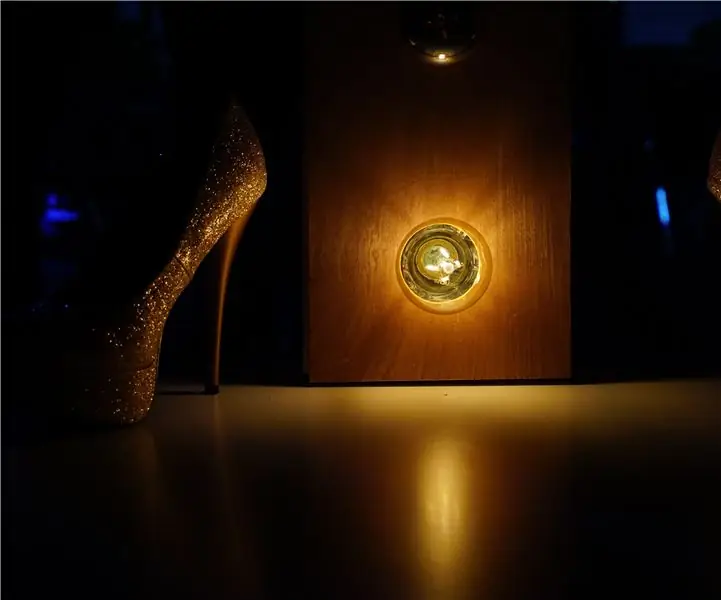
Inhoudsopgave:
- Benodigdheden
- Stap 1: 5V-schakeling: Arduino
- Stap 2: De doos ontwerpen
- Stap 3: De doos bouwen
- Stap 4: De stopcontacten in de doos installeren
- Stap 5: Solderen van de laagspanningselektronica
- Stap 6: De 220V-componenten aansluiten
- Stap 7: Magnetische snappers (optioneel)
- Stap 8: Wat ik anders zou doen?
2025 Auteur: John Day | [email protected]. Laatst gewijzigd: 2025-01-23 15:01
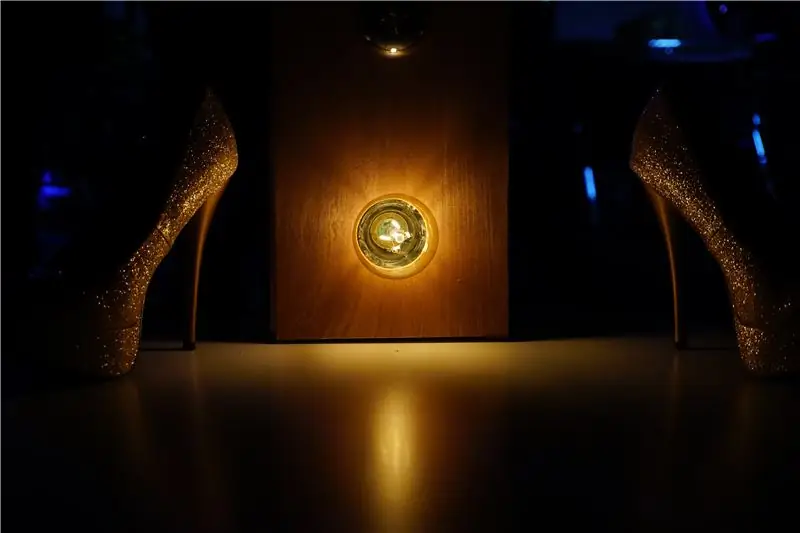
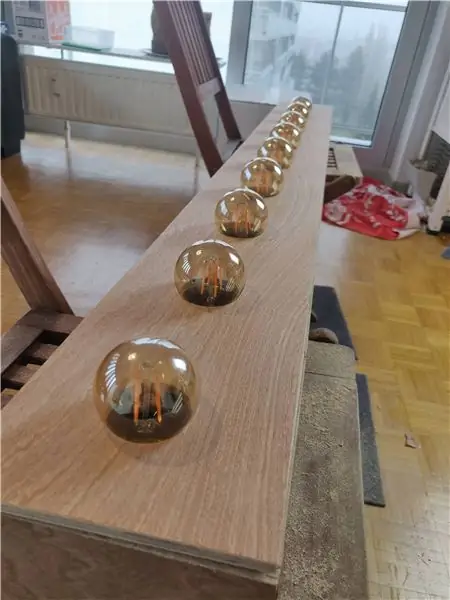
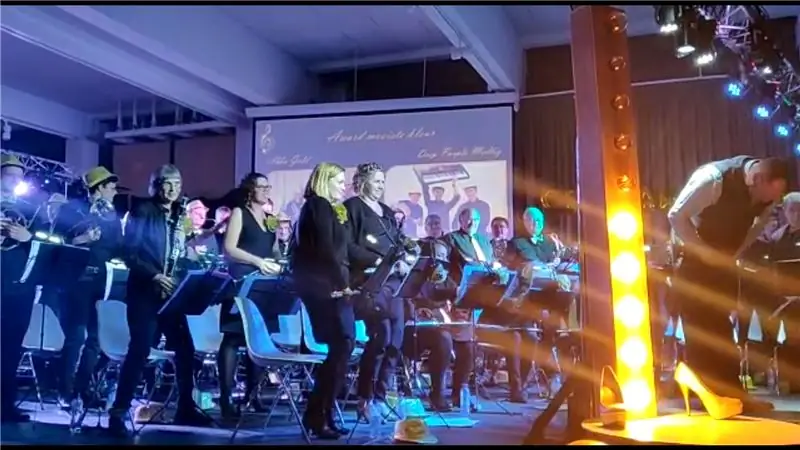
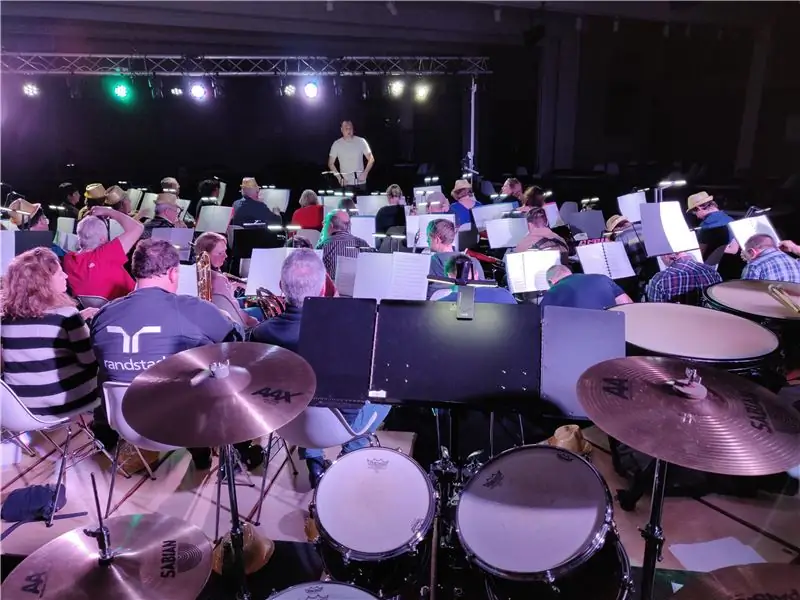
Sinds ergens rond het jaar 2001 ben ik begonnen met drumlessen. Na tien jaar, in 2011, trad ik toe tot mijn eerste harmonieorkest en was ik verkocht. Samen muziek maken en meespelen bij een concert is spannend. Nu zit ik al meer dan 5 jaar bij een ander harmonieorkest. We hebben twee concerten per jaar en verschillende commissies erbij.
Als thema van ons nieuwjaarsconcert wilden we een prijsuitreiking houden voor de beste nummers die we hebben gespeeld. De opzet was dat we in elke categorie twee nummers speelden. Bijvoorbeeld "Ice versus fire" waarvoor we een medley speelden van "Frozen" en een van "How to train your dragon". Het publiek zou dan moeten stemmen op het beste nummer, dat vervolgens een op maat gemaakte 3D-geprinte prijs zou krijgen.
Tijdens het brainstormen tijdens de voorbereidingen hadden we veel ideeën om het publiek te laten stemmen, van papieren stemmen tot apps. Maar al die suggesties vereisen dat de show voor elke prijs wordt stopgezet, terwijl het publiek ernstig wordt afgeleid. Toen er een applausmeter werd voorgesteld, wisten we allemaal dat we goud bereikten. Maar wat online zoeken bracht geen echte kant-en-klare oplossing aan het licht. Dus ik stond dapper op, verklaarde mezelf een beginnende maker en beweerde dat ik er gemakkelijk een helemaal opnieuw kon bouwen voor een vrij klein budget.
Oh boy, wat was ik niet voorbereid op het konijnenhol waar ik in zou vallen.
Benodigdheden
Gereedschap
- Je favoriete accuboormachine
- Cirkelboor en andere bits:
- schroevendraaiers
- 3D-printer (optioneel)
Geval
- Multiplex. (Ik kies 8 mm multiplex maar achteraf gezien had ik voor 12 mm of zelfs dikker moeten gaan)
- 4 X Magnetische Deurvanger (achteraf optioneel)
- Schroeven
Elektronica (5V)
- Arduino Nano
- Electret-microfoonversterker - MAX4466 met instelbare versterking (of vergelijkbaar, wat bij uw behoeften past)
- 2 X 5V 8-kanaals relaismodule
- 220V naar 5V transformator
- draden, veel korte, en één vieraderige draad van enkele meters voor de 'afstandsbediening'
- twee schakelaars
Elektronica (220V)
- standaard elektrische kabels (resten van woningbouw zijn ideaal, maar het beste flexibel)
- Gezekerd stopcontact (optioneel maar sterk aanbevolen)
- Lampen naar keuze
- Gloeilampen
Stap 1: 5V-schakeling: Arduino
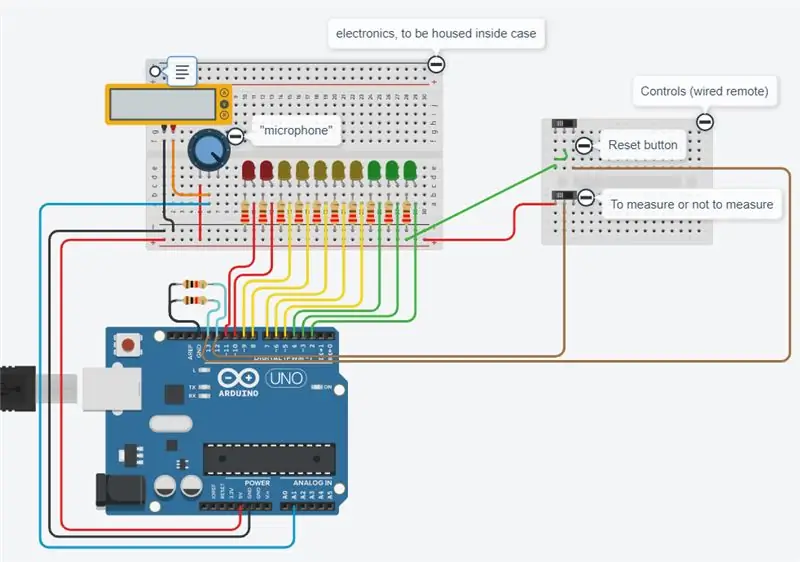
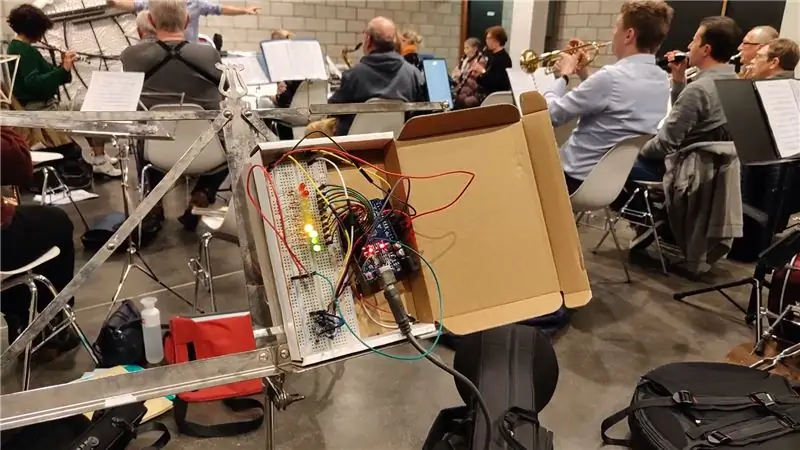
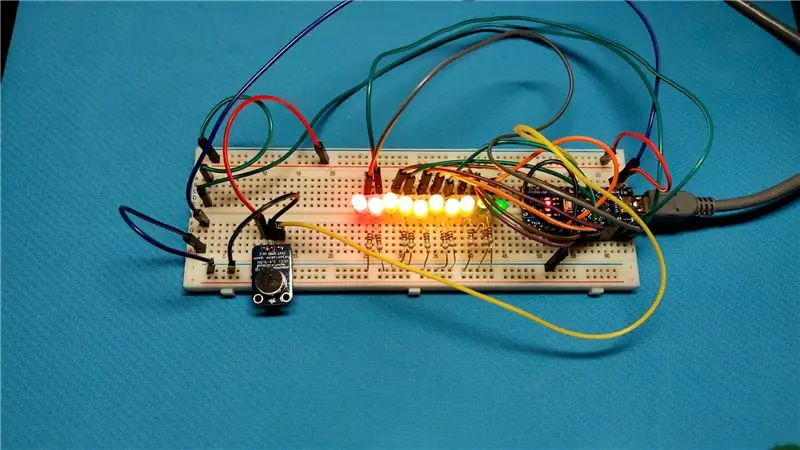
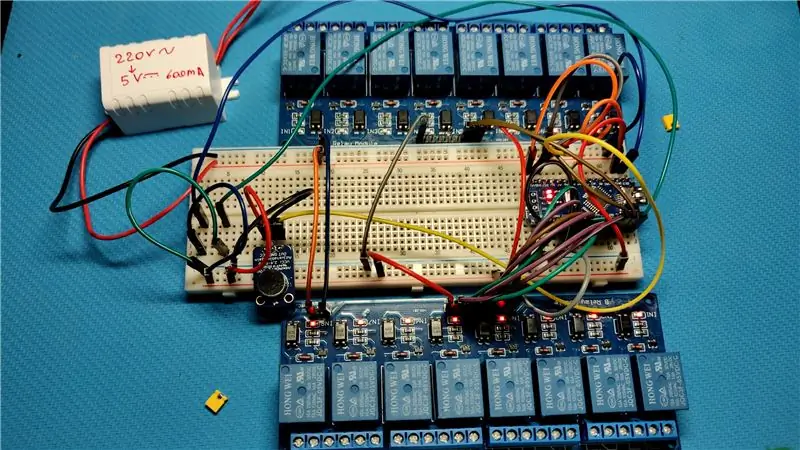
Deze build bestaat uit drie hoofdonderdelen: (1) de 5V-elektronica die het "harde denken" zal doen: luisteren en beslissen wanneer en welke lichten moeten worden ingeschakeld; (2) de behuizing om alles mooi in te passen, verbergt alle 'misdaden', en (3) het 220V-circuit dat wordt aangestuurd door het 5V-circuit.
Laten we beginnen met de 5V-schakeling, omdat we deze op kleine schaal kunnen bouwen.
Het was geen gemakkelijke taak om online bronnen te vinden. Ik stelde me tien lampjes voor, die oplichtten naargelang het luide applaus, maar niemand leek dit eerder te hebben gedaan. Dus ik begon klein; Op tinkerCAD heb ik een online simulatie gebouwd van hoe ik wilde dat de 5V elektronische onderdelen eruit zouden zien. Je kunt mijn zeer rudimentaire ontwerp met code hier vinden: https://www.tinkercad.com/things/8mnCXXKIs9M of hieronder op deze pagina als "Applause_1.0.ino" bestand.
Het online maken van een conceptversie en het testen van verschillende Arduino-codes op deze simulatie heeft me echt geholpen om een beter beeld te krijgen van wat er nodig was voor deze build. Op deze manier heb ik geëxperimenteerd met het toevoegen van een manier om het gedrag van het programma te regelen: ik eindigde met twee schakelaars. De ene schakelaar zet de meting aan en uit, de andere zet de score terug naar 0/10.
Ik heb alle benodigde componenten voorzien: enkele LED's, weerstanden, een Arduino en vooral een Arduino-compatibele microfoon.
Ik bouwde het circuit en testte alles bij de volgende repetitie, om te beseffen dat de microfoon die ik kocht veel te gevoelig was voor mijn gebruik. Slechts één klap op redelijke afstand, of alleen de band die speelt, zou de microfoon verzadigen en een score van 10/10 geven. Dit bracht me ertoe om te zoeken naar een microfoon met variabele versterking. Ik heb uiteindelijk gekozen voor de Electret-microfoonversterker - MAX4466. Het heeft een heel klein schroefje aan de achterkant waarmee je de gain kunt instellen. (kanttekening: ik heb ook zonder enige reden de Arduino uno vervangen door een Arduino Nano).
De MAX4466 presteerde beter, maar was ook maximaal bij het dichtklappen van dichtbij, daarom besloot ik om ook de klaptijd als variabele in de formule op te nemen in plaats van alleen de luidheid van het applaus. Ik heb ook een beetje meer elegante code geschreven voor deze versie 2.0 van de software (al zeg ik het zelf). Als een luidheidsdrempel werd overschreden, ging alleen het eerste licht aan, gevolgd door een korte pauze waarin geen lichten aan konden gaan. Na het wachten zou de Arduino luisteren of het geluid nog steeds luid genoeg was om het tweede lampje aan te laten gaan, zo ja, dan gaat het lampje branden en wordt de volgende wachttijd geactiveerd. Elke keer dat er een nieuw lampje ging branden, nam de wachttijd toe. Een applaus zou 22,5 seconden op vol volume moeten duren voordat de lichten 10/10 aangeven. Je kunt de code vinden op tinkerCAD https://www.tinkercad.com/things/lKgWlueZDE3 of hieronder als "Applause_2.0.ino" bestand
Een snelle test met de relaismodules aangesloten in plaats van de LED's leerde me dat de relais AAN waren als het signaal LAAG was en UIT waren als het signaal HOOG was. Geen probleem, gewoon wat AAN en UIT in de code uitschakelen en we waren klaar om te gaan.
Met dit alles geregeld. Ik zou alles aan elkaar kunnen solderen. Maar ik moest weten hoe lang alle verbindingen in de doos zouden moeten zijn. Laten we dus eerst de buitendoos bouwen en alle componenten daarin rangschikken.
Stap 2: De doos ontwerpen
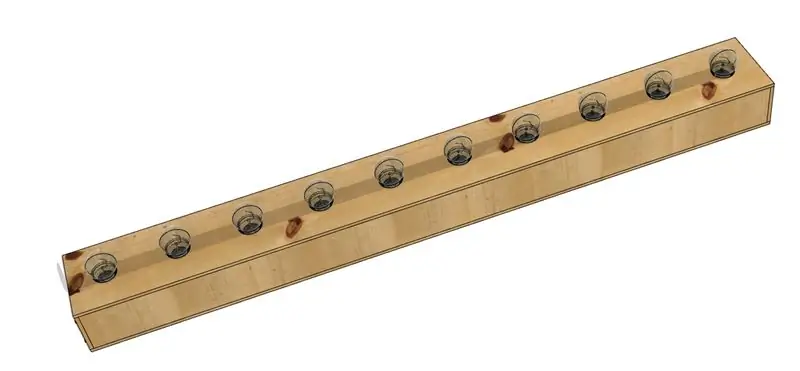
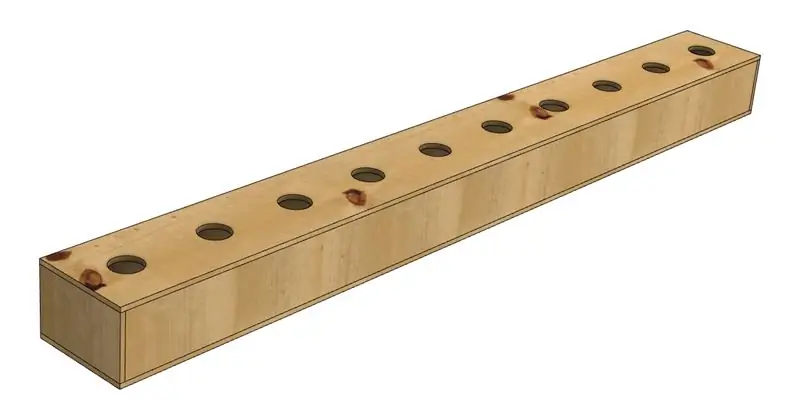
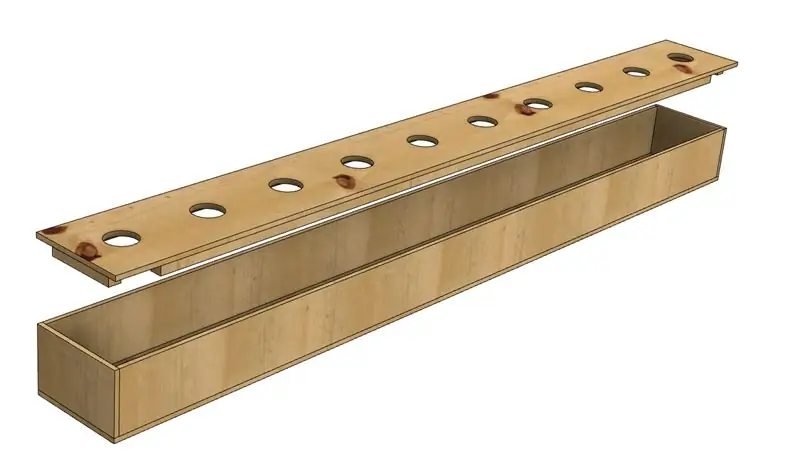
Een tweede aspect van deze constructie was de esthetiek. De applausmeter zou midden in de belangstelling staan dus het moest er in ieder geval goed uitzien. Ik heb ervoor gekozen om een houten kist te bouwen, omdat ik er het basisgereedschap voor heb en het relatief eenvoudig is.
Nadat ik op tinkerCAD had geleerd dat experimenteren in de digitale wereld zeer leerzaam is, ontwierp ik ook de applausmeterkast in het populaire 3D-CAD-programma Fusion360 voordat ik een van de benodigde materialen kocht.
In de loop van verschillende iteraties kwam ik uiteindelijk tot dit ontwerp (zie foto's). Het is een eenvoudige rechthoekige doos met de lichten die uit ronde gaten in het voorpaneel steken.
Lelijke schroeven in het voorpaneel werden vermeden door enkele steunbalken aan de binnenkant van het voorpaneel toe te voegen, waar later magnetische deurklikkers in zouden worden geschroefd. Het magnetische sluitsysteem is achteraf gezien meer een veiligheidsvoorziening dan een echt noodzakelijke, aangezien de staven de voorplaat alleen door wrijving op hun plaats hielden, prima.
Ik heb ook de elektronica toegevoegd aan mijn digitale ontwerp. Dit veranderde een aantal dingen, dus het wierp al vruchten af dat ik het eerst in Fusion360 ontwierp. De doos moest bijvoorbeeld iets breder zijn dan de oorspronkelijke 15 cm om de relais zijdelings te laten passen. Ik ben ook geëindigd met het modelleren en 3D-printen van plastic houders voor de lichtfittingen die op hun beurt de lichten op hun plaats zouden houden. Dit leek me de optie die me genoeg 'speelruimte' zou geven voor toekomstige fouten. (Ik weet dat deze houders ook als zodanig kunnen worden gekocht, maar dit kostte me drie keer meer en ik had een beperkt budget)
Ik heb het F360-bestand van mijn definitieve ontwerp hier toegevoegd zodat u ernaar kunt verwijzen en ermee kunt spelen.
Stap 3: De doos bouwen
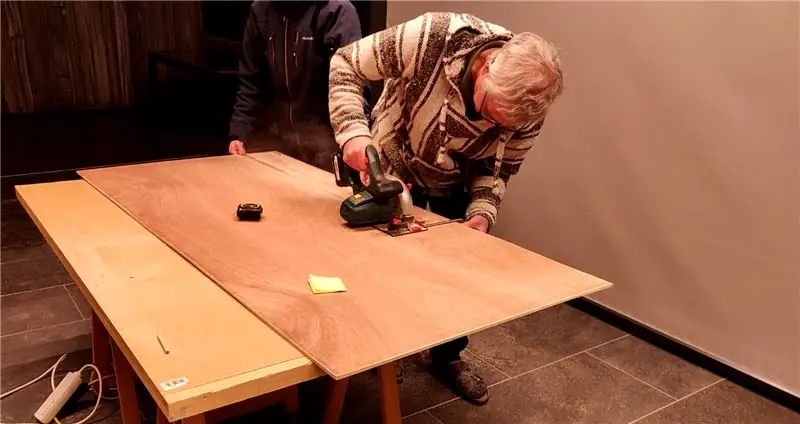
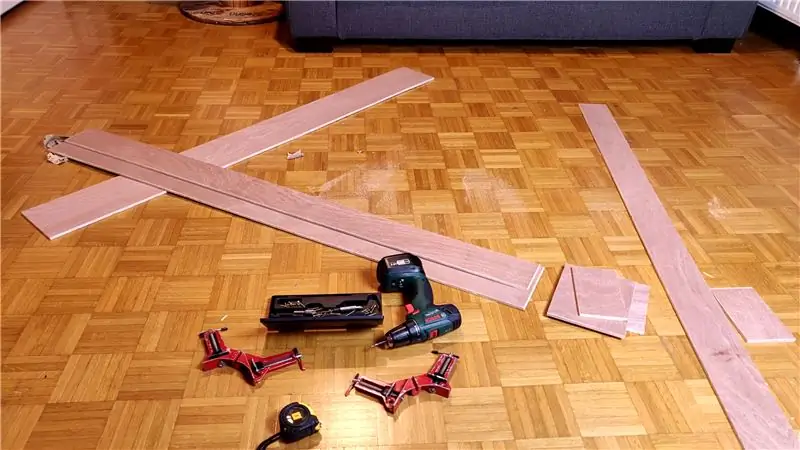
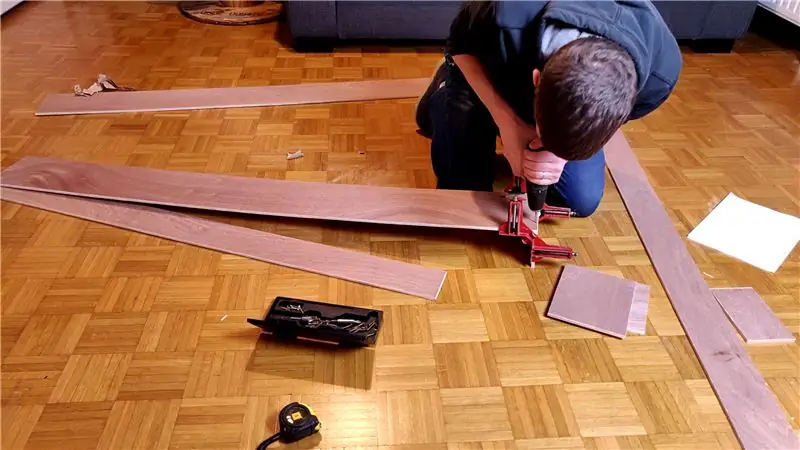
Toen het digitale ontwerp klaar was, was het tijd om naar de ijzerhandel te gaan, een groot stuk triplex te kopen en te beginnen met zagen. Omdat ik niet echt zulke 'felle' gereedschappen bezat, ging ik een weekend naar de plaats van mijn ouders en zaagde daar het hout op maat.
Mijn ontwerp leverde echter een vrij exotisch snijblad op:
- 2 keer 16,6x150cm voor de voor- en achterkant
- 2 keer 16,6x10,2cm voor de boven- en onderkant
- 2 keer 10,2x148.4cm voor de zijkanten
De steunbalken aan de binnenkant van het voorpaneel waren restanten en werden als zodanig gebruikt, anders zou de gewenste lengte 134 cm en 12 cm zijn geweest.
Eenmaal thuis heb ik alle onderdelen op de vloer gelegd en met behulp van enkele (geleende) hoekklemmen begonnen met het voorboren van gaten en het aan elkaar schroeven van de planken. Onthoud dat schroeven alleen in de boven-, onder- en achterkant van de meter passen voor pure esthetische reacties.
Het boren van de gaten en het aan elkaar schroeven van alle planken was een hachelijke taak omdat het triplex slechts 8 mm dun was, ik vervloekte mezelf vaak omdat ik dacht dat 8 mm dik genoeg zou zijn.
Het voorpaneel had enkele zorgvuldig uit elkaar geplaatste gaten van ongeveer 5 cm diameter nodig. Ik markeerde de middellijn van het voorbord en begon vanaf één kant. Het midden van het eerste gat was 8 mm (de materiaaldikte) + 75 mm (de helft van 150 mm) vanaf de rand van het bord. Alle andere gaten zijn 150 mm uit elkaar. Uiteindelijk zat ik er maar 2 mm naast toen ik het tiende gat markeerde… het was een goede dag!
De enige cirkelvormige boor die ik kon lenen was 51 mm, meer dan dichtbij genoeg om met plezier te beginnen met boren.
De frontplaatgeleiders werden aan de binnenzijde van de frontplaat vastgelijmd met eenvoudige houtlijm.
Stap 4: De stopcontacten in de doos installeren
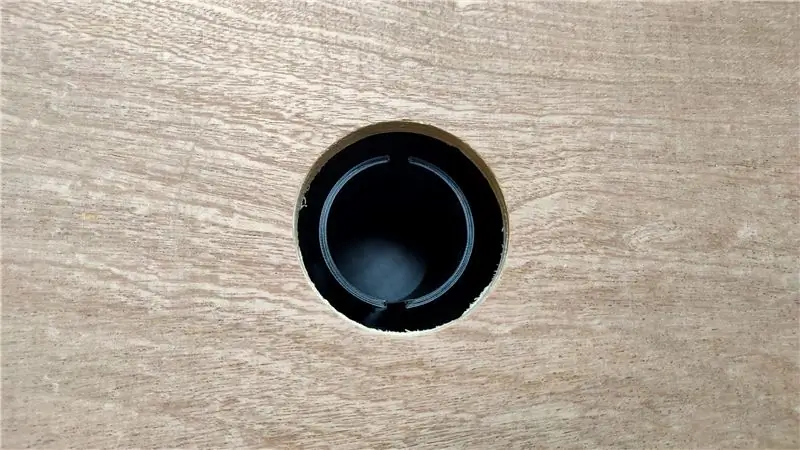
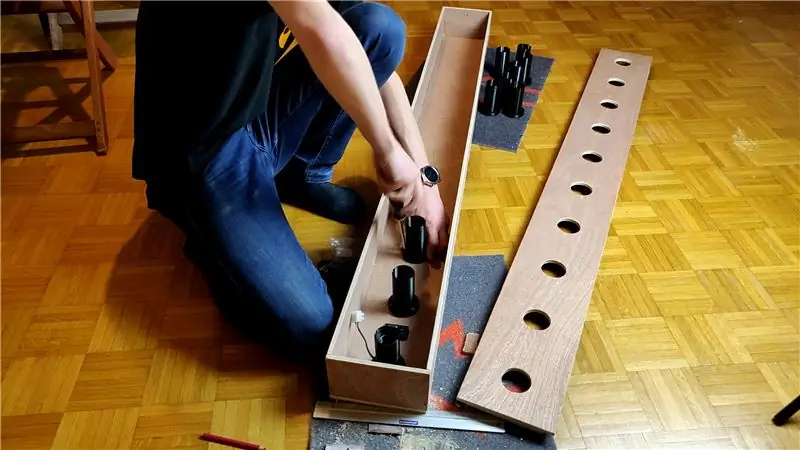
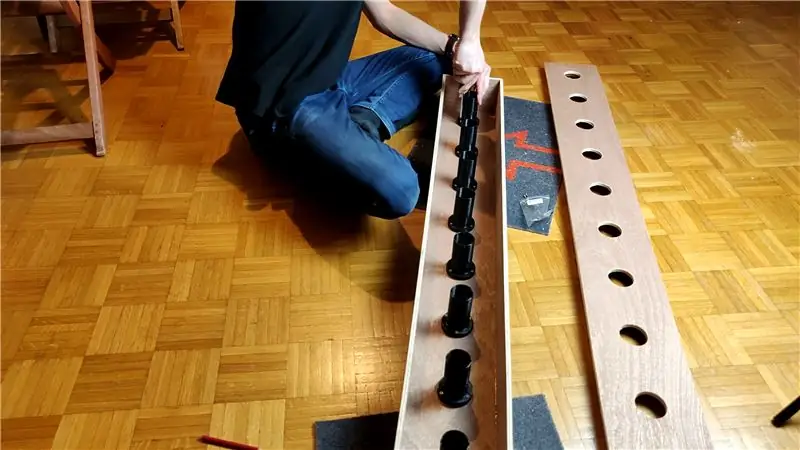
De eerste componenten die in onze nieuw gebouwde doos worden gemonteerd, zijn de licht-contactdooshouders. De reden hiervoor is dat de houders gecentreerd onder elk gat in de frontplaat moeten worden geplaatst. Omdat de houder de fittingen op hun plaats houdt, waar op hun beurt de gloeilampen in worden geschroefd, en de gloeilampen letterlijk het enige zijn dat uit het voorpaneel steekt en dus het enige zijn dat niet kan worden verplaatst naar een andere positie in onze box. Omdat hun positie vast staat, moeten ze als eerste naar binnen, om te voorkomen dat ik later een stomme fout maak.
Zoals ik eerder al zei, zijn er in de handel verkrijgbare lichtfittingen met een geïntegreerde beugel om ze loodrecht op een muur te monteren, maar deze kosten 4 keer meer dan de eenvoudige die gemaakt zijn om gewoon aan het plafond te hangen zonder zelfs maar een zwakke poging te doen om er mooi uitzien. Dus ging ik voor een goedkope en 3D-geprinte houder voor de stopcontacten. (STL-bestand hieronder). Bij het maken van het 3D-ontwerp heb ik ervoor gezorgd dat er voldoende 'wiebel' ruimte zou zijn om de stopcontacten op verschillende dieptes te plaatsen.
Ik heb slechts één houder afgedrukt om het ontwerp te verifiëren. Daarna heb ik 9 houders tegelijk geprint, waardoor mijn hele bouwplaat volledig werd gevuld en uiteindelijk meer dan 50 uur meeging.
Ik heb willekeurig de boven- en onderkant van de voorplaat en de doos gemarkeerd (onthoud dat ik maar liefst 2 mm afwijking kreeg tussen het digitale ontwerp en de realiteit). Toen begon ik met het moeizame proces van het centreren van een houder met het deksel op zijn plaats, voorzichtig de voorkant optillen, de positie markeren met potlood en naar de volgende houder gaan. Toen alles was gezegd en gedaan, controleerde ik elke positie opnieuw voordat ik ze uiteindelijk in de achterplaat schroefde.
Een opmerking over schroeven: mijn houderontwerp heeft een vrij dikke basis, dit is met opzet gedaan om ervoor te zorgen dat mijn 16 mm lange schroeven niet uit de achterkant van mijn 8 mm achterplaat steken. Nog een reden om voor dikker multiplex te gaan. (Vergeet "leven, liefhebben, lachen", het is "leven, liefhebben en leren").
Hoe dan ook, de lichtcontactdozen waren aan de beurt. Ik koos de gewenste hoogte waarbij ik de gloeilampen boven het voorpaneel wilde laten uitsteken, en mat vervolgens de diepte van de fittingen, opnieuw door alles voorzichtig te positioneren terwijl de voorkant gesloten is en het op te tillen en te meten. Een klein detail: ik moest eerst een stuk van het kabeluiteinde losschroeven en afbreken van alle stopcontacten die dienden als trekontlasting voor de kabels wanneer ze afschuwelijk aan het plafond hingen, maar aangezien ik ze in op maat gemaakte bedrukte houders monteerde, ze dienden helemaal geen functie voor mij. Erger nog, de trekontlasting zorgde ervoor dat de kabels weerstand boden aan de krappe bocht waarin ik ze dwong, waardoor ze hun werk perfect deden, … dus de trekontlasting moest worden geëlimineerd om de sockets in de houders te laten passen zoals ik wilde.
Ik lijmde alle sockets in de houders en liet het een nacht staan met elastiekjes die druk uitoefenden. Natuurlijk was ik fabelachtig vergeten dat ik 9 normale gloeilampen had gekocht en een dikke voor het tiende licht, dit grotere licht is meer bolvormig in plaats van peervormig, waardoor een fitting nodig is die dichter bij de voorkant van de doos is geplaatst dan alle andere lampen.(Leef en leer)
Ik was daarom genoodzaakt om de lijm te breken (slechts een klein beetje mijn 3D-print gebroken) om de socket vrij te maken en te herpositioneren. Na flink wat lijm om zowel de houder te bevestigen als op de juiste hoogte aan de sok te bevestigen, was de montage van de sokkels klaar.
Ik heb ook de connectoren van de lichtfittingen op een van de zijkanten van de achterplaat geschroefd.
Stap 5: Solderen van de laagspanningselektronica
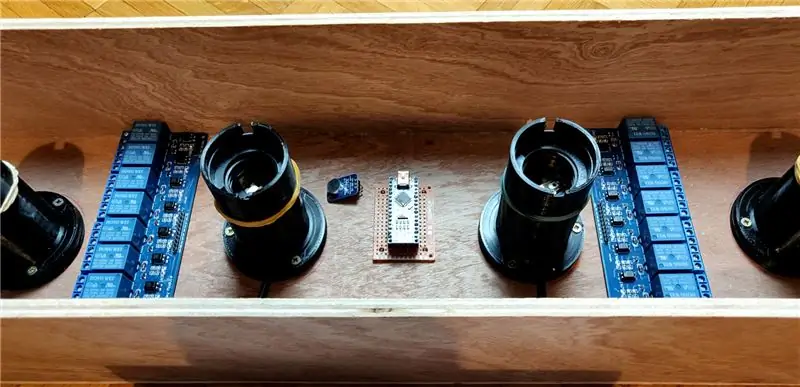
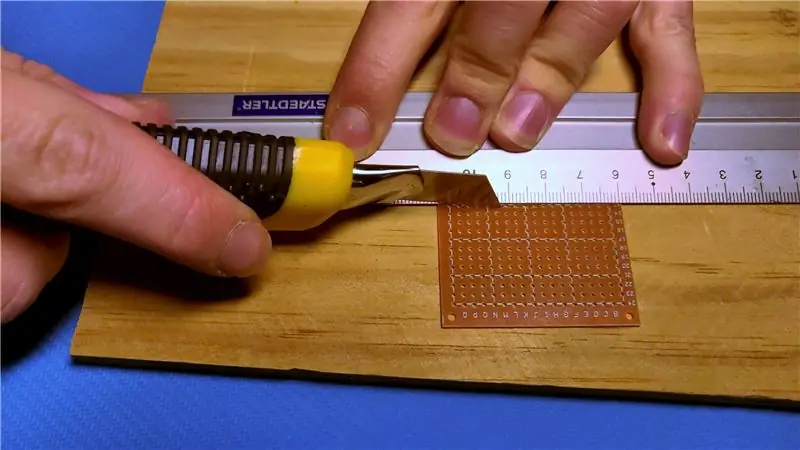
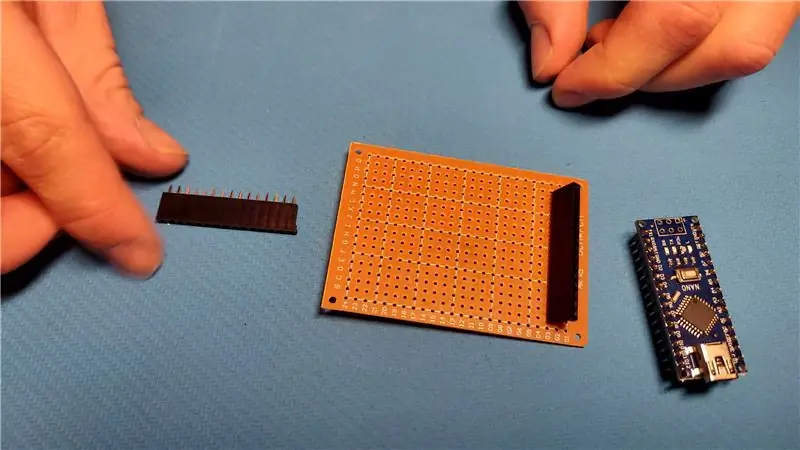
De volgende opdracht is het "dry-fitten" van alle laagspanningselektronica in de doos om een idee te krijgen hoe lang de gesoldeerde verbindingen tussen de onderdelen moeten zijn.
Ik begon door de Arduino in het midden tussen licht 5 en 6 te plaatsen en de relais op de aangrenzende plaatsen boven en onder te rangschikken.
Ik realiseerde me dat er geen houtschroeven door de gaten in de Arduino nano zouden passen. Dit is snel op te lossen door enkele vrouwelijke headers op een soldeerbaar breadboard te solderen. De headers houden de Arduino vast en sommige geboorde gaten in de printplaat accepteren de houtschroeven zonder klachten. Dit soldeerbare bord bevat ook de headers voor de aan te sluiten microfoon, de connectoren (met kabels) om naar de relais te gaan en de lange kabel voor de afstandsbedieningskast.
Over de afstandsbediening; Ik had twee schakelaars nodig aan het einde van een heel erg lange kabel. Ik sta ver achter op het podium als percussionist, terwijl de meter helemaal vooraan op het podium zou staan. Ik heb 20 m 4 gevlochten draad gekocht die meestal wordt gebruikt voor het solderen van LED-strips. Om de twee schakelaars te huisvesten, heb ik een eenvoudige doos ontworpen en in 3D geprint (STL- en F360-bestanden hieronder), maar elke rechthoekige doos met enkele uitsparingen voor de componenten en draden zal het werk doen.
Na het meten van de afstand tussen de componenten en het nemen van een royale overmaat op die afstand, verhitte ik de soldeerbout en begon te solderen.
Het solderen van alle verbindingen vereist wat geduld, en vooral enige concentratie om het goed te doen. Ik heb het bedradingsschema bijgevoegd dat ik heb gebruikt om alle verbindingen te maken, maar houd er rekening mee dat uw bedrading een beetje anders kan zijn als u verschillende componenten gebruikt. (Of als ik een fout heb gemaakt in mijn diagram)
Uiteindelijk zag mijn bedrading eruit alsof er een vogel probeerde te nestelen. Desalniettemin werden er wonderbaarlijk geen fouten gemaakt en begon er niets te roken bij het aanzetten van de stroom.
Met alles aangesloten kon ik elke printplaat op het achterpaneel op 3D-geprinte afstandhouders schroeven. Deze afstandhouders hadden twee functies: (1) het is altijd een goed idee om wat ruimte te laten tussen printplaten en de plaat waarop u ze monteert. En (2) heb ik al geklaagd dat ik 16 mm schroeven en 8 mm multiplex heb, en dat ik daarom constant gevaar loop om schroeven dwars door het hout te schroeven? Ja, de afstandhouders zorgden er ook voor dat mijn schroeven het andere uiteinde van de triplexdoos niet zouden bereiken.
[OPMERKING] Achteraf gezien zou ik eigenlijk aanraden om 5 relais per relaismodule te gebruiken. Mijn idee om twee 8-kanaals relaismodules te gebruiken, was om rekening te houden met een kapot relais, in dat geval zou ik gewoon de verbindingen moeten veranderen en zou de applausmeter weer werken. Dit zou ook de 220V-aansluitingen wat beter verdelen over de twee modules, waardoor het kabelbeheer wat beter … beheersbaar wordt. (Leef en leer)
Stap 6: De 220V-componenten aansluiten
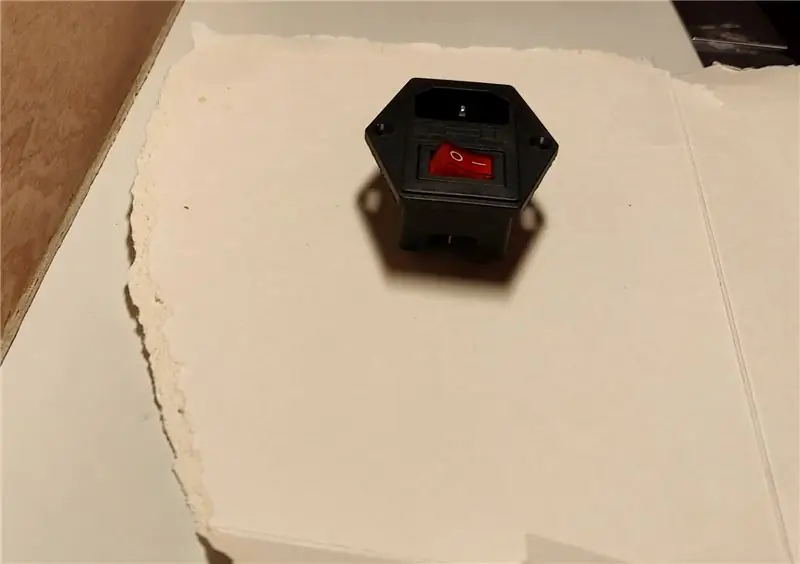
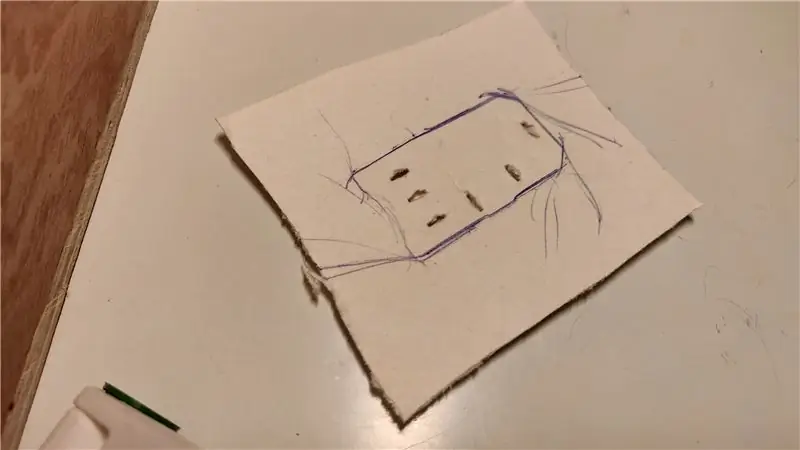
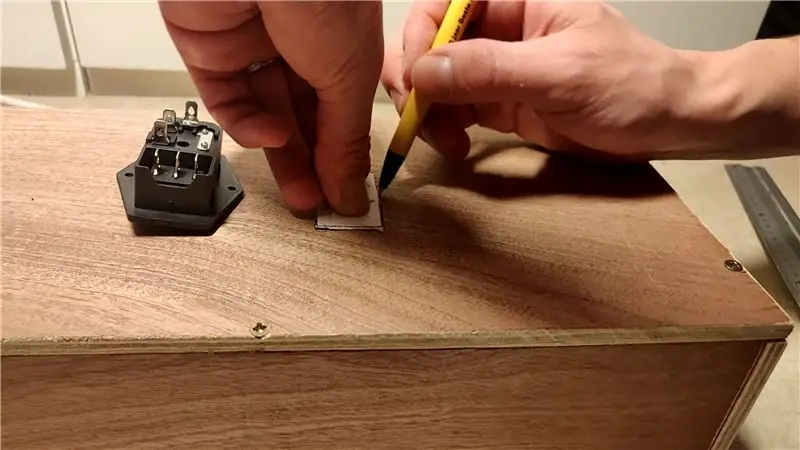
Met alle laagspanningscomponenten op hun plaats is het tijd voor het serieuze werk en het installeren van het hoofdspanningscircuit.
Het spreekt voor zich dat u tijdens het werken met de snoeren deze in geen geval op het lichtnet aansluit !!!!!
Samen met de technicus die de showlichten zou installeren en bedienen voor ons aanstaande concert, hebben we besloten om een gezekerd stopcontact te gebruiken als stroomingang voor de applausmeter. Dit zorgde ervoor dat elke kabel van elke lengte in onze meter kon passen en van stroom kon voorzien.
Dit zou ook een veiligheidslaag aan onze opstelling toevoegen: deze connectoren zijn uitgerust met een zekering die boven een bepaalde stroomsterkte doorbrandt, zodat er niets in de cache kan schieten als dat niet de bedoeling is.
Voor het installeren van deze plug hadden we de exacte afmetingen nodig. Het heeft echter een vrij complexe vorm. Dus het eenvoudigste wat ik kon bedenken, is om de stekker op een stuk karton te drukken en de contouren van de stekker te volgen. De contourlijnen kunnen vervolgens worden uitgesneden, waardoor een sjabloon ontstaat die op het hout kan worden overgebracht.
Houd er bij het markeren en uitknippen van de locatie voor de stekker rekening mee dat er al componenten aan de binnenkant van de meter zijn geïnstalleerd die niet meer kunnen worden verplaatst, waardoor de mogelijke locaties waar de stekker uit de doos kan steken, worden beperkt. Hetzelfde geldt voor het uitgangsgat van de 20m lange draad voor de 'afstandsbediening'.
Normaal zaag je het gat met een decoupeerzaag, maar ik heb niet zo'n apparaat en ik was ongeduldig, dus ik boorde gewoon gaten langs de contouren en zaagde het gat gewoon uit met een scherp mes. Dit werkt, maar ik kan het niet aanbevelen omdat ik bijna mijn vingers eraf sneed.
Nu is het alleen nog een kwestie van alles op elkaar aansluiten. Ik heb een bedradingsschema van het 220v-circuit gemaakt voor gemakkelijke referentie. De hete draad is parallel aangesloten op alle lampen, terwijl de nuldraad wordt onderbroken door de relais voordat deze op de lampen wordt aangesloten. Zo simpel is het. Zorg ervoor dat u het juiste licht op het juiste relais aansluit, anders moet u het 5V-besturingseinde of de 220v-draden opnieuw aansluiten om uw fout te herstellen.
Er is een Instructable over hoe je je draden op het gezekerde stopcontact kunt aansluiten die alles beter uitlegt dan ik ooit zou kunnen, dus spring daarheen, maar vergeet niet om hier terug te springen (https://www.instructables.com/id/Wire- Up-a-Fused-AC-Male-Power-Socket/)
[OPMERKING] Om de neutrale draden aan te sluiten op de centraal geplaatste relais, heb ik een draad aangesloten op de gezekerde aansluiting en deze in tien gedeeld voordat ik deze op de relais heb aangesloten. Ik was van plan om door de neutrale kabels bij de relais te gaan en elke relaisingang parallel aan elkaar te verbinden. De relaisterminals accepteerden echter niet meer dan één kabel, waardoor ik met een andere oplossing moest komen. Om deze splitsing te maken, is het raadzaam om een soort connector te gebruiken. Ik had dat niet (en ik was ongeduldig) en knoopte gewoon alle kabels samen in één grote knoop voordat ik het er als een blok voor zette. Ik raad deze 'knoop' niet aan vanwege elektrische veiligheidsredenen. VOORAL vanwege de nabijheid van het Arduino-bord. Het lijkt echter gewoon goed te werken.
Stap 7: Magnetische snappers (optioneel)
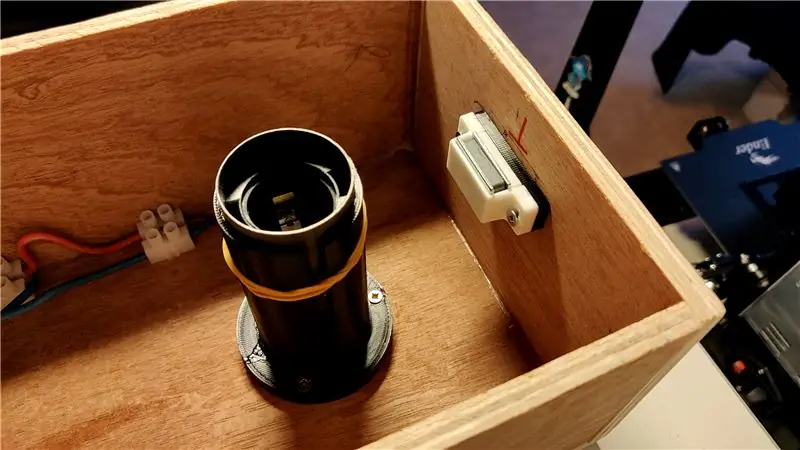
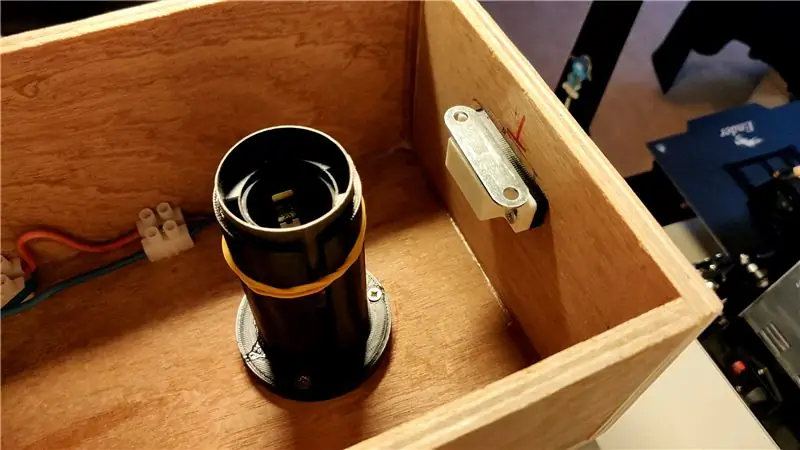
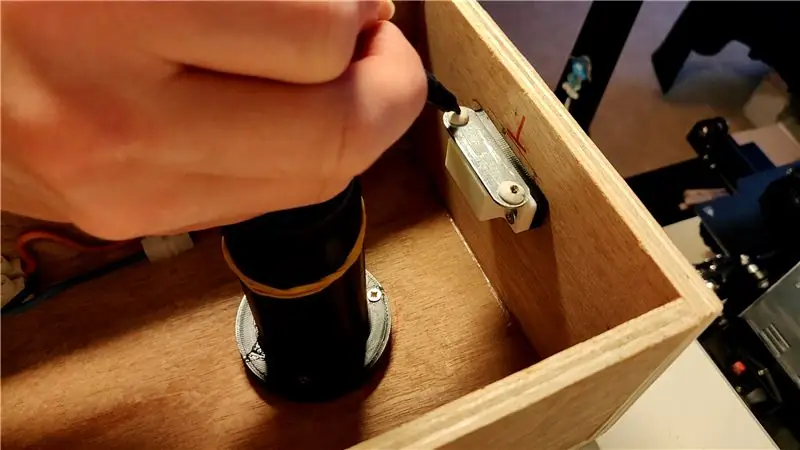
Deze stap is volledig optioneel, omdat de voorpaneelgeleiders de voorplaat voldoende vasthouden door alleen wrijving. Ik besloot om de snappers alleen als een veiligheidsvoorziening op te nemen, zodat het voorpaneel niet los zou komen zonder dat ik het los wilde laten
Ik lag vele nachten wakker en bedacht wat de beste methode zou zijn om het voorpaneel van de doos te houden waar het thuishoorde. Uiteindelijk kwam ik op het gebruik van magnetische deurdrangers. Ik betwijfel of dit de officiële term is voor deze handige apparaten, maar je herkent ze meteen. De magnetische snappers worden meestal gebruikt om kastdeuren gesloten te houden zonder een slot te gebruiken.
Ik heb het magnetische deel aan de buitenschaal van de applausmeter bevestigd (boven-, onder-, linker- of rechterpaneel). Dit gebeurde door middel van op maat gemaakte 3D-geprinte spacer en schroeven (yadda yadda yadda, lange schroeven, dun hout, je kent het verhaal inmiddels)
De metalen platen werden op het hout van de geleiders geschroefd. Dit was ook de eerste keer dat het hout echt dik genoeg was om geen spaties te gebruiken (yay). Ik had echter wat problemen met het bepalen van de positie van de metalen platen. Ik heb een oplossing bedacht:
- Bevestig het magnetische deel aan de doos
- plaats de metalen plaat op de magneet in de perfecte positie
- plaats een bolletje "Pritt-buddy" op de gaten in de plaat (een soort kauwgom-achtige lijm om posters aan de muur te bevestigen zonder punaises, gewone kauwgom zou waarschijnlijk ook werken)
- maak met een alcoholstift een stip op de Pritt-buddybal op de plaats waar de gaatjes zitten
- sluit het deksel, waardoor een deel van de markeringsinkt op het hout wordt overgebracht
- Til het deksel op en tadaa! Je hebt een kleine markering gemaakt waar je schroeven moeten komen
- verwijder de buddies en de plaat en schroef deze in de juiste positie, probeer eerst
- stap 8: winst
Ik plaatste vier magnetische snappers in de doos: één onderaan, één bovenaan, één links in het midden, één rechts in het midden.
De snappers die ik koos hadden een houdkracht van 6 kg. Met vier daarvan leverden ze genoeg kracht om de hele doos bijna alleen aan het voorpaneel op te tillen.
Stap 8: Wat ik anders zou doen?
Tijdens het maken van deze applausmeter heb ik vaak mijn verleden vervloekt voor het nemen van domme beslissingen, ik zal hier de belangrijkste lessen opsommen die ik heb geleerd:
-
GEBRUIK DIKKER TRIPLEX. Serieus, een doos maken van 8 mm multiplex is mogelijk, maar het brengt veel uitdagingen met zich mee en dwingt tot het sluiten van een aantal compromissen.
- Ten eerste is het voorboren van alle gaten voor de schroeven een uitdaging, omdat er geen tolerantie is voor boren met een verkeerde hoek.
- Ten tweede waren de schroeven die ik had 16 mm (heb ik dit al eerder genoemd?). Dit dwong me om enkele afstanden te maken bij het in het hout schroeven om te voorkomen dat de schroeven aan de andere kant naar buiten steken, maar tegelijkertijd betekende dit dat de schroeven niet diep genoeg penetreerden om voldoende tractie te krijgen om sommige componenten vast te houden.
- ….
- gebruik gewoon dikker hout