaam
- 12 V, 6 A voeding
- DHT22 (AM2302) temperatuur- en vochtigheidssensor
- 6 stuks, 40 mm lange PCB afstandhouders
Daarnaast heb ik deze warmtegeleidende epoxy gebruikt die vrij goedkoop was en een lange potlife heeft. Een boor- en dremelgereedschap werd gebruikt om de nodige gaten in de aluminium- en acrylplaten te maken. Houder voor de Arduino's en PCB's voor motorstuurprogramma's werden 3D-geprint en bevestigd met hete lijm. Ook heb ik heel veel dupont-draden gebruikt om alle verbindingen te maken. Verder kwam deze print met schroefklemmen goed van pas om de 12 V voeding te verdelen.
Let op: Blijkbaar hebben veel van de TB6612FNG-kaarten de verkeerde condensatoren geïnstalleerd. Hoewel alle verkopers het bord specificeren voor motorspanningen tot 15 V, zijn de condensatoren vaak alleen geschikt voor 10 V. Nadat ik de condensatoren op mijn eerste twee borden had opgeblazen, heb ik ze allemaal gedesoldeerd en vervangen door de juiste.
Stap 1: Het maken van de koperen platen
Voor de koperplaten heb ik gebruik gemaakt van een online lasersnijservice (zie hier) waar ik de bijgevoegde dxf-bestanden kon uploaden. Omdat de vormen echter niet erg ingewikkeld zijn, is lasersnijden geen must en zijn er waarschijnlijk goedkopere fabricagetechnieken (bijvoorbeeld ponsen, zagen). In totaal zijn 14 van de segmenten, twee cirkels en één streepje nodig voor de weergave. De dikte van de koperplaten was 1 mm, maar kan waarschijnlijk worden verminderd tot 0,7 of 0,5 mm, waardoor er minder verwarmings-/koelvermogen nodig is. Ik heb koper gebruikt omdat de warmtecapaciteit en thermische geleidbaarheid superieur is aan aluminium, maar dit laatste zou ook redelijk goed moeten werken.
Stap 2: Vloeibaar kristalblad bevestigen
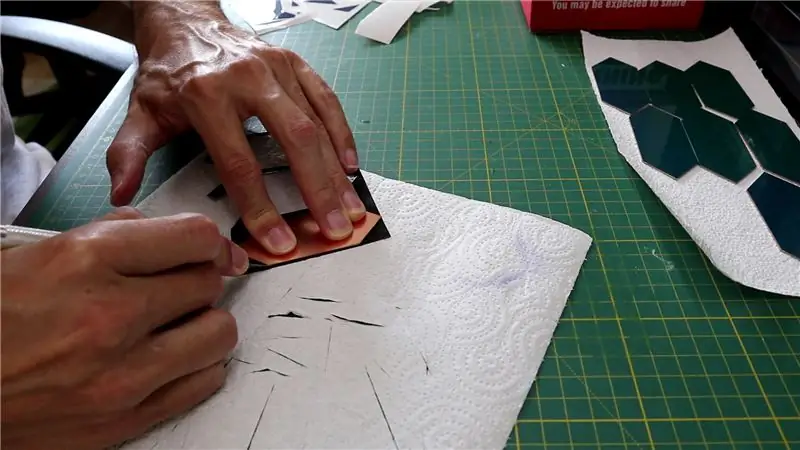
Het belangrijkste onderdeel van dit project is de thermochrome vloeibaar-kristalfolie die ik van SFXC heb verkregen. De folie is verkrijgbaar in verschillende temperatuurbereiken en verkleurt van zwart bij lage temperaturen over rood, oranje en groen naar blauw bij hoge temperaturen. Ik probeerde twee verschillende bandbreedtes 25-30°C en 29-33°C uit en koos uiteindelijk voor het laatste. Omdat verwarmen met een peltier-element gemakkelijker is dan koelen, moet het temperatuurbereik iets boven kamertemperatuur liggen.
De vloeibare kristalfolie heeft een zelfklevende achterkant die zeer goed hecht aan de koperplaten. De overtollige folie werd met een exact mes om de plaat gesneden.
Stap 3: TEC-element bevestigen
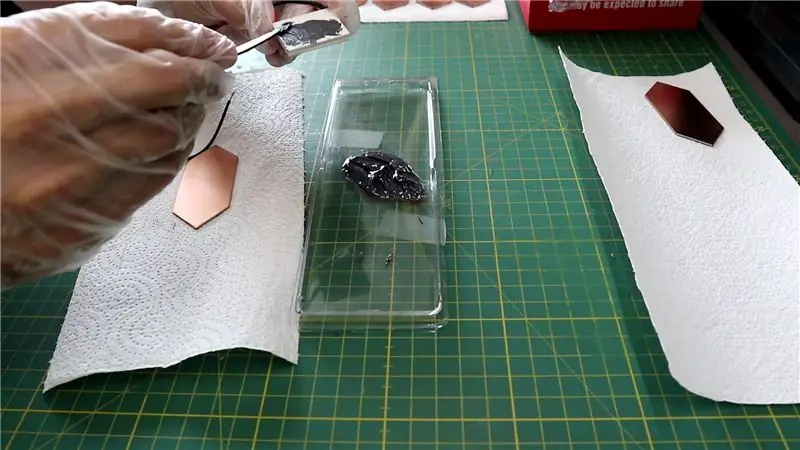
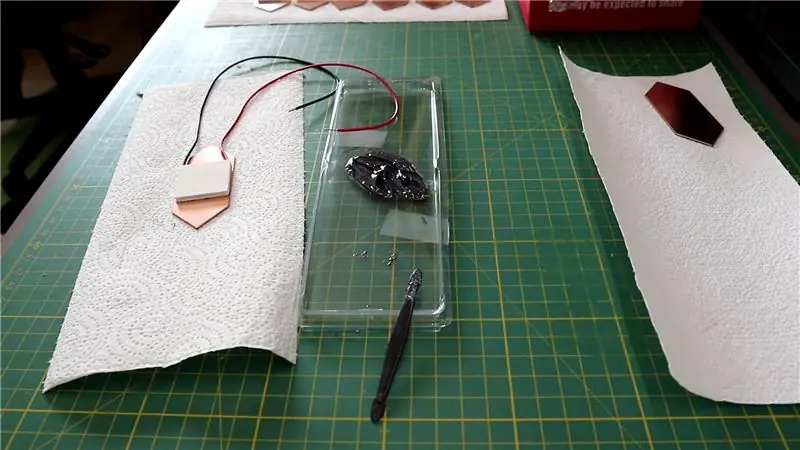
De peltiers werden bevestigd aan het midden van elke koperen plaat met behulp van thermisch geleidende epoxy. De platen zijn iets groter dan de peltiers zodat ze er helemaal achter blijven. Voor de langere plaat die het streepje van het procentteken vormt, heb ik twee peltiers gebruikt.
Stap 4: Aluminiumplaat voorbereiden
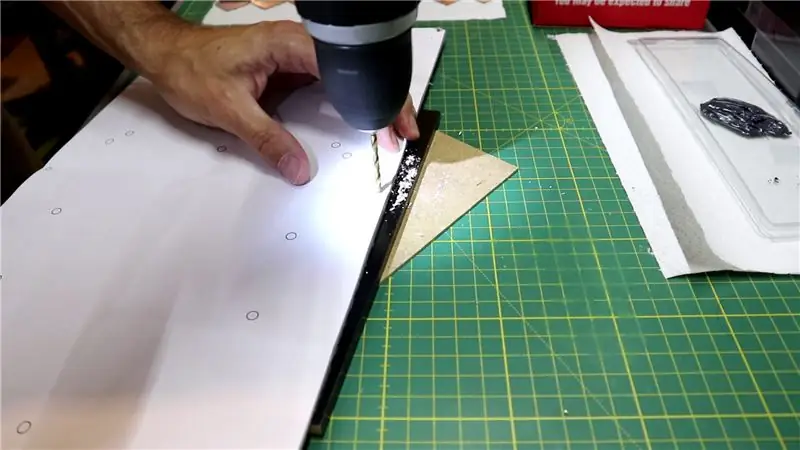
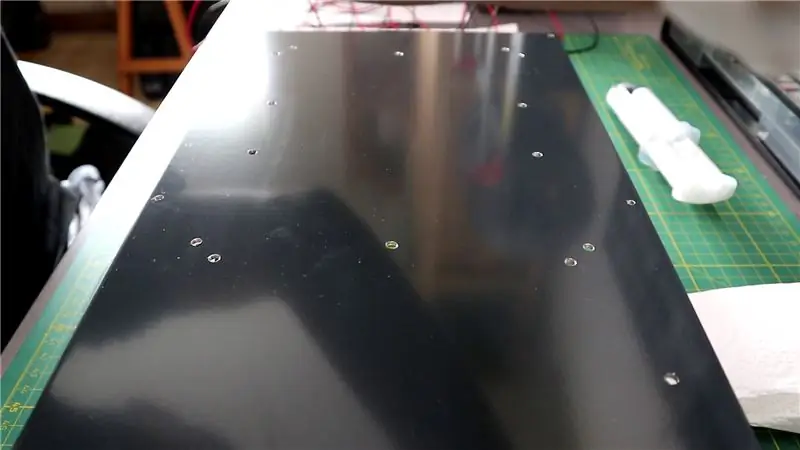
Om wat geld te besparen heb ik zelf alle gaten in aluminium plaat geboord. Ik heb zojuist de bijgevoegde pdf op A3-papier uitgeprint en als boorsjabloon gebruikt. Er is een gat voor elk segment waar de TEC-kabels doorheen lopen en 6 gaten aan de randen om later de acrylplaat te bevestigen.
Stap 5: Segmenten koppelen
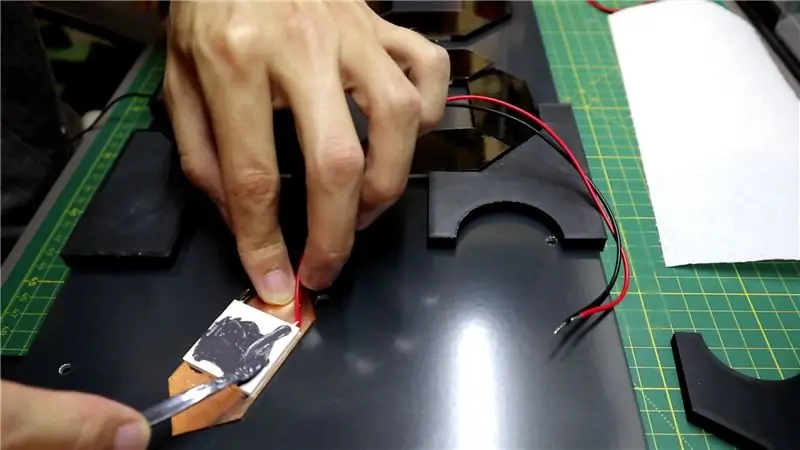
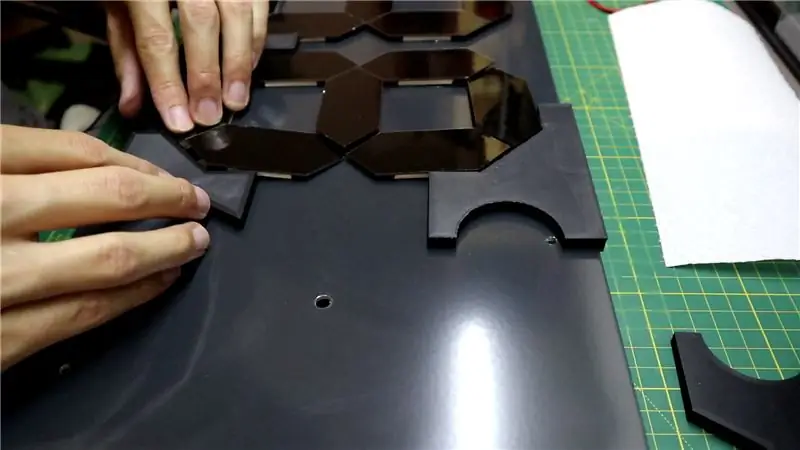
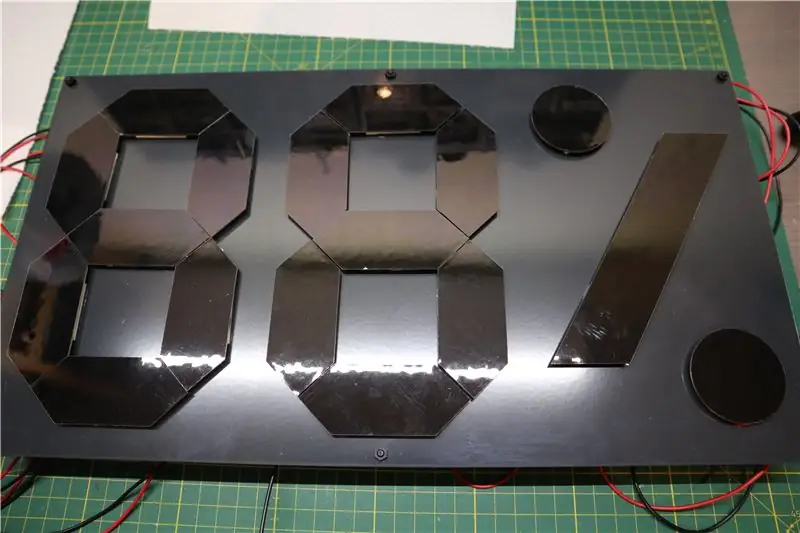
Een van de moeilijkste onderdelen van dit project was om de segmenten correct op de achterplaat te bevestigen. Ik heb verschillende mallen in 3D geprint die me zouden helpen bij het uitlijnen van de segmenten, maar dit werkte slechts gedeeltelijk omdat de segmenten constant weggleden. Daarnaast drukken de kabels op de peltier zodat deze loskomt van de plaat. Het is me op de een of andere manier gelukt om alle segmenten op de juiste plaats te lijmen, maar een van de peltiers in het dashboardsegment heeft een zeer slechte thermische koppeling. Het is misschien beter om zelfklevende thermische pads te gebruiken in plaats van epoxy, hoewel ik vermoed dat dit na verloop van tijd kan losraken.
Stap 6: Heatsinks en houders bevestigen
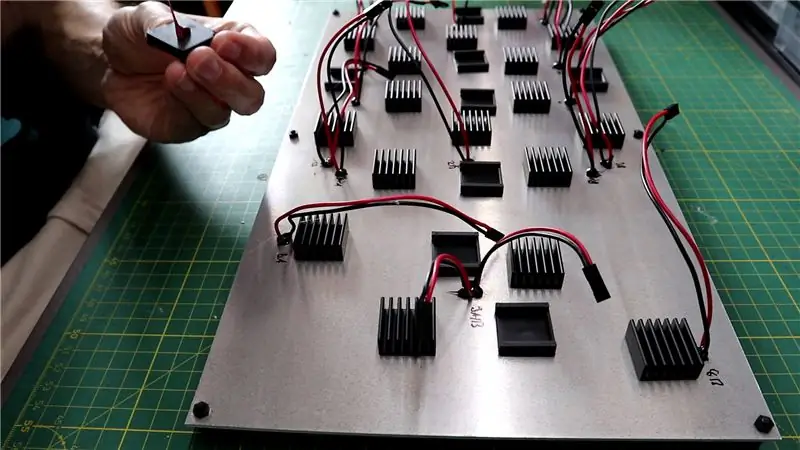
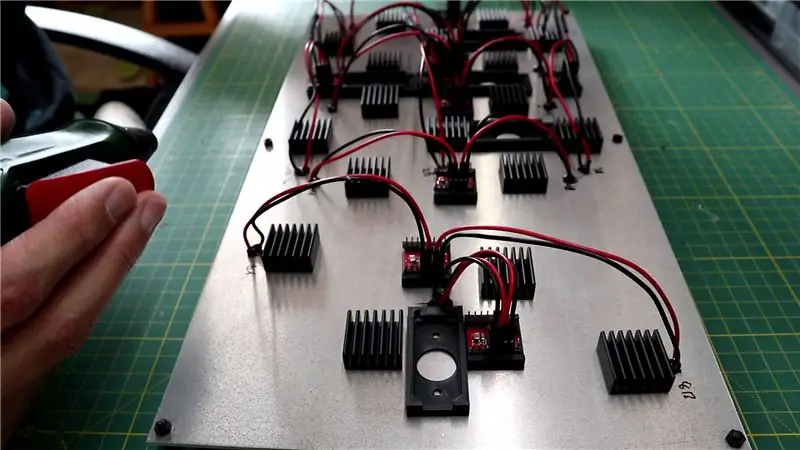
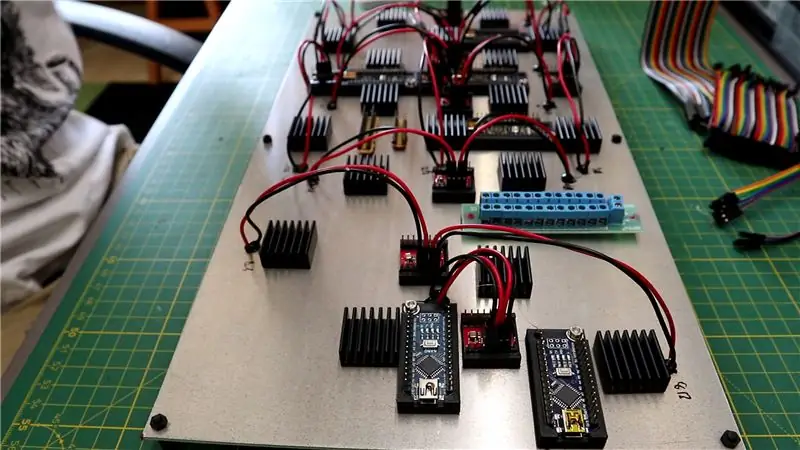
Mijn oorspronkelijke idee was om de aluminium plaat gewoon als koellichaam voor de peltiers te gebruiken, zelfs zonder ventilator. Ik dacht dat de totale temperatuur van de plaat maar een klein beetje zou stijgen omdat sommige segmenten worden gekoeld en andere worden verwarmd. Het bleek echter dat zonder extra heatsinks en geen koelventilator de temperatuur zo hoog blijft oplopen dat de koperplaten niet meer afgekoeld kunnen worden. Dit is vooral problematisch omdat ik geen thermistoren gebruik om het verwarmings-/koelvermogen te regelen, maar altijd een vaste waarde gebruik. Daarom kocht ik kleine koellichamen met een zelfklevende pad die achter elke peltier aan de achterkant van de aluminium plaat werden vastgemaakt.
Daarna werden ook 3D-geprinte houders voor de motordrivers en arduino's met hotglue aan de achterkant van de plaat bevestigd.
Stap 7: Code uploaden
Elke Arduino kan maximaal twee motordrivers besturen, omdat ze twee PWM- en 5 digitale IO-pinnen nodig hebben. Er zijn ook motordrivers die via I2C kunnen worden bestuurd (zie hier), maar deze zijn niet compatibel met de 5 V-logica van de arduino's. In mijn circuit is er één "master" arduino die via I2C communiceert met 5 "slave" arduino's die op hun beurt de motorstuurprogramma's besturen. De code voor de arduino's is hier te vinden op mijn GitHub-account. In de code voor de "slave" arduino's moet het I2C-adres voor elke arduino in de header worden gewijzigd. Er zijn ook enkele variabelen die het mogelijk maken om het verwarmings-/koelvermogen en de bijbehorende tijdconstanten te wijzigen.
Stap 8: Bedrading Waanzin
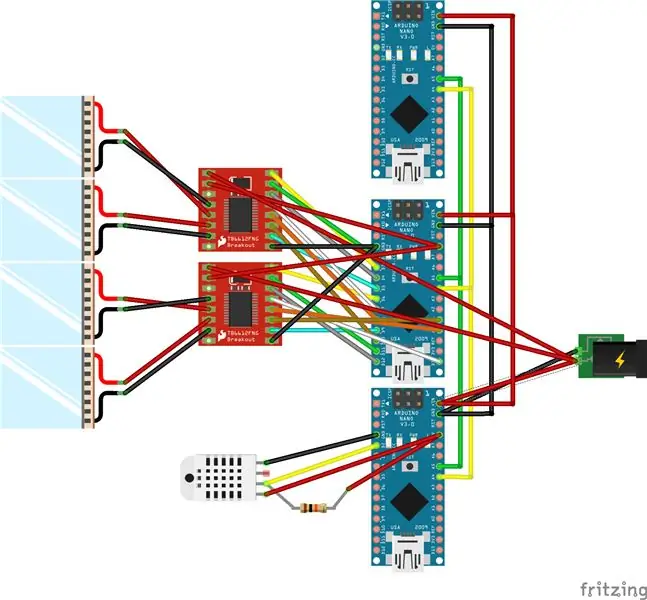
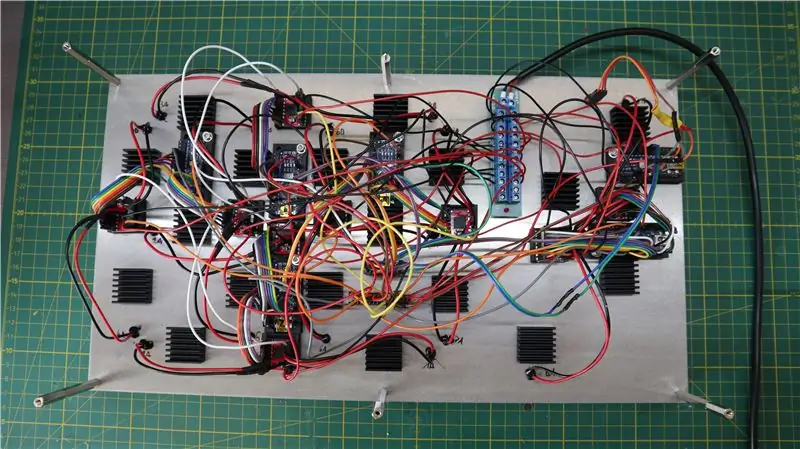
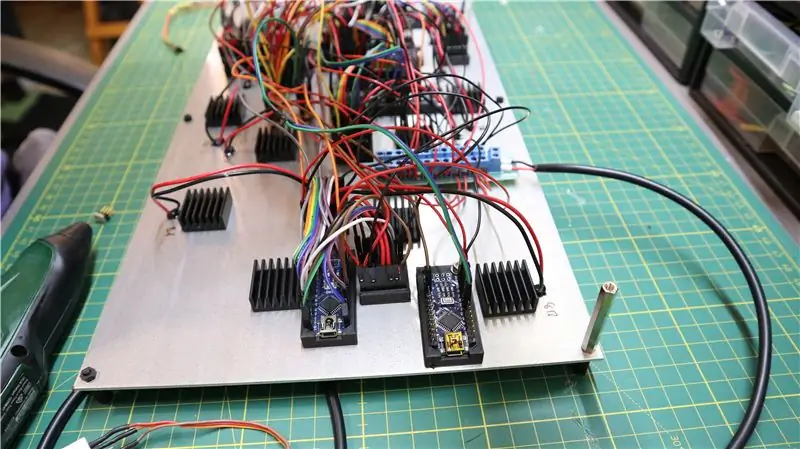
De bedrading van dit project was een totale nachtmerrie. Ik heb een fritzing-diagram bijgevoegd dat de aansluitingen voor de master-arduino en een enkele slave-arduino als voorbeeld laat zien. Daarnaast is er een pdf die documenteert welke TEC is aangesloten op welke motor driver en arduino. Zoals je op de foto's kunt zien wordt door de grote hoeveelheid aansluitingen de bedrading erg rommelig. Ik gebruikte dupont-connectoren waar het mogelijk was. De 12 V-voeding werd verdeeld via een printplaat met schroefklemmen. Op de stroomingang heb ik een DC-kabel met losse kabels bevestigd. Om de 5 V-, GND- en I2C-verbindingen te verdelen, heb ik enkele prototype-printplaten uitgerust met mannelijke pin-headers.
Stap 9: Acrylplaat voorbereiden
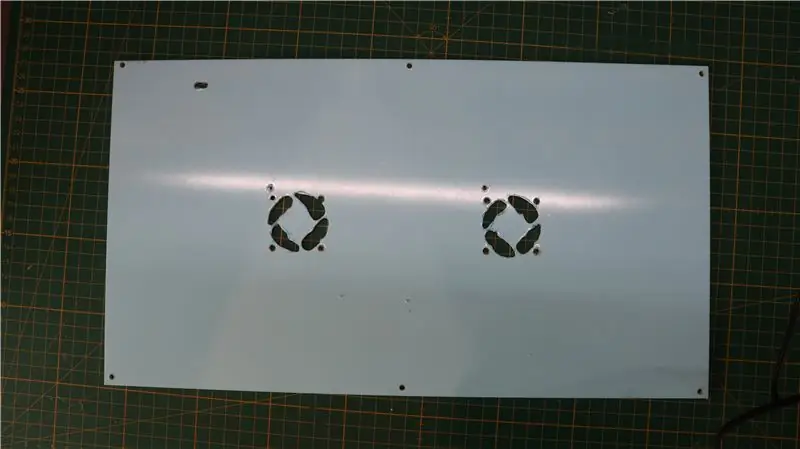
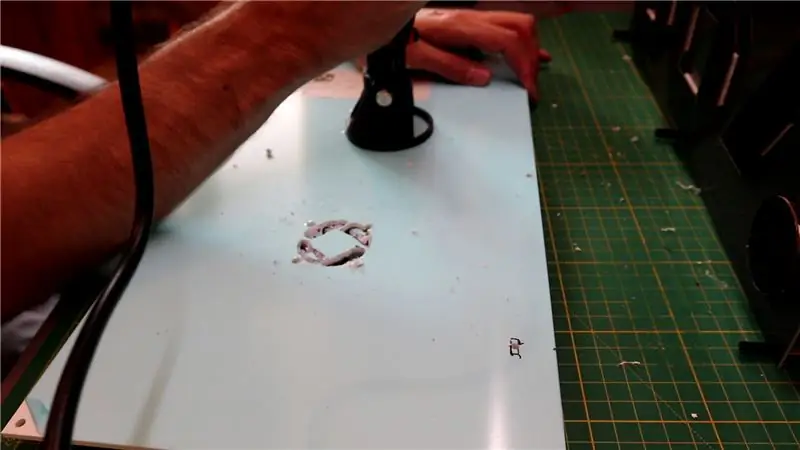
Vervolgens heb ik enkele gaten in de acrylplaat geboord, zodat deze via PCB-afstandhouders aan de aluminiumplaat kan worden bevestigd. Daarnaast wat uitsparingen gemaakt voor de ventilatoren en een gleuf voor de DHT22 sensorkabel met mijn dremel gereedschap. Daarna werden de ventilatoren aan de achterkant van de acrylplaat bevestigd en werden de kabels door een aantal gaten geleid die ik had geboord. De volgende keer zal ik waarschijnlijk de plaat maken door te lasersnijden.
Stap 10: Voltooid project
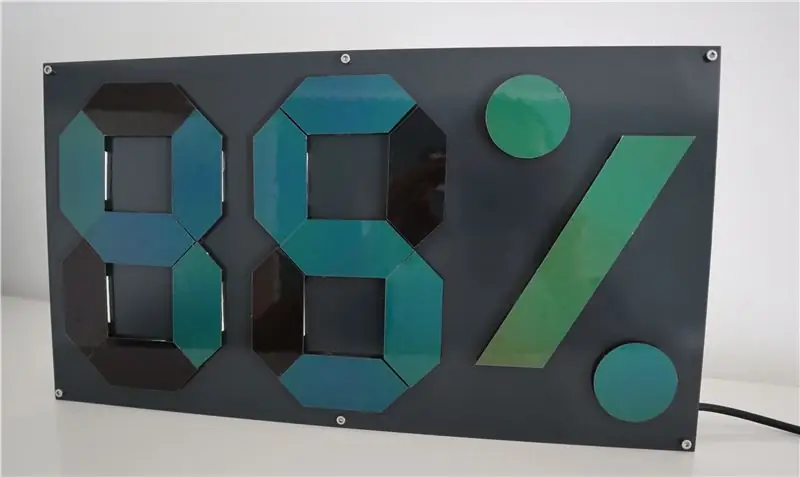
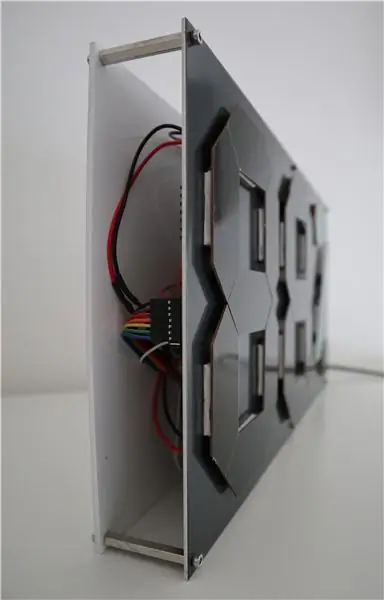
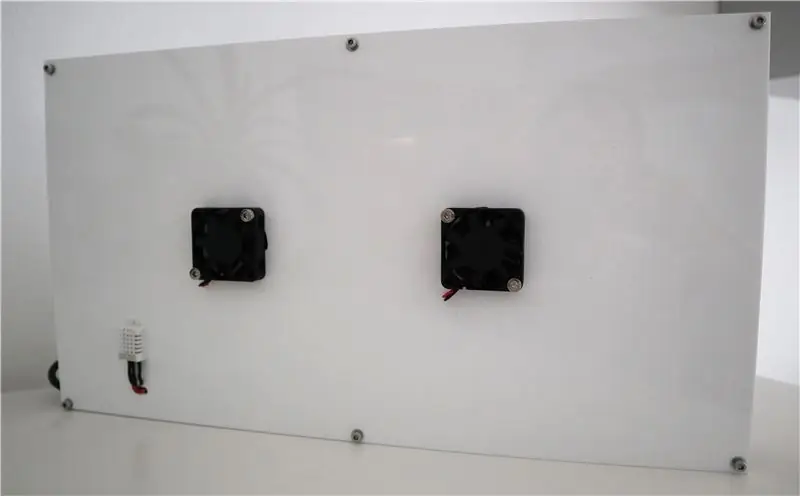
Ten slotte werden de acrylplaat en aluminiumplaat aan elkaar bevestigd met behulp van 40 mm lange PCB-afstandhouders. Daarna is het project af.
Bij aansluiting op de voeding geven de segmenten afwisselend de temperatuur en vochtigheid weer. Voor de temperatuur zal alleen de bovenste stip van kleur veranderen terwijl ook het streepje en de onderste stip gemarkeerd zijn bij het tonen van de vochtigheid.
In de code wordt elk actief segment gedurende 25 seconden verwarmd terwijl tegelijkertijd de niet-actieve segmenten worden gekoeld. Daarna worden de peltiers 35 seconden uitgeschakeld zodat de temperatuur weer kan stabiliseren. Desalniettemin zal de temperatuur van de koperplaten na verloop van tijd stijgen en het duurt even voordat de segmenten een volledige kleurverandering ondergaan. Het stroomverbruik voor een enkel cijfer (7 segmenten) werd gemeten op ongeveer 2 A, dus het totale stroomverbruik voor alle segmenten ligt waarschijnlijk in de buurt van het maximum van 6 A dat de voeding kan leveren.
Men zou het stroomverbruik zeker kunnen verminderen door thermistoren toe te voegen als feedback om het verwarmings-/koelvermogen aan te passen. Een stap verder gaan zou zijn om een speciale TEC-controller met PID-lus te gebruiken. Dit zou waarschijnlijk een constante werking mogelijk moeten maken zonder veel stroomverbruik. Ik denk er momenteel over om zo'n systeem te bouwen met behulp van Thorlabs MTD415T TEC-stuurprogramma's.
Een ander nadeel van de huidige configuratie is dat men de 1 kHz PWM-uitgang van de motordrivers kan horen. Het zou ook leuk zijn als je de fans kwijt zou kunnen raken, omdat ze ook behoorlijk luid zijn.
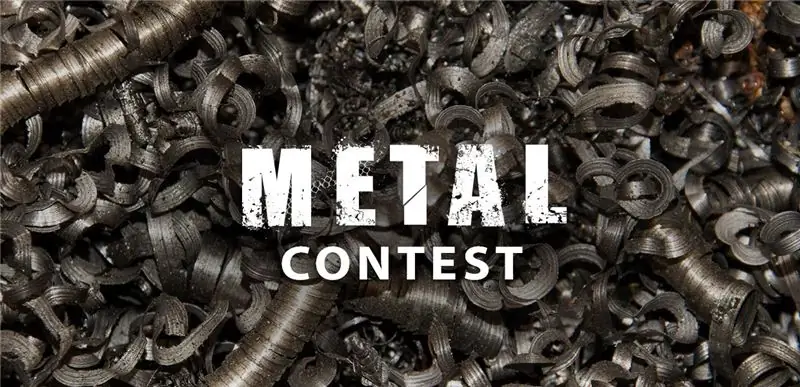
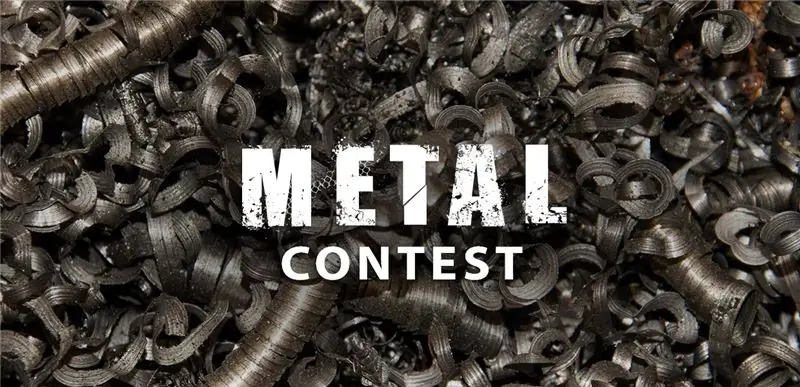
Eerste prijs in de metaalwedstrijd
Aanbevolen:
Aan de slag met draadloze temperatuur- en trillingssensoren met groot bereik: 7 stappen
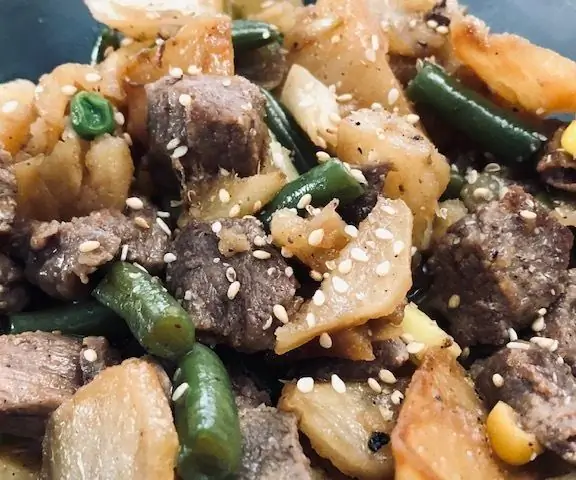
Aan de slag met draadloze temperatuur- en trillingssensoren met groot bereik: Soms zijn trillingen de oorzaak van ernstige problemen in veel toepassingen. Van machineassen en lagers tot de prestaties van de harde schijf, trillingen veroorzaken schade aan de machine, vroegtijdige vervanging, lage prestaties en veroorzaken een grote aanslag op de nauwkeurigheid. Toezicht houden
Temperatuur- en lichtsensor: 8 stappen
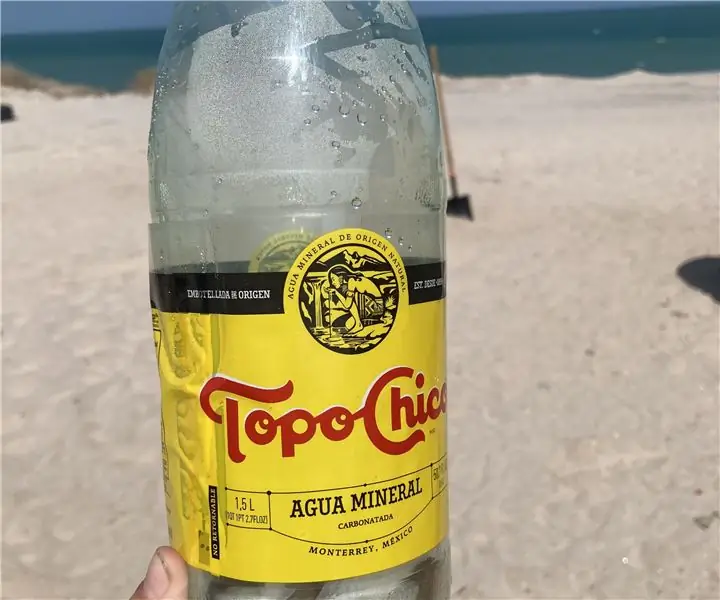
Temperatuur- en lichtsensor: dit instructable is voor een basistemperatuur- en lichtsensor. Dat is het zo'n beetje
Easy Very Low Power BLE in Arduino Part 2 -- Temperatuur-/vochtigheidsmonitor -- Rev 3: 7 stappen
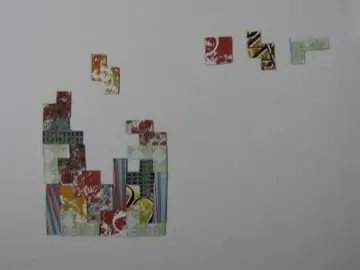
Easy Very Low Power BLE in Arduino Part 2 -- Temperatuur-/vochtigheidsmonitor -- Rev 3: Update: 23 november 2020 – Eerste vervanging van 2 x AAA-batterijen sinds 15 januari 2019 dwz 22 maanden voor 2xAAA AlkalineUpdate: 7 april 2019 – Rev 3 van lp_BLE_TempHumidity, voegt datum-/tijdplots toe, met behulp van pfodApp V3.0.362+, en automatische beperking van
De temperatuur meten: 7 stappen
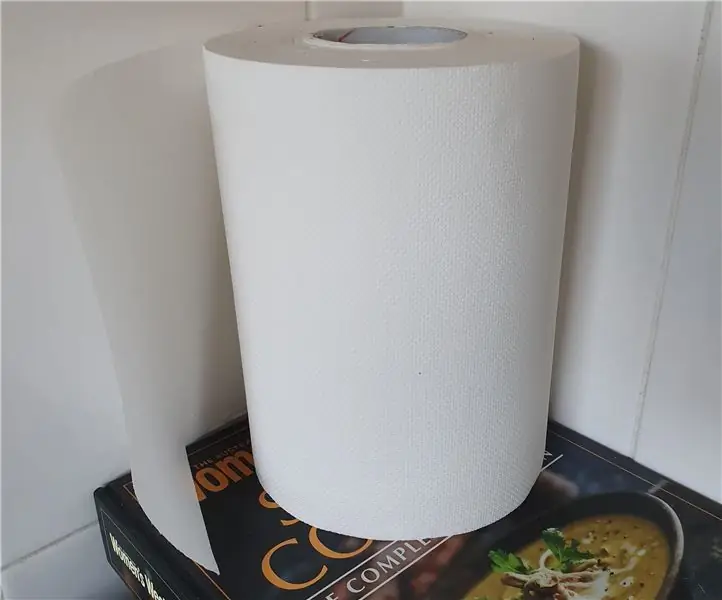
De temperatuur meten: هو قياس درجه الحراره باستخدام الكاميرا االحراريه
Thermochrome patronen: 7 stappen (met afbeeldingen)
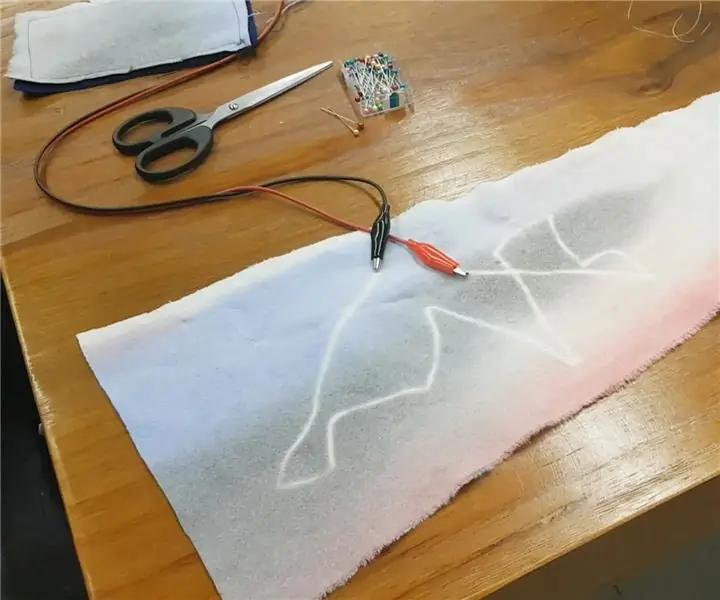
Thermochrome patronen: Als u op zoek bent naar een nieuw materiaal om mee te ontwerpen, dan is thermochrome verf misschien precies wat u zoekt. Volg deze tutorial om te leren hoe u interactieve thermochrome ontwerpen kunt maken