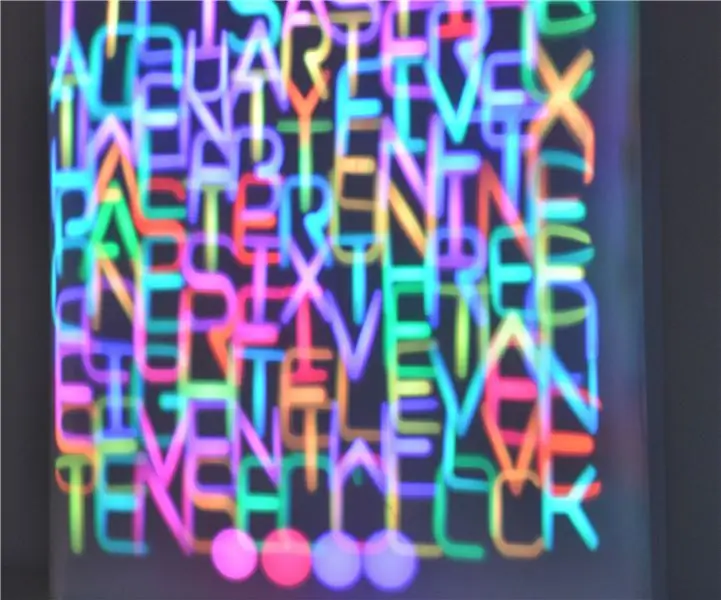
Inhoudsopgave:
- Stap 1: Ontwerp
- Stap 2: Materialen verzamelen
- Stap 3: 3D-geprinte componenten
- Stap 4: Het frame construeren
- Stap 5: De brievenbussen in elkaar zetten
- Stap 6: Montage van de aandrijvingen
- Stap 7: De achterplaat maken
- Stap 8: Bevestig componenten aan achterplaat en bedrading
- Stap 9: Achterplaat aan frame bevestigen
- Stap 10: De servo's kalibreren
- Stap 11: De code uploaden
- Stap 12: Het scherm bevestigen
- Stap 13: De boven- en onderafdekking bevestigen
- Stap 14: Voltooide klok en samenvatting
2025 Auteur: John Day | [email protected]. Laatst gewijzigd: 2025-01-23 15:01
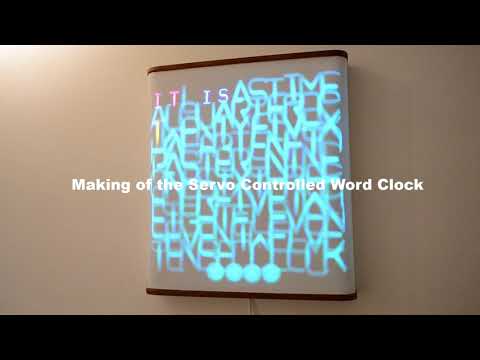
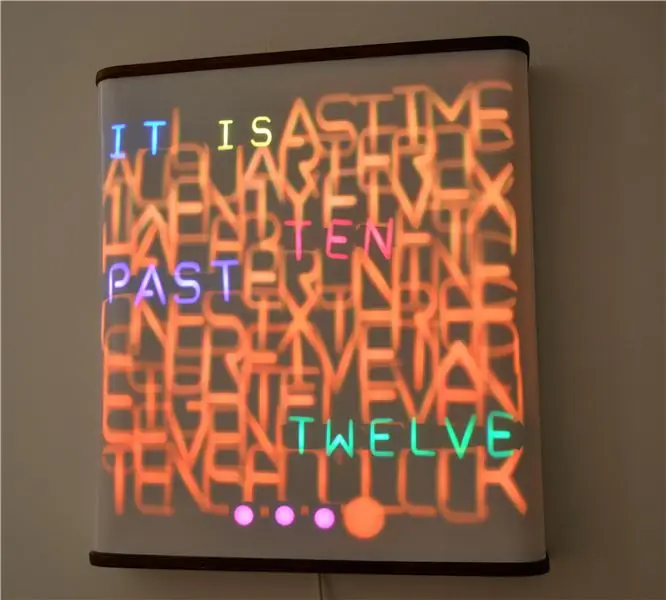
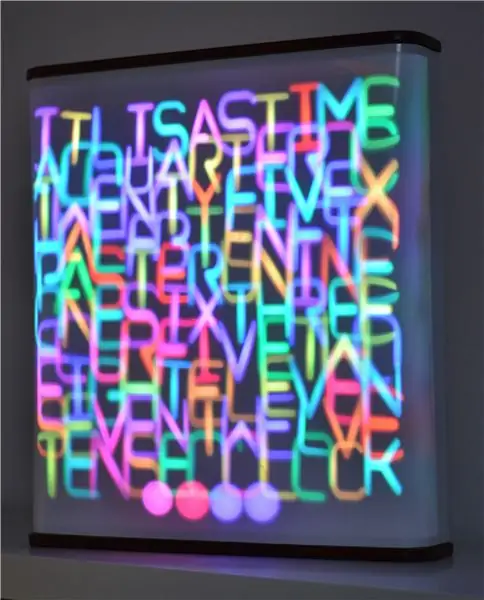
Fusion 360-projecten »
Wat heeft 114 LED's en is altijd aan? Zoals u wellicht weet, is het antwoord een woordklok. Wat heeft 114 LED's + 114 servo's en is altijd in beweging? Het antwoord is deze servogestuurde wordclock.
Voor dit project werkte ik samen met een vriend van mij, wat een must bleek te zijn vanwege de grote inspanning van deze build. Bovendien vulden mijn elektronische en zijn mechanische vaardigheden elkaar goed aan. Het idee voor deze aanpassing van de populaire woordklok kwam bij ons terwijl we een gewone klok aan het maken waren als kerstcadeau. Daar merkten we dat het ook mogelijk is om de letters van achteren op een wit vel papier te projecteren. Destijds was dit slechts een tijdelijke oplossing om ons waardeloze vakmanschap te verbergen, aangezien we een heleboel bubbels kregen terwijl we een vinylsticker met de letters op de achterkant van een glasplaat plakten. We merkten toen dat je interessante effecten kunt bereiken bij het buigen van het vel papier, omdat de letters van grootte veranderen en wazig worden. Dit bracht ons op het idee om een wordclock te maken waarbij de letters van achteren op een scherm worden geprojecteerd en heen en weer kunnen worden bewogen om de grootte van het geprojecteerde beeld te veranderen. In het begin waren we een beetje terughoudend om dit project te bouwen vanwege de kosten en moeite die het kost als je elk van de 114 letters afzonderlijk wilt verplaatsen. Dus kwamen we op het idee om een versie te maken waarin elk woord dat wordt gebruikt om de tijd weer te geven heen en weer kan worden verplaatst. Toen we echter zagen dat de Epilog-wedstrijd op Instructables kwam en om epische projecten vroeg, en ook nadat we relatief goedkope servomotoren hadden gevonden, besloten we er alles aan te doen en een goede versie te maken waarbij elke letter afzonderlijk wordt bestuurd door een servo.
LET OP: Dit is geen eendaagse build!
Om u een idee te geven van de inspanningen die in dit project zijn gemoeid, kunt u de volgende cijfers bekijken. De voltooide klok bevat:
- 798 individuele 3D-geprinte modellen (totale printtijd ~ 200 uur)
- ~600 schroeven + ~250 moeren en ringen
- ~500 draden (totale lengte ~ 50 m). Nog afgezien van de draden die al aan de servo's waren bevestigd.
Stap 1: Ontwerp
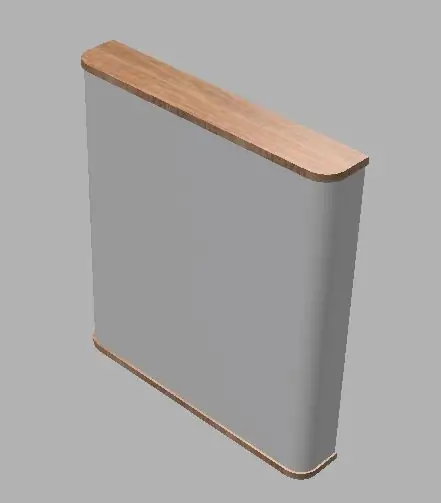
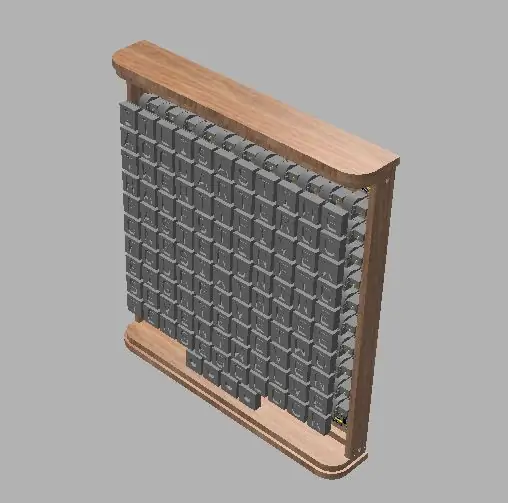
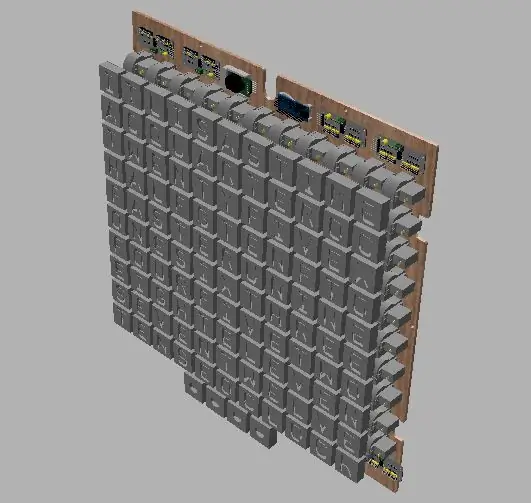
De klok is ontworpen met Autodesk Fusion 360 en Inventor. Zoals je kunt zien bestaat de klok uit 114 brievenbussen die worden bewogen door lineaire actuatoren die op hun beurt worden aangedreven door servomotoren. Elke brievenbus bevat een LED die de letter op de achterkant van een scherm van witte PVC-folie projecteert. Alle componenten zijn ondergebracht in een houten frame.
Stap 2: Materialen verzamelen
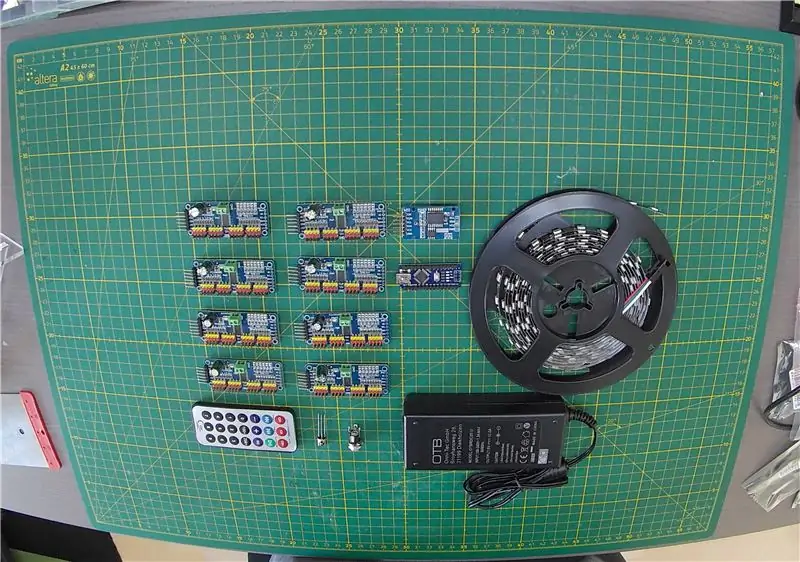
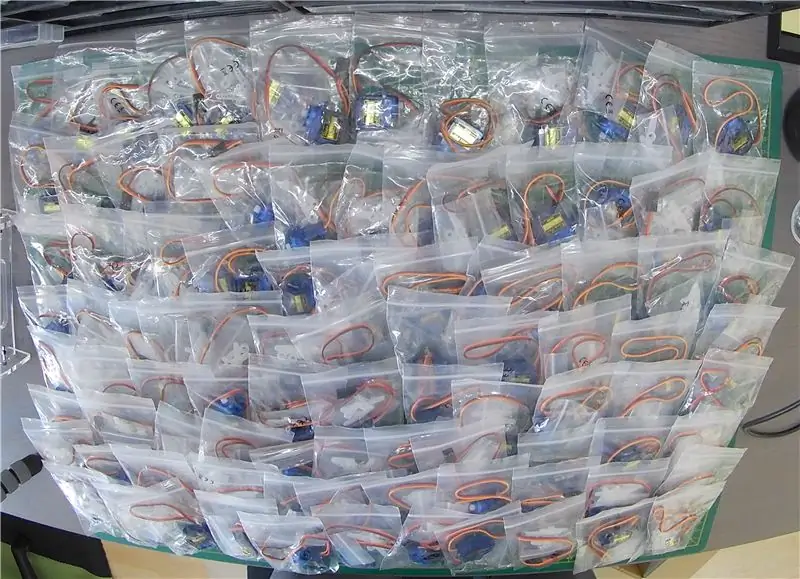
Elektronische componenten
114x SG90 micro-servomotoren (ebay.de)
Hoewel de servo's waren gelabeld met de naam van het populaire merk "Tower Pro", zijn het zeker goedkopere namaakproducten. Omdat de prijs van de knock-off echter ongeveer 1 EUR is in vergelijking met 3 EUR voor het origineel, maakt dit het hele project veel betaalbaarder. Blijkbaar trekken de knockoffs ook minder stroom (dit betekent natuurlijk ook minder koppel) waardoor het makkelijker werd om een geschikte voeding voor het hele project te vinden.
- 5 m WS2812B ledstrip, 60 leds/m (ebay.de)
- 8x 16 Ch PWM servo driver PCA9685 (ebay.de)
- DS3231 RTC-module (ebay.de)
- Arduino nano (ebay.de)
- VS1838B IR-ontvanger + afstandsbediening (ebay.de)
- 5 V, 10 A voeding (ebay.de)
- 20x 15 cm servo verlengkabel (ebay.de)
- kabel DC-bus naar blanke draad (conrad.de)
- 300-500 Ohm weerstand
- 1000 µF condensator (> 5 V)
Materialen voor frame
-
houten latten
- 2 stuks 40 x 10 x 497 mm
- 2 stuks 12 x 12 x 461 mm
- 2 stuks 12 x 12 x 20 mm
-
multiplex
- 2 stuks 12 x 77 x 481 mm
- 2 stuks 12 x 84 x 489 mm
- witte PVC-folie (700 x 1000 x 0,3 mm) (modulor.de)
- 500 x 500 mm HDF-plaat, 3 mm dik
Schroeven, kabels, enz
- 228x M2 schroeven, 8 mm lang + ringen + zeskantmoeren
- 228x zelftappende schroeven M2.2, 6,5 mm lang
- verschillende houtschroeven
- 50 m, 0,22 mm2 (24 AWG) draad
Bovendien vergde dit project veel 3D-printen en solderen. De achterplaat is gemaakt door middel van lasersnijden. Het frame werd gebouwd met een cirkelzaag, decoupeerzaag en boor. Zoals voor elk fatsoenlijk project hebben we ook veel hete lijm gebruikt, ook wat epoxy- en plasticlijm.
De totale kosten voor dit project bedroegen ongeveer 350 EUR.
Stap 3: 3D-geprinte componenten
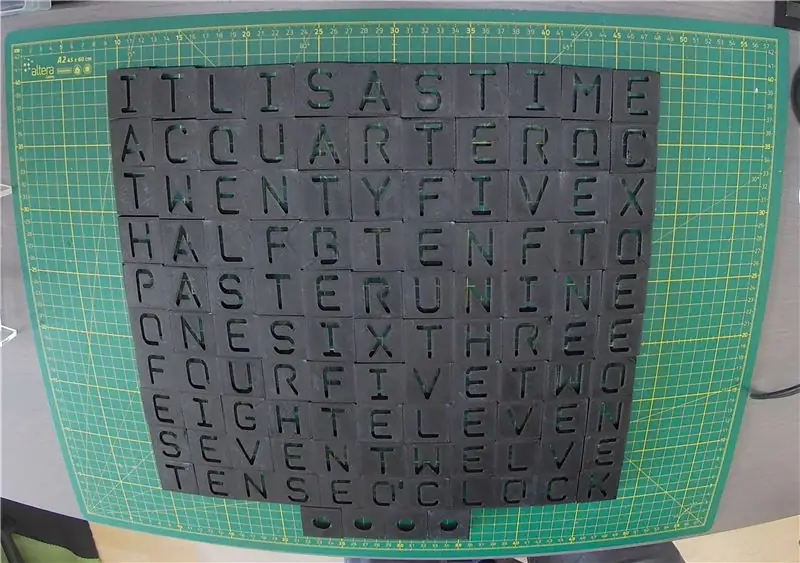
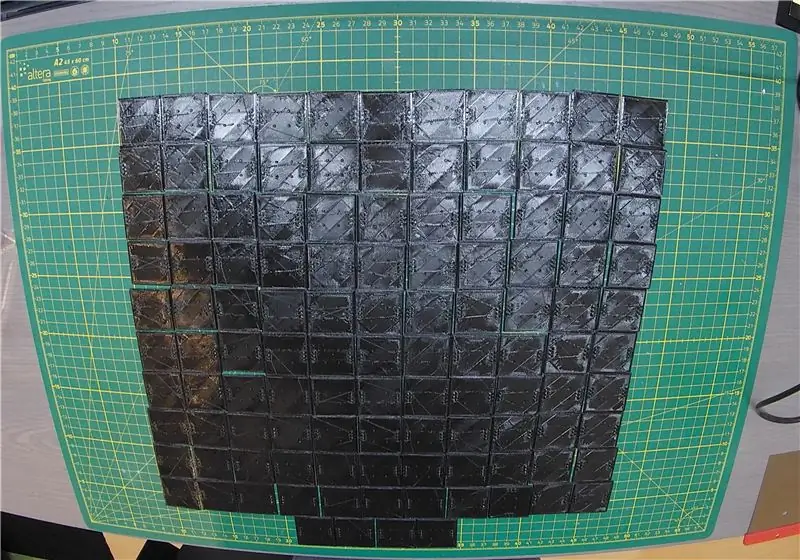
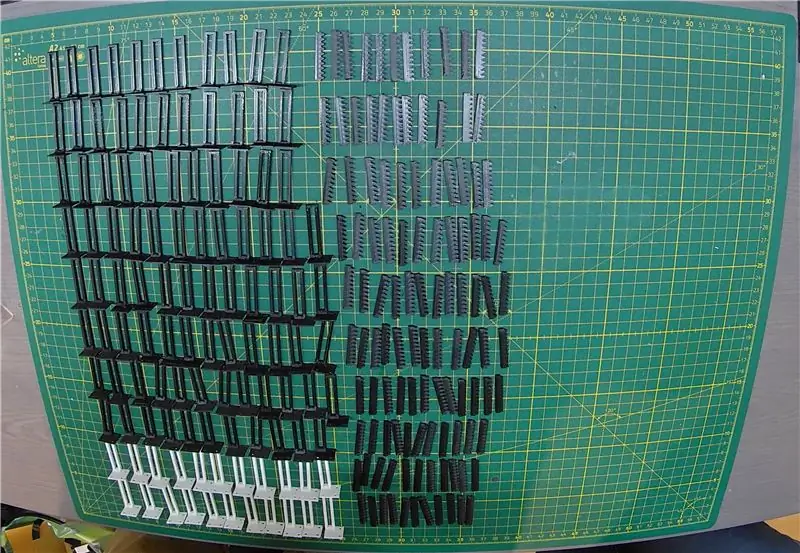
Brievenbussen
Elke brievenbus bestaat uit een 3D-geprint deksel dat als schaduwmasker fungeert en een basisplaat waarop een LED wordt bevestigd. De basisplaat bevat vier paspennen om de uitlijning op de actuator te vergemakkelijken en zes gaten voor het doorvoeren van de LED-kabels. In totaal zijn dit 228 modellen die allemaal zijn geprint van zwart PLA (Formfutura EasyFill PLA) met een laaghoogte van 0,4 mm. De totale afdruktijd op mijn Anycubic Kossel Linear Plus was ongeveer 23 uur voor de briefomslagen en 10 uur voor de basisplaten. Alle stl-bestanden zijn te vinden in het bijgevoegde zip-bestand.
Actuatoren
Het ontwerp van de actuator is aangepast van de Linear Servo Extender door Roger Rabbit, wat erg nuttig was. Omdat de onderdelen strak op elkaar passen, moeten ze op een degelijke 3D-printer worden afgedrukt. Een kleine laaghoogte is niet zo belangrijk (0,2 mm is prima) als een kleine spuitmonddiameter (wij raden 0,4 mm aan). De onderdelen moeten in de getoonde richting worden afgedrukt. Elke actuator bestaat uit 5 afzonderlijke onderdelen, aangezien we 114 actuatoren nodig hadden, betekent dit in totaal 570 onderdelen (!) Om deze te printen gebruikten we de gecombineerde kracht van verschillende professionele 3D-printers (Ultimaker S2+, Ultimaker S5, Lulzbot TAZ6, Sindoh 3D Wox DP200). Toch hadden we veel mislukte afdrukken op de onderdelen en ik heb wat foto's toegevoegd voor uw vermaak. De totale printtijd was ongeveer 150 uur (!). Nogmaals, de stl-bestanden zijn te vinden in het bijgevoegde zip-bestand.
Stap 4: Het frame construeren
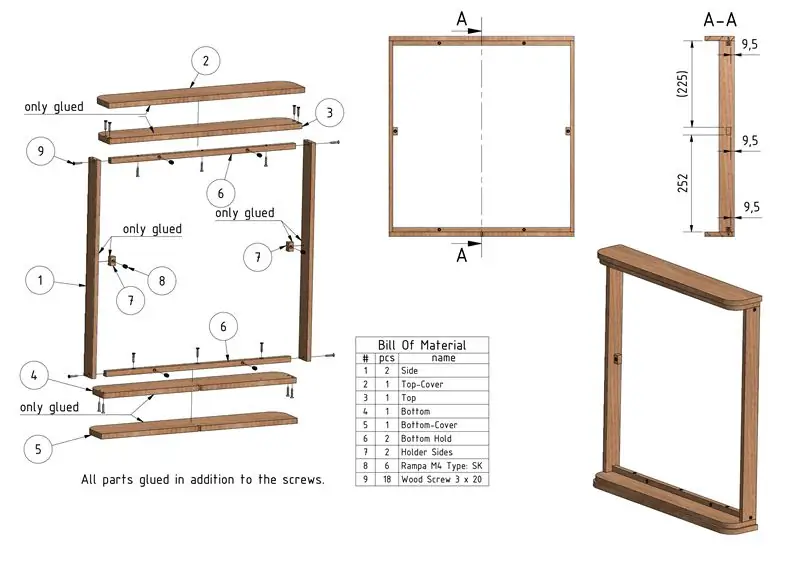
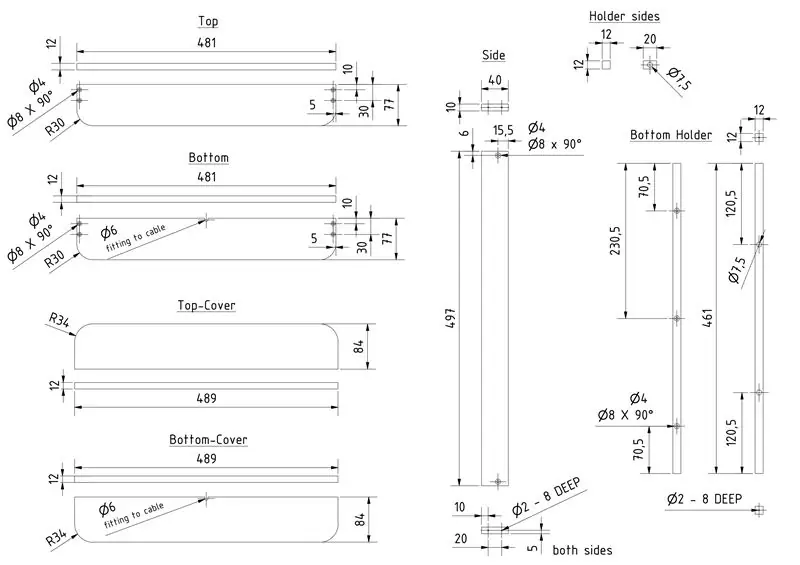

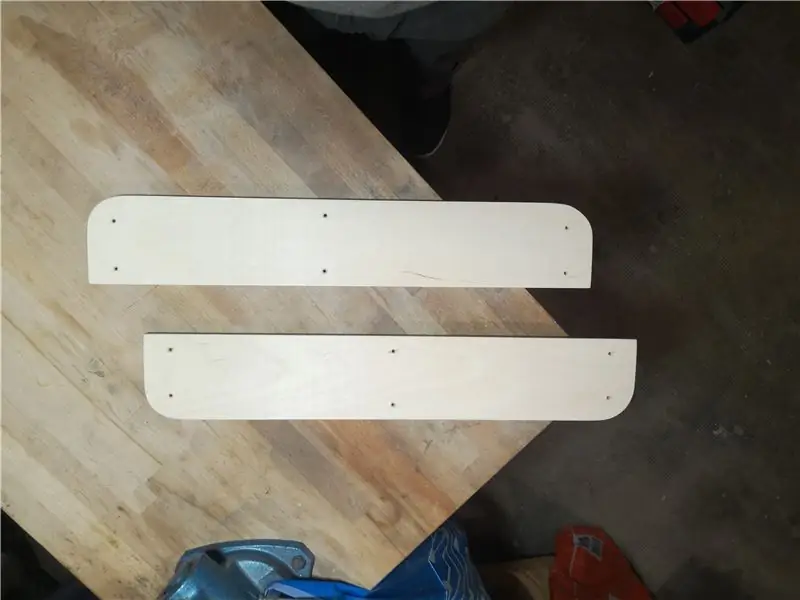
Het frame is gemaakt van houten latten en multiplex. De onderdelen zijn uitgesneden met een cirkelzaag en een decoupeerzaag en vervolgens aan elkaar bevestigd met houtlijm en houtschroeven. De boven- en onderkaft zijn ook gebeitst om het een mooiere uitstraling te geven. Een gedetailleerde beschrijving van de onderdelen inclusief alle afmetingen vindt u in de bijgevoegde tekeningen.
Stap 5: De brievenbussen in elkaar zetten
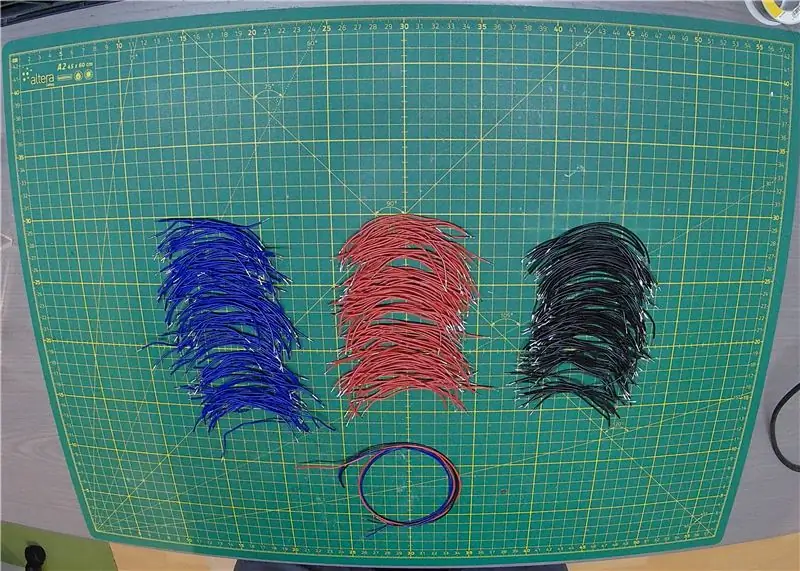
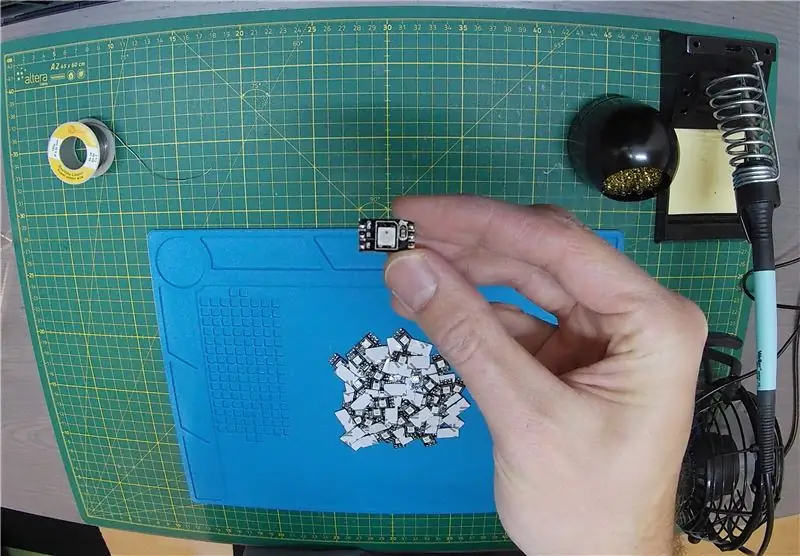
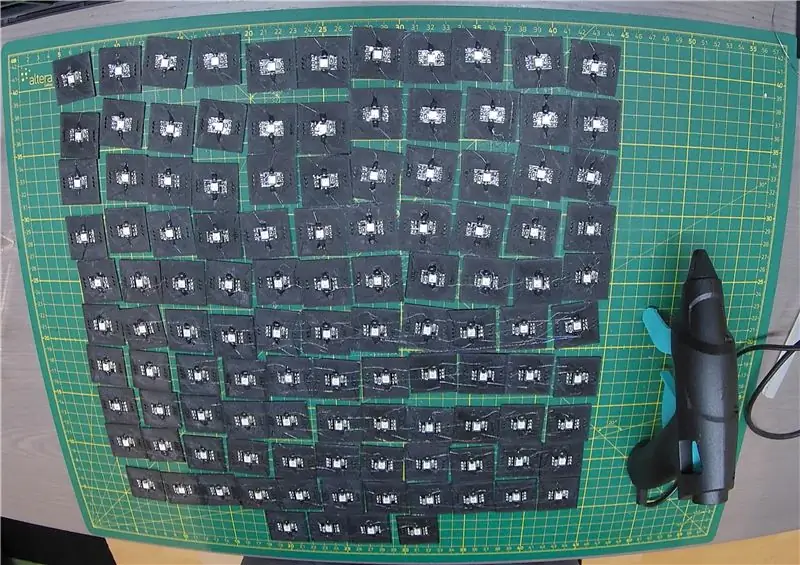
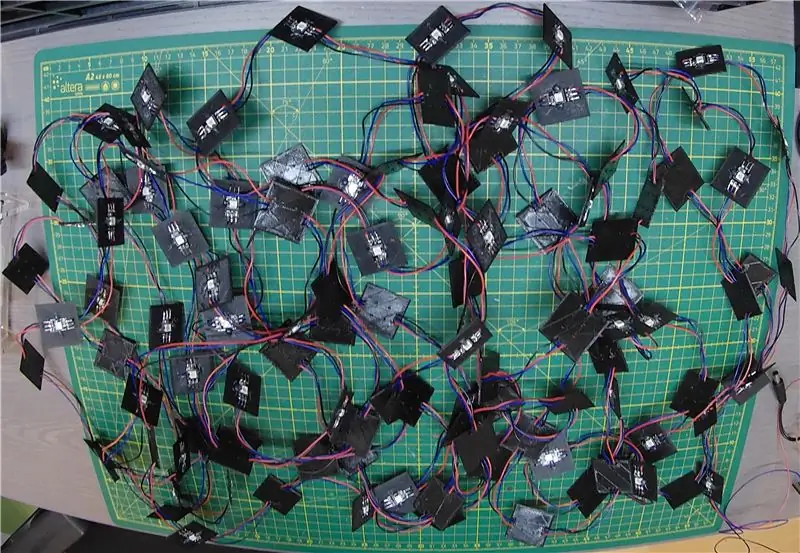
Het in elkaar zetten van de brievenbussen was veel werk en duurde erg lang, vooral het solderen. Dit komt omdat elke stap die je maakt 114 keer herhaald moet worden.
- Knip 114 losse stukjes uit de ledstrip
- Tin alle LED-pads
- Bevestig elke LED aan de 3D-geprinte achterplaat van een brievenbus. De LED moet gecentreerd zijn. We hebben het ook vastgezet met hete lijm.
- Vervolgens hebben we 3x114 = 442 draden voorbereid, d.w.z. op lengte knippen, de uiteinden strippen en vertinnen. De lengte van elke draad was elk 10 cm, behalve de draden die de laatste letter met de stippen verbinden, die langer moeten zijn (~ 25 cm). Ook moeten de draden die zijn aangesloten op de eerste letter die op de arduino en de voeding wordt aangesloten, langer zijn.
- Diasy ketting LED's met behulp van draden. De draden worden door de gaten in de 3D-geprinte achterplaat van elke brievenbus geleid.
- De voorkant van de brievenbus was vastgemaakt met lijm
- Delen van het lineaire rek voor de actuator moeten aan elkaar worden gelijmd
- Lineair rek wordt met lijm aan de achterkant van de brievenbus bevestigd
Stap 6: Montage van de aandrijvingen
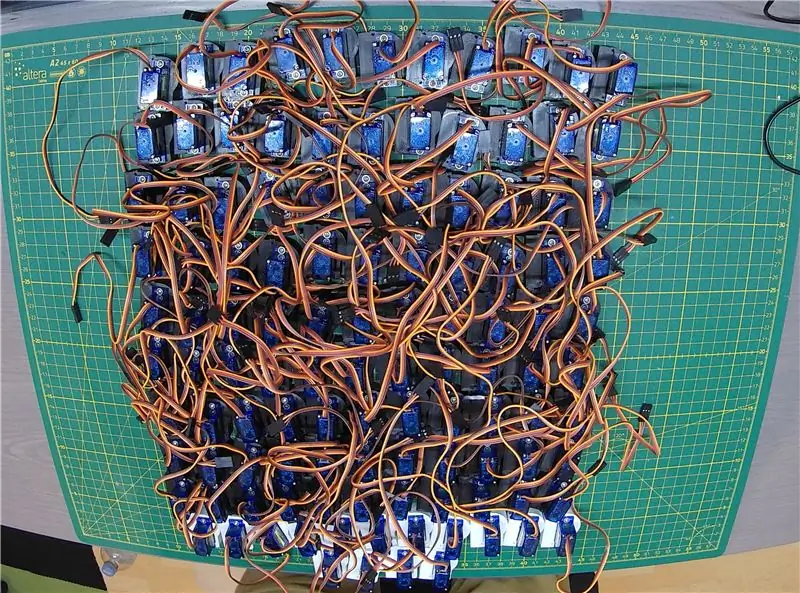
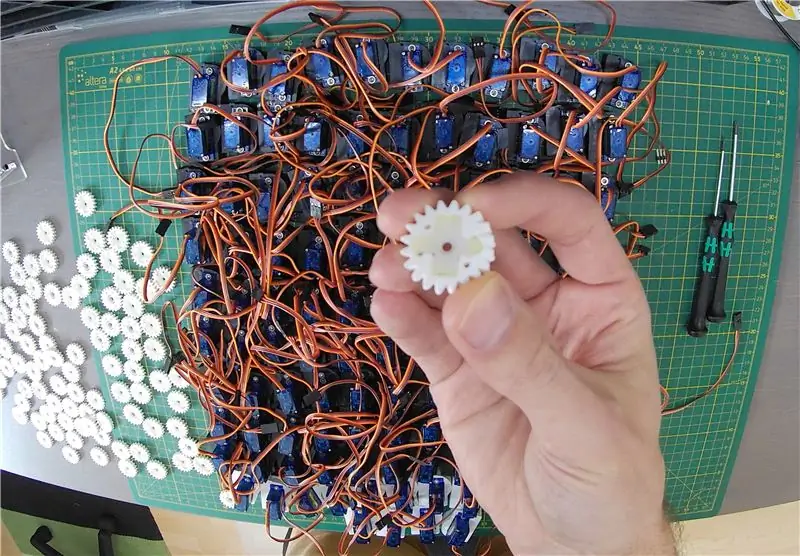
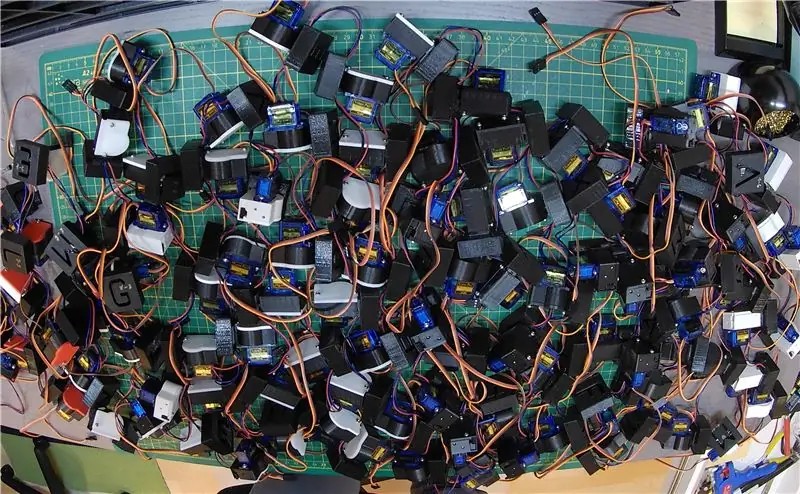
Het opnieuw monteren van de actuatoren was een zeer vervelende procedure die veel tijd in beslag nam.
- Bevestig de servo aan de 3D-geprinte behuizing met behulp van de meegeleverde schroeven
- Het ronde tandwiel wordt aan de servo bevestigd met behulp van het meegeleverde plastic kruis, maar eerst moet het kruis in vorm worden gesneden en met epoxy aan het tandwiel worden bevestigd.
- Bevestig de versnelling aan de servo met behulp van de meegeleverde schroef
- Voordat het lineaire rek werd geplaatst, werd elke servo op dezelfde positie gezet
- Het lineaire rek met de brievenbus plaatsen
- Twee M2-zeskantmoeren in de 3D-geprinte behuizing plaatsen die later zullen worden gebruikt om deze op de achterplaat te bevestigen
- Sluit de behuizing met 3D-geprint deksel met behulp van de M2.2 zelftappende schroeven
Uiteindelijk eindigden we met een grote puinhoop van diasy-geketende actuatoren zoals weergegeven in de afbeelding hierboven
Stap 7: De achterplaat maken
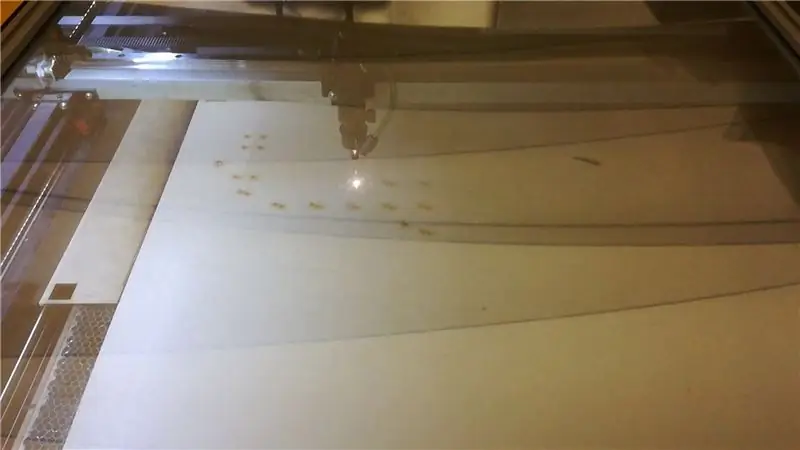
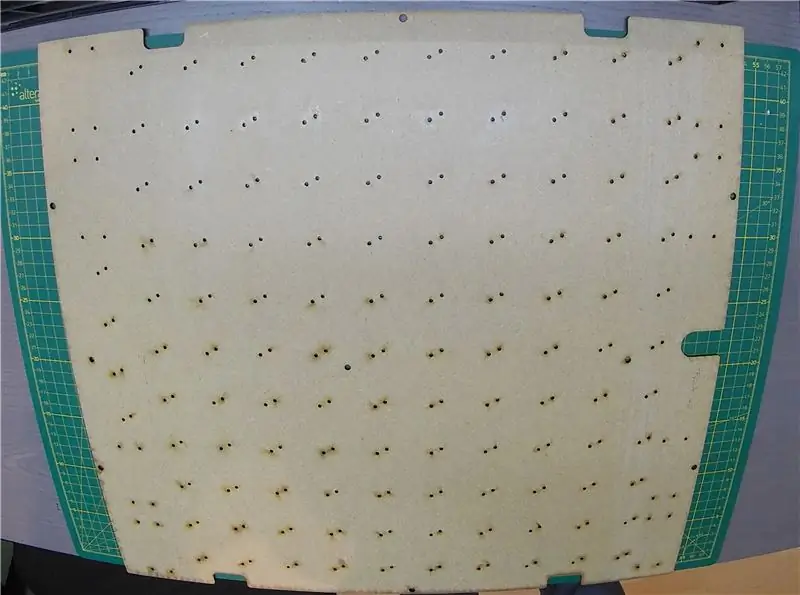
De achterplaat werd met een laser uit 3 mm dik HDF-hout gesneden met behulp van een CO2-lasersnijder van onze lokale makerruimte. Eerst probeerden we multiplex, maar het bleek veel te dun om het gewicht van alle componenten te dragen. Het zou in dit geval nog beter zijn geweest om aluminium te gebruiken, maar dat is natuurlijk duurder en niet te snijden met een CO2-laser. Het dxf-bestand voor de achterplaat is bijgevoegd.
Stap 8: Bevestig componenten aan achterplaat en bedrading
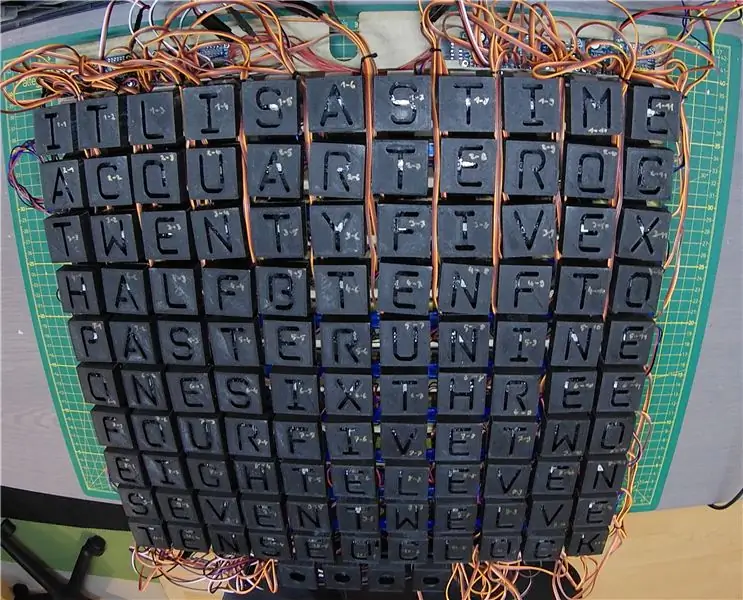
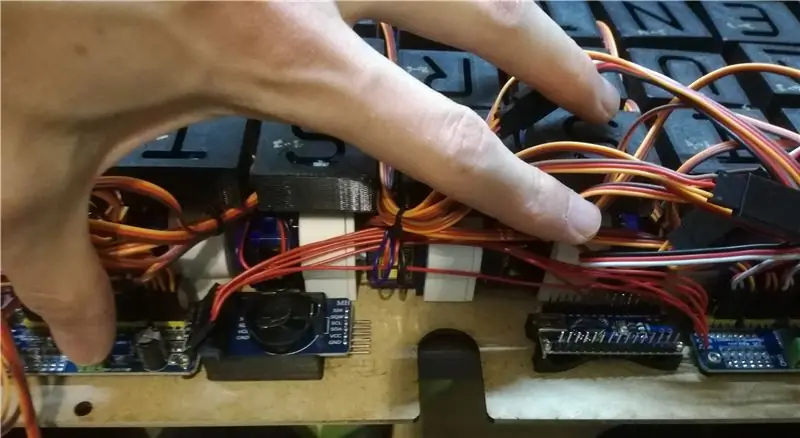
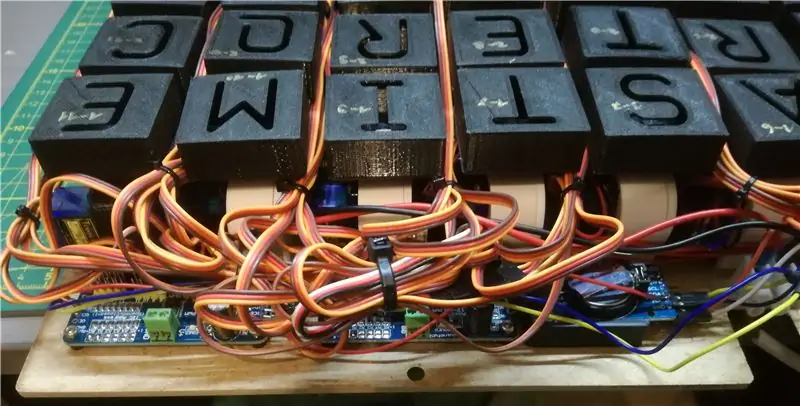
Eerst moeten de PCA9685-kaarten op de achterplaat worden bevestigd met behulp van PCB-afstandhouders. Vervolgens kunnen de Arduino nano en RTC module worden geplaatst zoals op de afbeelding hierboven. Voor de laatste twee hebben we 3D-geprinte houders gebruikt die met hete lijm waren vastgemaakt. Componenten zijn aangesloten zoals aangegeven in het bedradingsschema. Merk op dat het het beste is om elke PCA9685 afzonderlijk van stroom te voorzien via het klemmenblok. In eerste instantie hebben we ook de V+- en GND-connectoren in serie geschakeld en alleen het aansluitblok van het eerste bord aangesloten (zoals gesuggereerd op de adafruit-pagina), maar in dit geval gaat alle stroom door het eerste bord en hebben we uiteindelijk de MOSFET verbrand van het omgekeerde beveiligingscircuit. Er is ook een spreadsheet bijgevoegd met de bekabeling van de servo's. Verlengkabels voor de servo's werden waar nodig gebruikt. Merk op dat je verschillende I2C-adressen moet toewijzen aan elke PCA9685 zoals uitgelegd op de adafruit-pagina.
De actuatoren werden vervolgens met 228x M2-schroeven aan de achterplaat bevestigd. Het werk was weer erg eentonig maar nadat het klaar was begon de klok al vorm te krijgen. We hebben ook geprobeerd de servokabels zo goed mogelijk te ordenen, maar uiteindelijk was de bekabeling nog steeds erg rommelig.
Stroom werd geleverd door de DC-kabel door de achterplaat te voeren en deze aan te sluiten op een aansluitblok.
Stap 9: Achterplaat aan frame bevestigen
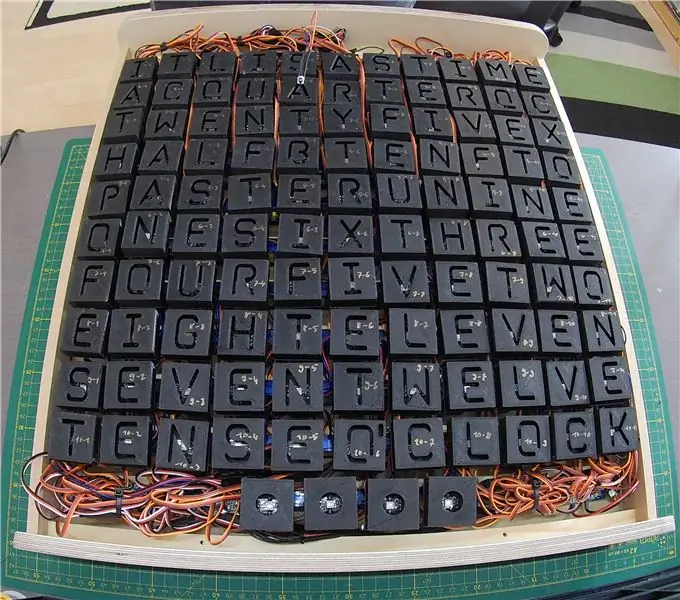
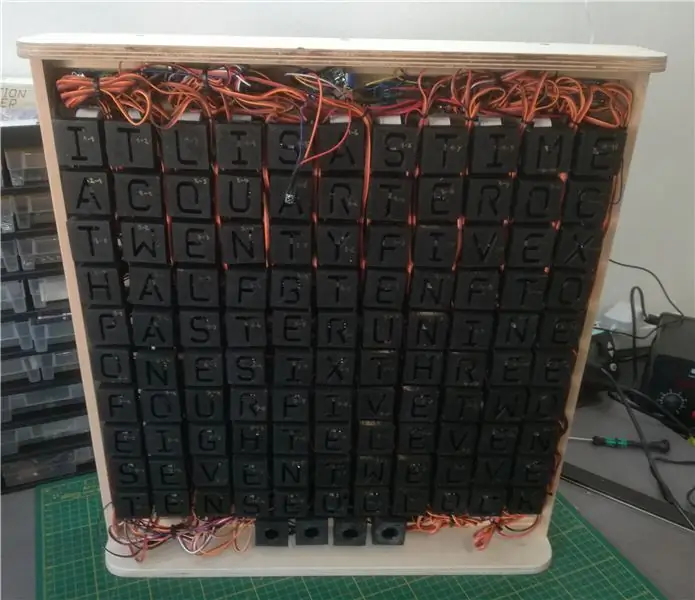
Nadat alle componenten waren gemonteerd en de kabels waren geordend, hebben we de achterplaat aan het frame bevestigd met 6x M4-schroeven. Helaas hebben we heel weinig ruimte overgelaten om alle kabels te laten passen, dus moesten ze een beetje worden samengedrukt.
Stap 10: De servo's kalibreren
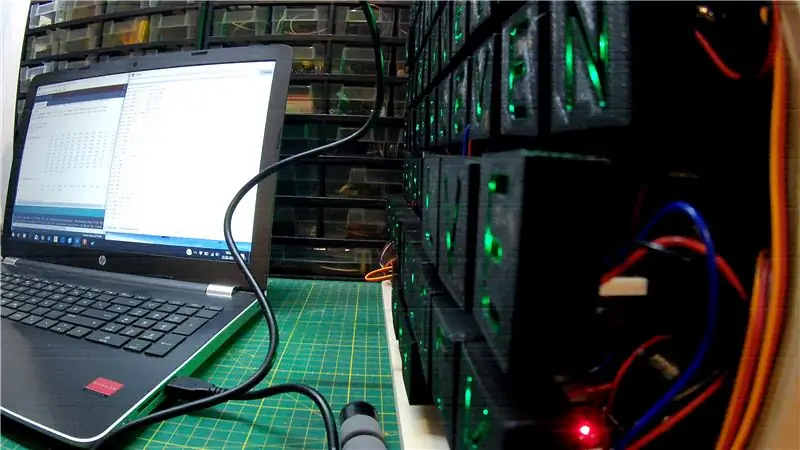
Omdat de hoogte van alle brievenbussen na montage iets anders was, hebben we de bijgevoegde code gebruikt om alle servo's te kalibreren zodat de brievenbussen dezelfde minimum- en maximumposities hebben. Voor de maximale positie hebben we geprobeerd de brievenbus zo dicht mogelijk bij het scherm te plaatsen. De gekalibreerde min/max-posities voor elke servo worden dan later in de hoofdcode ingevoerd.
Stap 11: De code uploaden
Bijgevoegd is de hoofdcode voor de woordklok. Er zijn drie soorten effecten voor het weergeven van de tijd.
- Verplaats snel alle letters naar achteren (de een na de ander) en licht LED's op met dezelfde willekeurige kleur. Verplaats vervolgens snel letters die de tijd weergeven een voor een naar voren en licht elk woord in een willekeurige kleur op.
- Verplaats snel alle letters naar achteren (de een na de ander) en licht LED's op met dezelfde willekeurige kleur. Verplaats langzaam elk woord dat de tijd weergeeft naar voren (alle letters tegelijk) en vervaag de kleur van de achtergrondkleur naar een willekeurige waarde.
- Verplaats snel alle letters naar een willekeurige positie (de een na de ander) en licht LED's op met verschillende willekeurige kleuren. Verplaats vervolgens langzaam alle letters naar achteren en vervaag de kleur. Ga verder met 1. of 2.
Ik wilde ook een effect implementeren waarbij de stip die de huidige minuut aangeeft, geleidelijk naar voren beweegt en de kleur vervaagt, zodat deze op de voorste positie staat met de juiste kleur wanneer de minuut is afgelopen. Helaas heb ik het nog niet werkend gekregen omdat het lijkt alsof de IR-ontvanger niet meer reageert.
Stap 12: Het scherm bevestigen
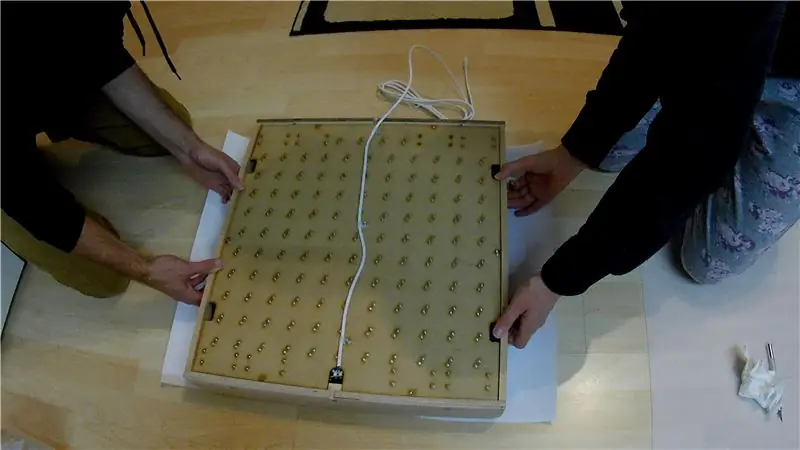
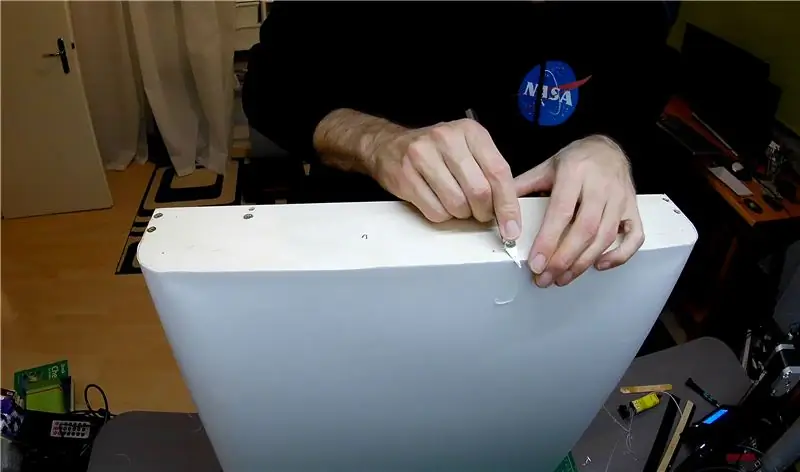
In eerste instantie wilden we witte stof als scherm gebruiken. Het probleem was dat na bevestiging aan het frame de stof in het midden naar beneden boog en we een speldenkussenvervorming kregen. We hebben toen besloten om in plaats daarvan een dunne witte PVC-folie voor het scherm te gebruiken. De folie wordt ook geadverteerd voor het maken van lampenkappen zodat het een redelijke transmissie heeft maar het is niet doorschijnend dus de zwarte brievenbussen blijven verborgen. In onze eerste proef hebben we de folie met epoxy bevestigd, maar deze plakte niet zo goed, dus zijn we overgestapt op hete lijm. Pas echter op dat als de lijm te heet is, deze de folie kan smelten. Overtollige folie werd verwijderd met een exacto mes.
Stap 13: De boven- en onderafdekking bevestigen
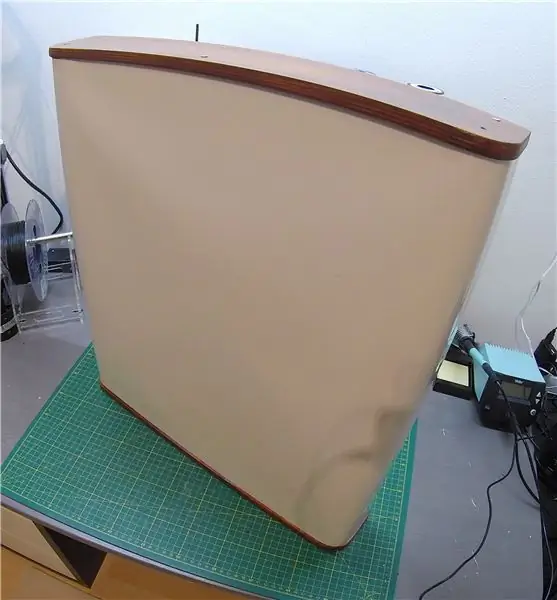
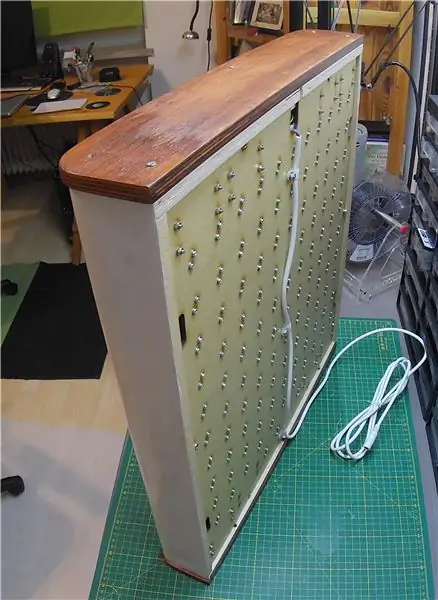
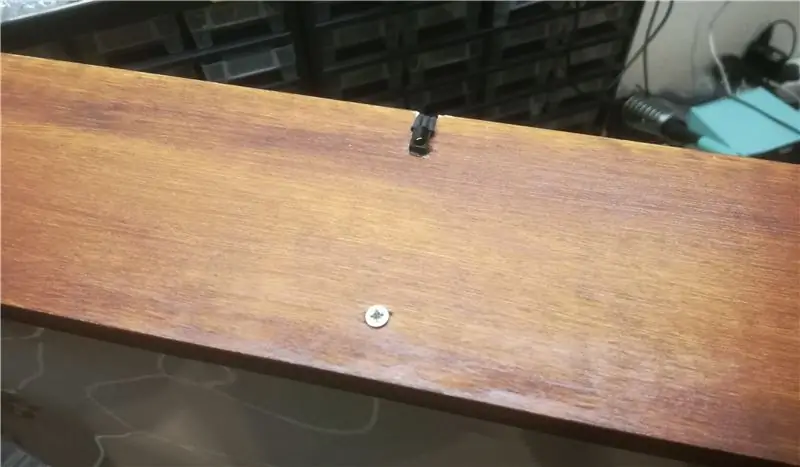
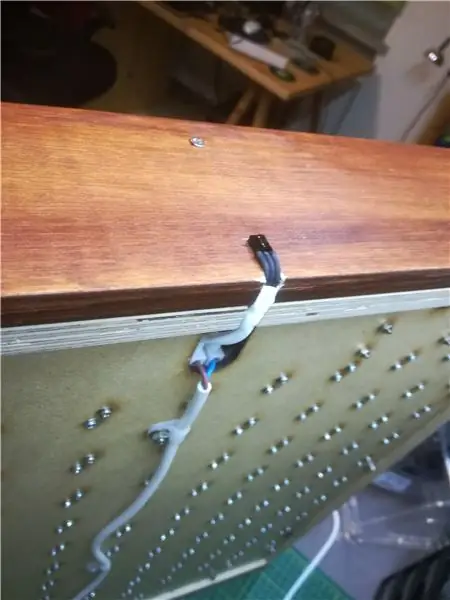
Ten slotte werden de gebeitste houten deksels aan de boven- en onderkant bevestigd. De donkere kleur vormt een mooi contrast met het witte scherm. De IR-ontvanger werd door het gat in de achterplaat gevoerd en met hete lijm aan de bovenklep bevestigd.
Stap 14: Voltooide klok en samenvatting
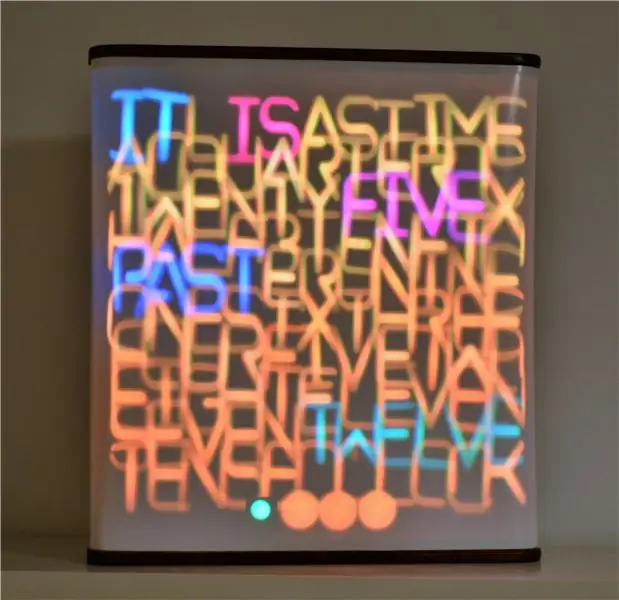
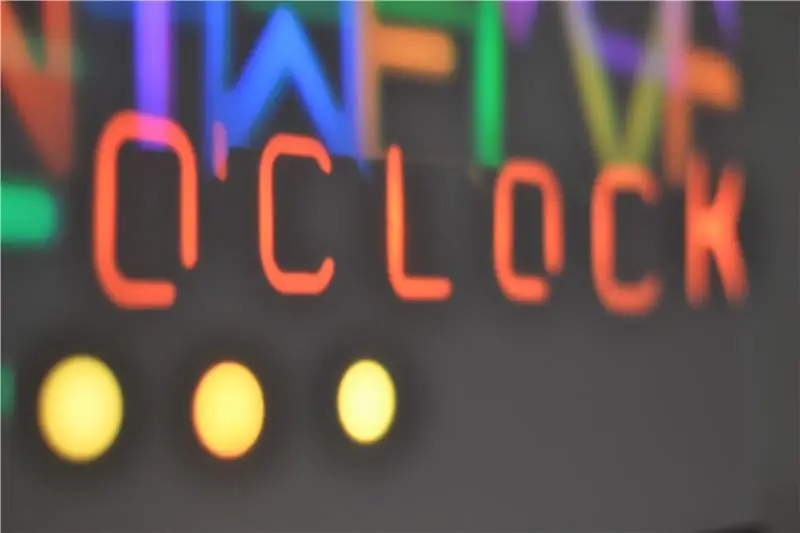
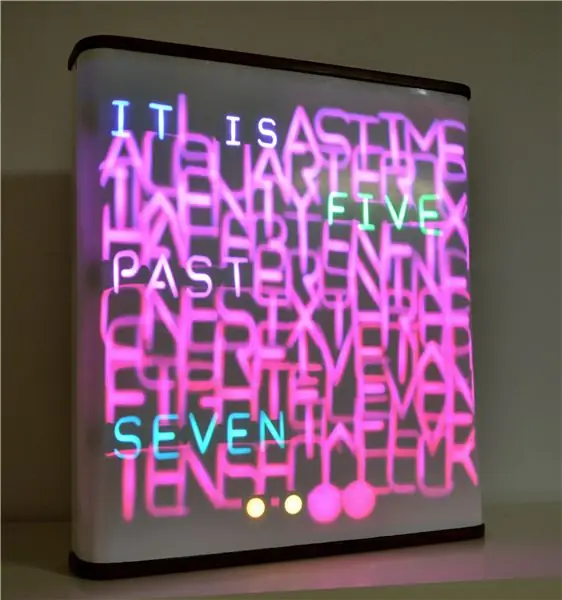
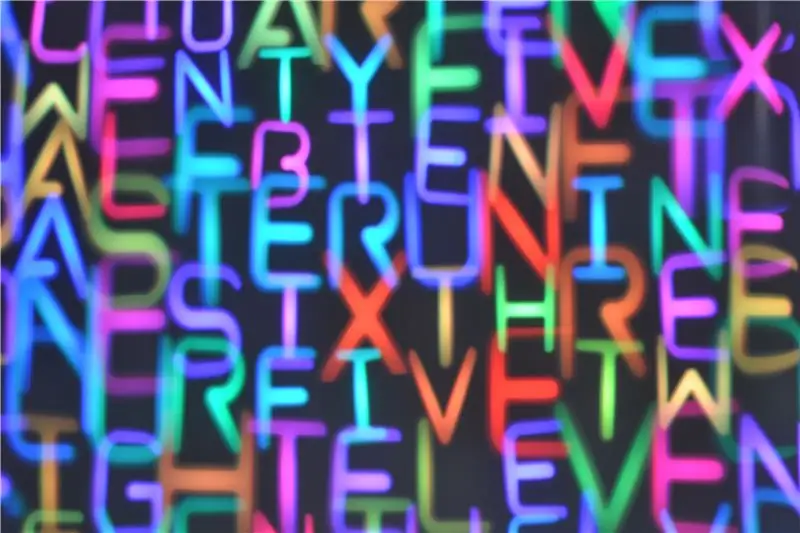
Na twee maanden intensief werken was de klok eindelijk af en werkend. Over het algemeen zijn we erg blij met het resultaat. Het verplaatsen van de letters achter het scherm in combinatie met het veranderen van de kleuren van de LED's levert zeer coole effecten op. Uiteindelijk kwamen de letters niet perfect overeen en was het scherm niet 100% vlak, maar dit maakt het bijna nog mooier. Er zijn zeker dingen die verbeterd kunnen worden, maar ik denk niet dat er een versie 2.0 zal komen vanwege de enorme inspanning van deze build, tenzij we de volgende keer de productie uitbesteden aan China.
Als je deze build leuk vindt en erin geslaagd bent om helemaal naar beneden te scrollen, stem dan op ons in de Epilog-wedstrijd.
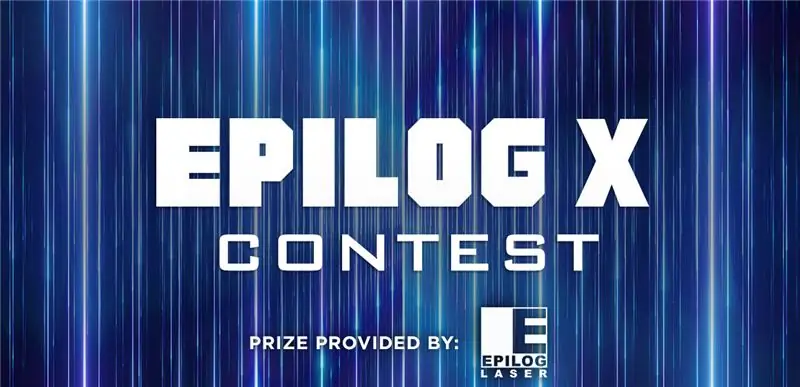
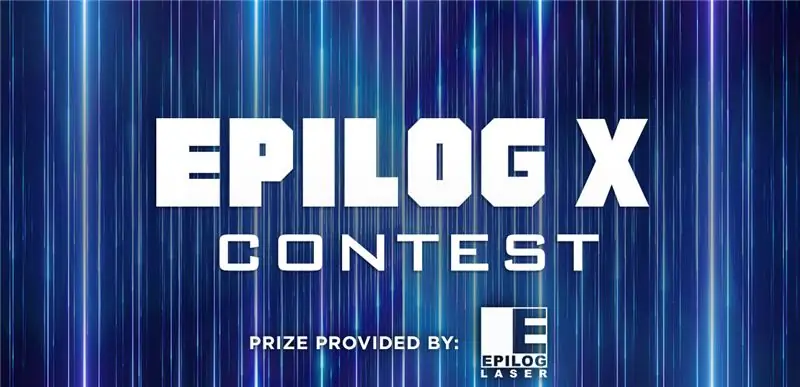
Eerste prijs in de Epilog X-wedstrijd
Aanbevolen:
Robot: Two Ways Mobile bestuurd door Windows Phone .: 6 stappen (met afbeeldingen)
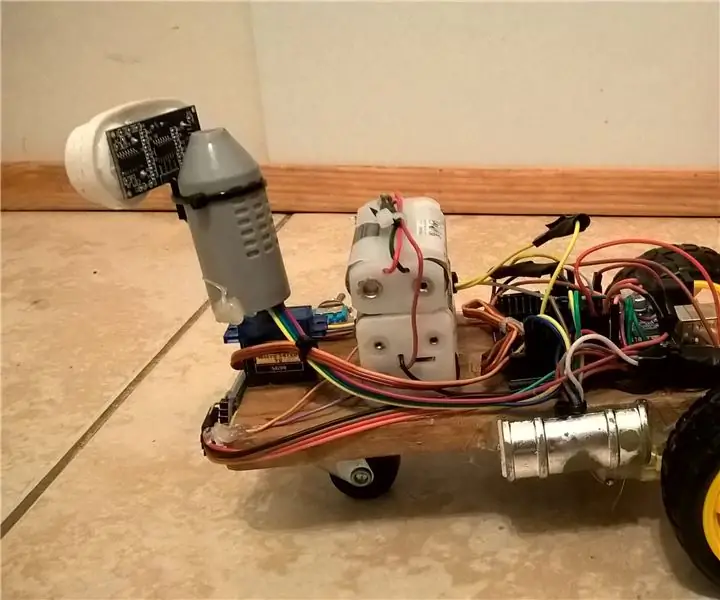
Robot: Two Ways Mobile Gecontroleerd door Windows Phone.: Lijst: Arduino Uno L 293 (Bridge) HC SR-04 (Sonar Module) HC 05 (Bluetooth Module) Tg9 (Micro Servo) Motor met Versnellingsbak (Twee) Batterijhouder (voor 6 AA) Contach Lenzen Houder Draden (mannelijke naar vrouwelijke pinnen) Kabelbinders Hot Lijm (plakken
[WIP] Een Drawbot maken die wordt bestuurd door een Myo-armband: 11 stappen
![[WIP] Een Drawbot maken die wordt bestuurd door een Myo-armband: 11 stappen [WIP] Een Drawbot maken die wordt bestuurd door een Myo-armband: 11 stappen](https://i.howwhatproduce.com/images/006/image-16723-30-j.webp)
[WIP] Een Drawbot maken die wordt bestuurd door een Myo-armband: Hallo allemaal! Een paar maanden geleden besloten we om het idee aan te pakken om een open-frame drawbot te bouwen die alleen een Myo-band gebruikte om hem te besturen. Toen we voor het eerst aan het project begonnen, wisten we dat het zou moeten worden opgesplitst in een paar verschillende p
Kerstboomlicht bestuurd door een stuk speelgoed. 12 stappen (met afbeeldingen) Antwoorden op al uw "Hoe?"
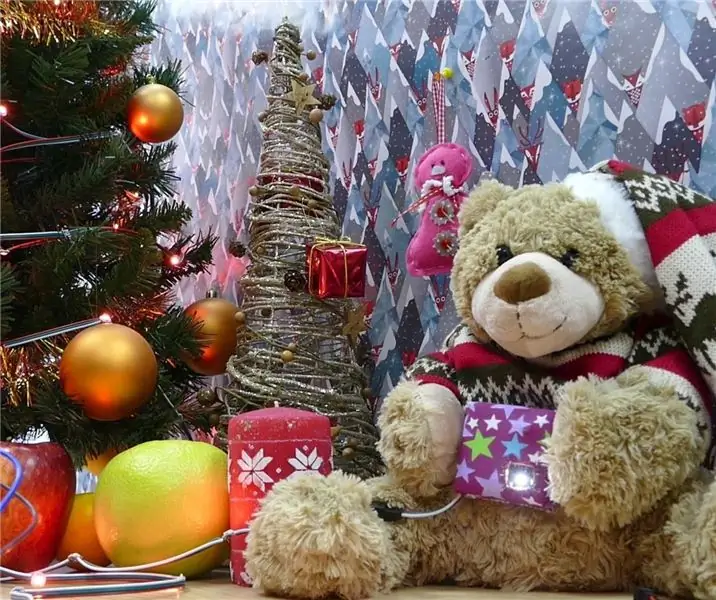
Kerstboomlicht bestuurd door een stuk speelgoed.: Gegroet makers! Kerstmis en nieuwjaar komen eraan. Het betekent een feeststemming, cadeaus en natuurlijk een kerstboom versierd met felle kleurrijke lichtjes. Voor mij zijn kerstverlichting op de massamarkt te saai. Om kinderen een plezier te doen, heb ik een unieke C
DIY-videogame bestuurd door hoofdbeweging (Augmented Reality): 4 stappen
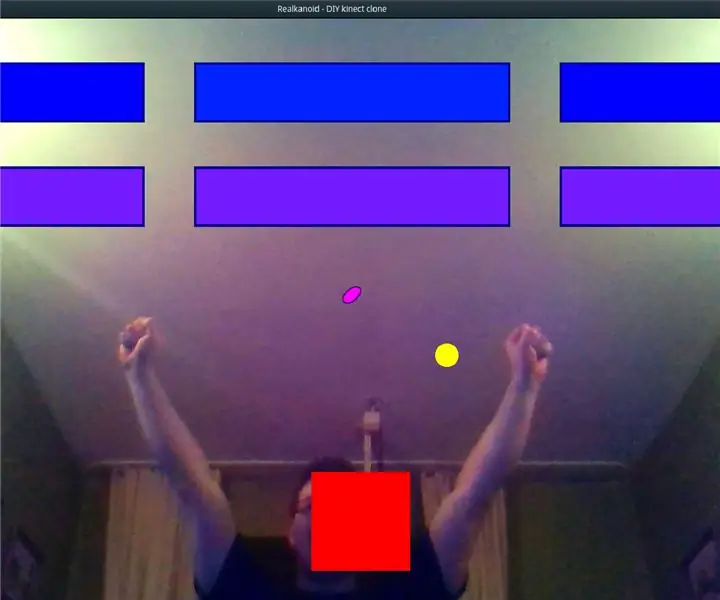
DIY-videogame bestuurd door hoofdbeweging (Augmented Reality): ik wil je laten zien hoe gemakkelijk het tegenwoordig is om een eigen spel te maken dat kan worden bestuurd door je lichaam te bewegen. Je hebt alleen een laptop met webcam en enige programmeervaardigheid nodig. Als je geen laptop en webcam hebt of niet weet hoe je moet programmeren, kun je
Geweldige bewegende versnellingen bestuurd door geweldige knoppen (wordt vervolgd): 9 stappen
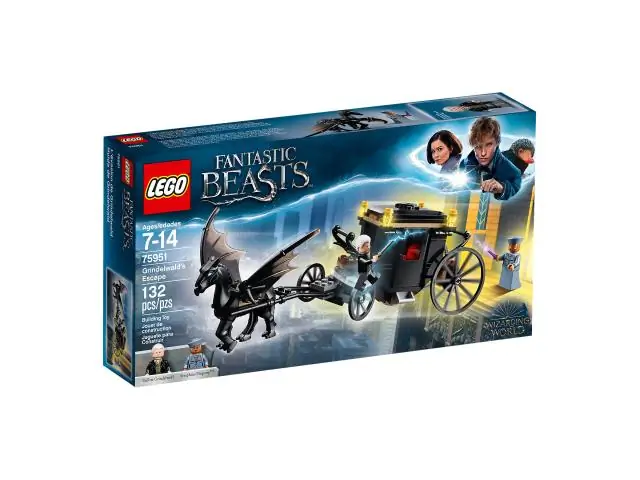
Awesome Moving Gears bestuurd door Awesome Buttons (wordt vervolgd): Fysiek / elektronisch game-ontwerp voor UCLA Design Media Arts met Eddo Stern. Dit instructable is onvolledig. Het project loopt nog