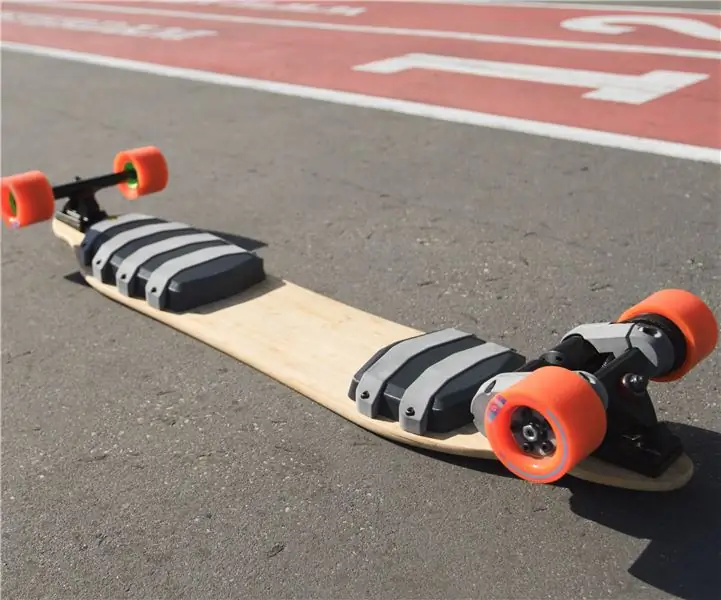
Inhoudsopgave:
2025 Auteur: John Day | [email protected]. Laatst gewijzigd: 2025-01-23 15:01
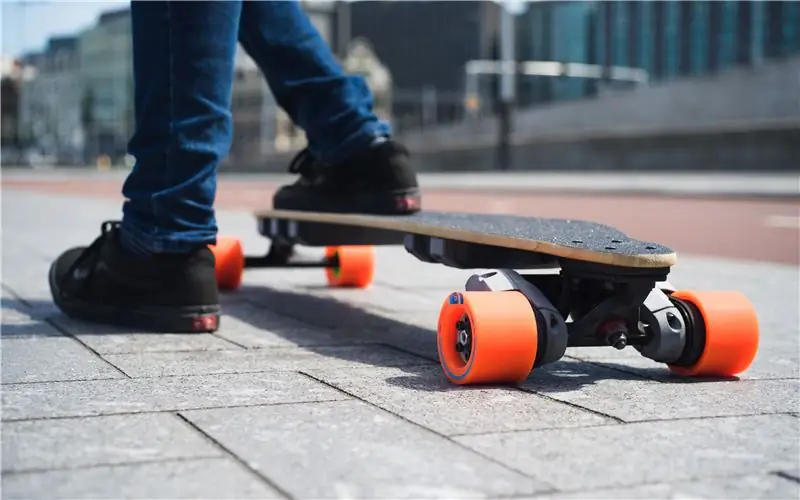
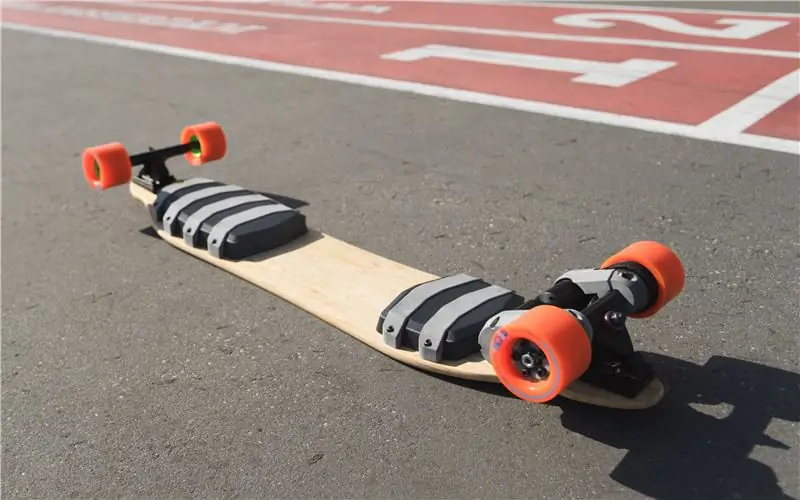
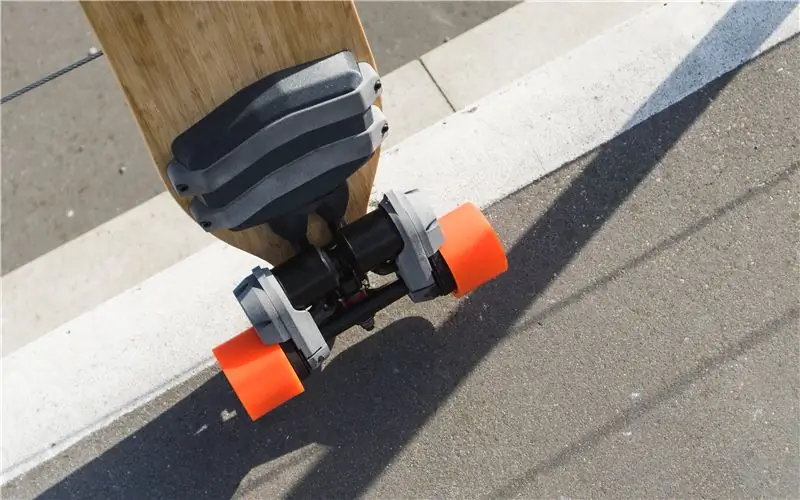
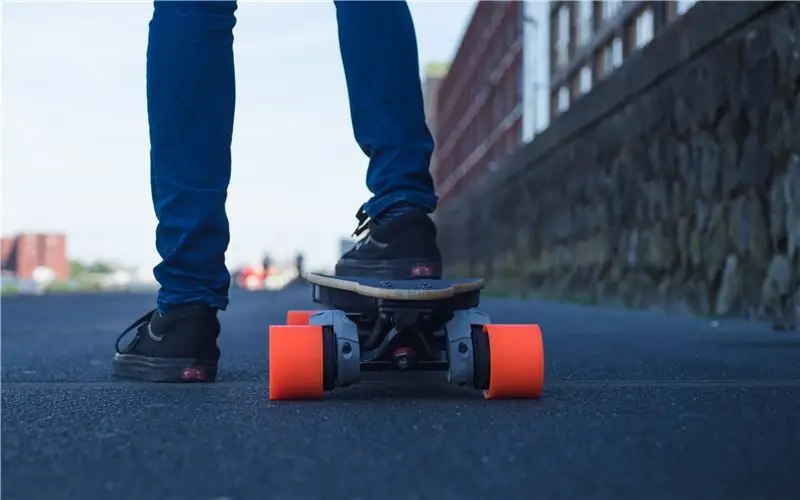
Deze Instructable is een overzicht van het bouwproces voor het Fusion E-Board dat ik heb ontworpen en gebouwd terwijl ik bij 3D Hubs werkte. Het project kreeg de opdracht om de nieuwe HP Multi-Jet Fusion-technologie van 3D Hubs te promoten en om te laten zien hoe meerdere 3D-printtechnologieën effectief kunnen worden gecombineerd.
Ik ontwierp en bouwde een elektrisch gemotoriseerd longboard, dat kan worden gebruikt voor korte tot middelzware reizen of kan worden gecombineerd met het openbaar vervoer om een veel groter reisbereik te bieden. Hij heeft een hoge topsnelheid, is zeer wendbaar en is gemakkelijk mee te nemen als hij niet in gebruik is.
Stap 1: Ontwerpproces
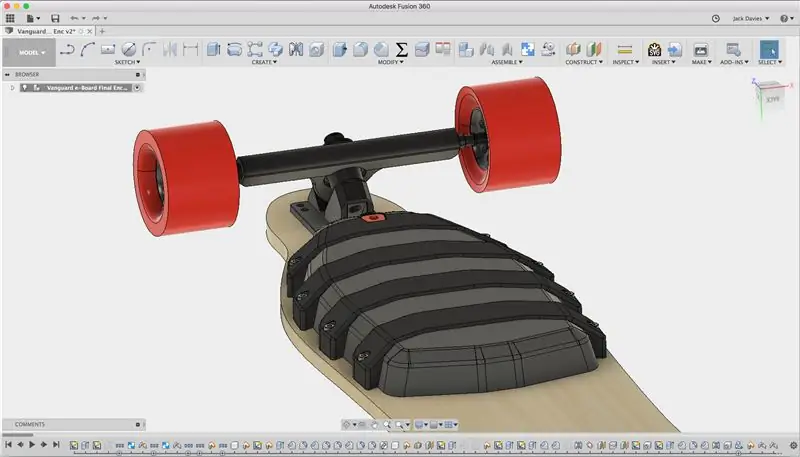
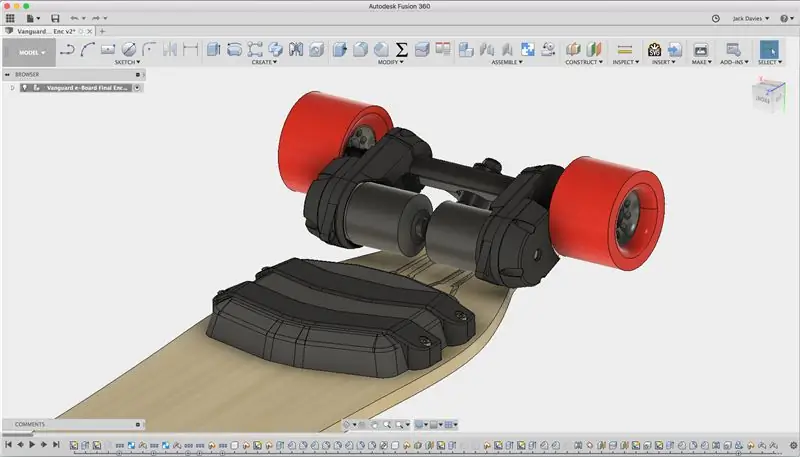
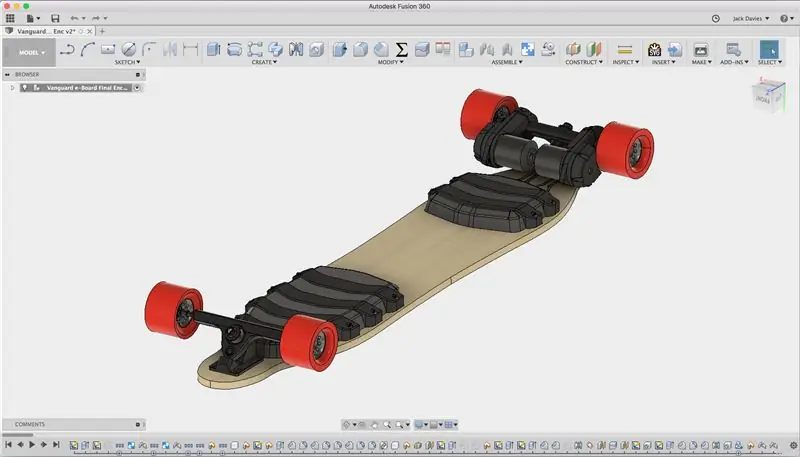
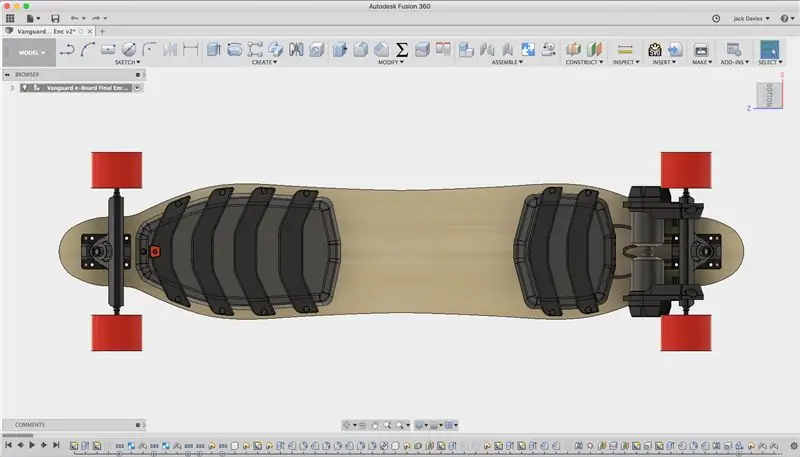
Ik begon het project door de belangrijkste standaardcomponenten van het longboard te identificeren; vrachtwagens, dek en wielen. Dit waren kant-en-klare onderdelen, dus ik heb deze als uitgangspunt voor het ontwerp gebruikt. De eerste fase was het ontwerpen van de aandrijflijn, dit omvat de motorsteunen, de versnellingsopstelling en enkele aanpassingen aan de vrachtwagens. De grootte en positie van de motorsteunen zouden de grootte en locatie van de behuizingen bepalen, dus het was belangrijk dat dit eerst werd voltooid. Ik berekende de gewenste topsnelheid en koppelvereisten, waardoor ik de motoren en batterij voor het bord kon selecteren. Ook werd de overbrengingsverhouding berekend en werden de poeliematen gekozen, samen met de lengte van de aandrijfriem. Hierdoor kon ik de juiste maat van de motorsteunen bepalen wat zorgde voor een goed gespannen riem.
De volgende fase was het ontwerpen van de behuizingen voor de batterij en de snelheidsregelaar (ESC). Het geselecteerde dek bestaat voornamelijk uit bamboe en is dus vrij flexibel en buigt grotendeels in het midden. Dit heeft als voordeel dat het comfortabel is om te rijden, omdat het de hobbels in de weg absorbeert en niet doorgeeft aan de berijder. Dit betekent echter ook dat er een gesplitste behuizing nodig is om de batterij en elektronica te huisvesten, omdat een behuizing over de volledige lengte niet met het bord kan buigen en tijdens bedrijf contact met de grond zou maken. De elektronische snelheidsregelaars (ESC) werden vanwege elektrische beperkingen het dichtst bij de motoren geplaatst. Omdat de motoren via de vrachtwagens zijn bevestigd, verandert de positie tijdens het draaien, dus de behuizing moest zo worden ontworpen dat er ruimte voor de motoren was.
Het batterijsysteem werd aan het andere uiteinde van het dek geplaatst en bevatte de elektronica met betrekking tot stroom. Dit omvatte het batterijpakket, bestaande uit 20 lithium-ion 18650-cellen, het batterijbeheersysteem, aan / uit-schakelaar en oplaadaansluiting.
Ik gebruikte Autodesk Fusion360 voor het hele ontwerpproces, deze software stelde me in staat om snel componenten in de hoofdassemblage te modelleren, wat de ontwikkelingstijd aanzienlijk versnelde. Ik heb ook de simulatiefuncties in Fusion360 gebruikt om ervoor te zorgen dat de onderdelen sterk genoeg zouden zijn, vooral de motorsteunen. Dit stelde me in staat om de afmetingen van de bevestigingen daadwerkelijk te verkleinen, omdat ik de sterkte- en doorbuigingsvereisten kon verifiëren en materiaal kon verwijderen terwijl ik toch een geschikte veiligheidsfactor handhaafde. Nadat het ontwerpproces was voltooid, was het heel eenvoudig om de afzonderlijke onderdelen te exporteren voor 3D-printen.
Stap 2: Aandrijving
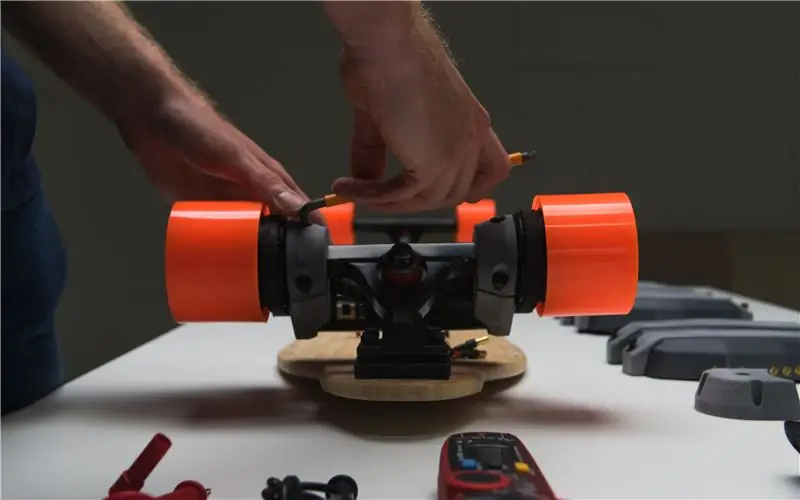
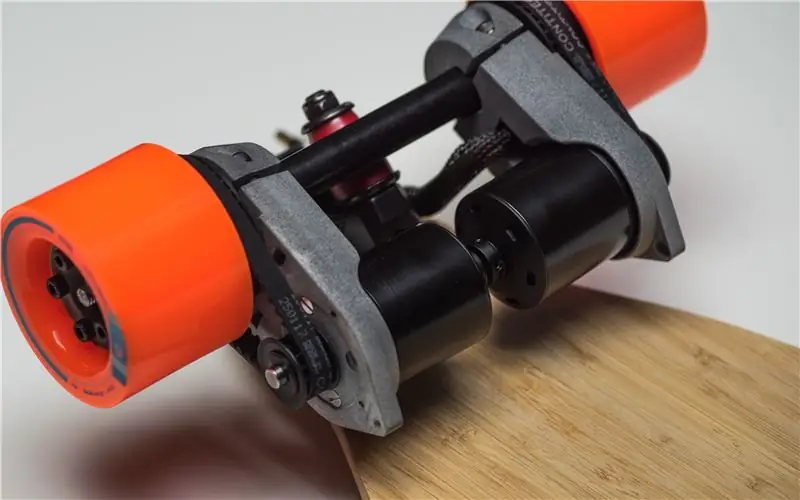
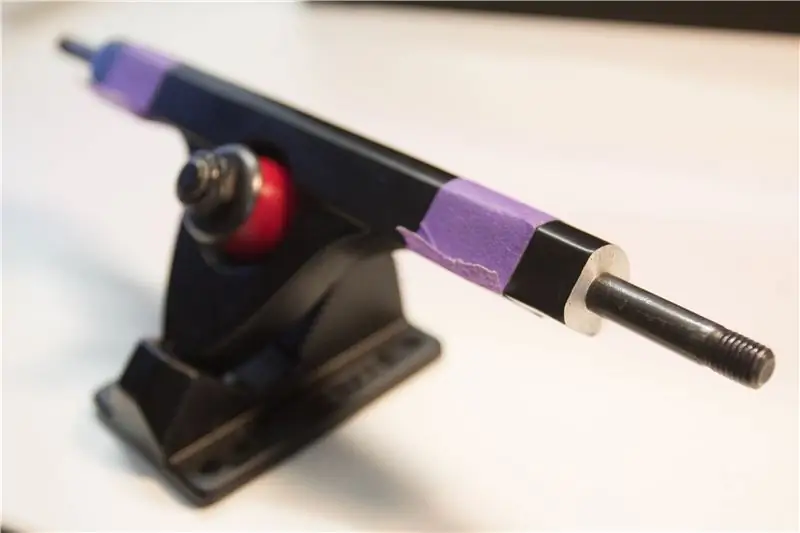
Ik voltooide eerst de bouw van de aandrijflijn om te zorgen voor voldoende ruimte voor de elektronicabehuizing. Ik heb gekozen voor Caliber-trucks om te gebruiken omdat ze een vierkant profiel hebben dat perfect was om de motorsteunen op te klemmen. De as was echter iets te kort om de twee motoren op dezelfde truck te kunnen gebruiken, dus ik moest deze verlengen om de wielen te laten passen.
Ik heb dit bereikt door een deel van de aluminium vrachtwagenhangerbehuizing te verkleinen, waardoor meer van de stalen as zichtbaar wordt. Ik sneed toen het grootste deel van de as naar beneden, waardoor er ongeveer 10 mm over was die ik vervolgens kon inrijgen met een M8-matrijs.
Er kan dan een koppeling worden geschroefd en er kan een andere as met schroefdraad aan worden toegevoegd, waardoor de as effectief wordt verlengd. Ik heb Loctite 648 borgmiddel gebruikt om de koppeling en de nieuwe as permanent vast te zetten om ervoor te zorgen dat ze tijdens gebruik niet zouden losraken. Hierdoor konden de twee motoren op de vrachtwagen passen en was er voldoende ruimte voor de wielen.
De aandrijflijn is voornamelijk geprint met HP Multi-Jet Fusion-technologie, om stijfheid en sterkte te garanderen tijdens hoge acceleraties en remmen, waar de grootste krachten zouden worden overgedragen.
Er is een speciale poelie ontworpen om in de achterwielen te vergrendelen, die vervolgens met een HTD 5M-riem met de motorpoelie werd verbonden. Er is een 3D-geprinte hoes toegevoegd om de katrolconstructie te beschermen.
Stap 3: Ribbehuizingen
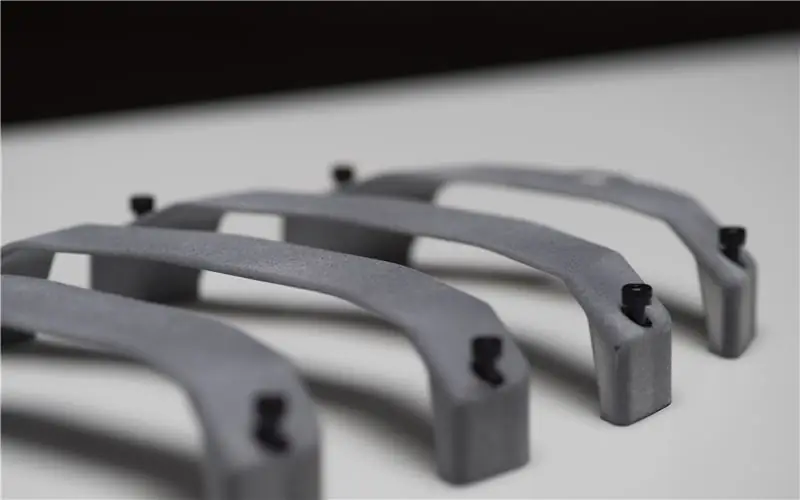
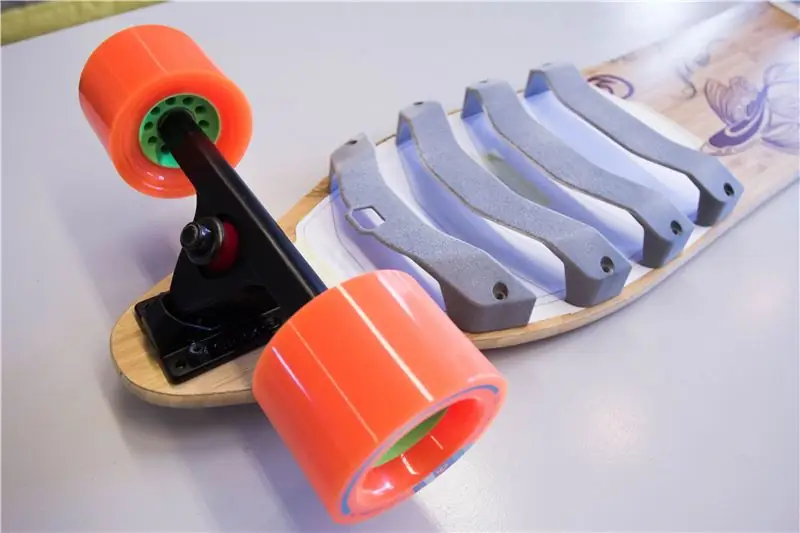
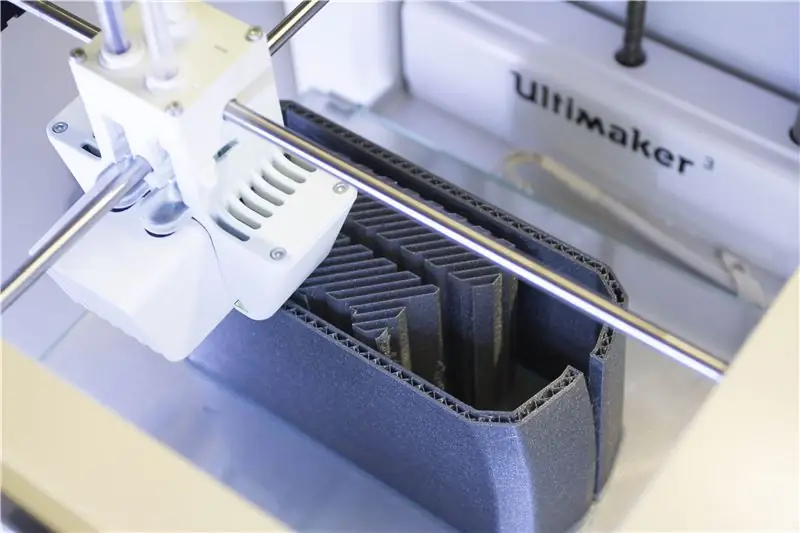
Een van de belangrijkste ontwerpbeslissingen die ik nam, was het scheiden van de behuizingen, wat resulteerde in een strak uiterlijk en waardoor het flexibele dek kon functioneren zonder extra stijfheid van de behuizingen. Ik wilde de functionele aspecten van de HP Multi Jet Fusion-technologie overbrengen, dus besloot ik het hoofdgedeelte van de behuizingen FDM te printen, wat de kosten verlaagde, en vervolgens de HP-onderdelen gebruikt om ze te ondersteunen en vast te klemmen aan het deck. Dit zorgde voor een interessante esthetiek en was ook zeer functioneel.
De FDM-bedrukte behuizingen werden in tweeën gedeeld om te helpen bij het printen, aangezien ondersteunend materiaal van het buitenoppervlak kon worden verwijderd. De splitlijn was zorgvuldig gepositioneerd om ervoor te zorgen dat deze werd verborgen door het HP-gedeelte wanneer deze op het bord werd geklemd. Gaten voor de motoraansluitingen werden toegevoegd en vergulde kogelconnectoren werden op hun plaats gelijmd om
Inzetstukken met schroefdraad werden in het bamboedek ingebed om de behuizingen aan het bord te bevestigen en werden gelijk met het bordoppervlak geschuurd om ervoor te zorgen dat er geen opening was tussen het dek en de behuizing.
Stap 4: Elektronica
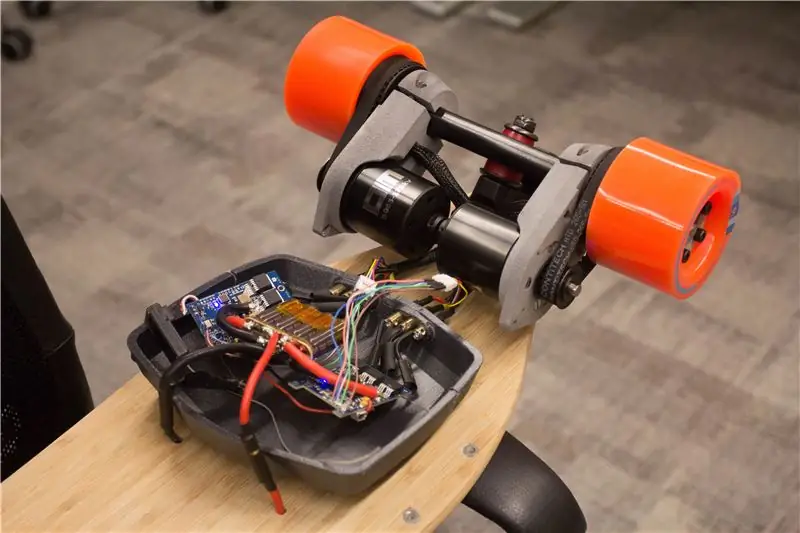
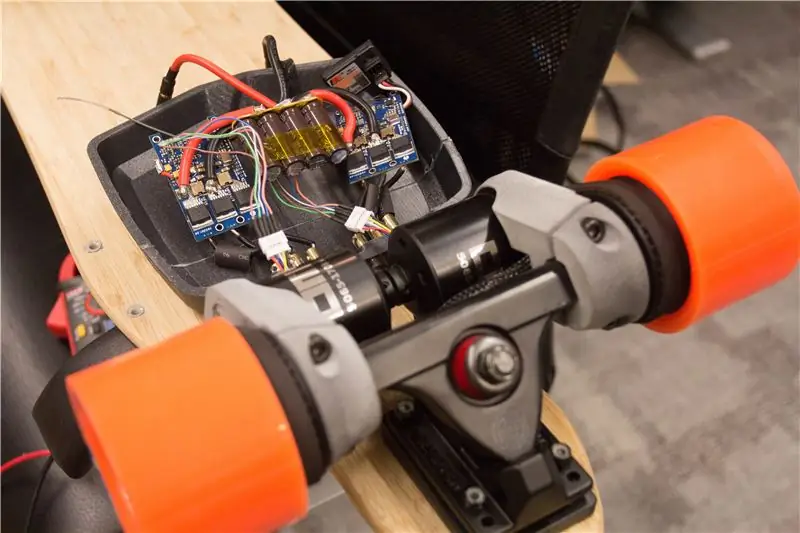
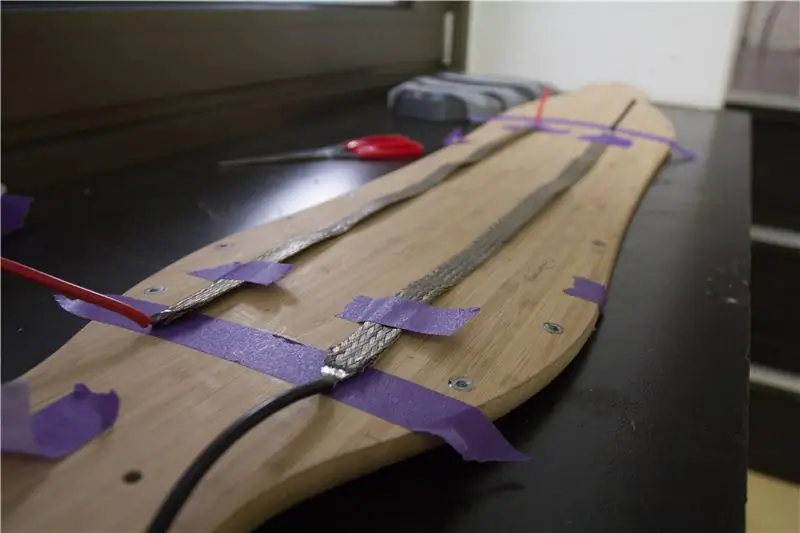
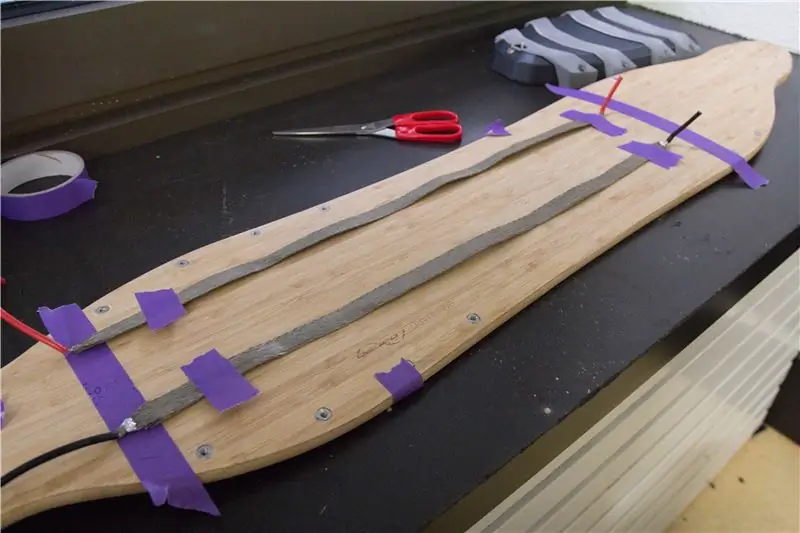
De elektronica is zorgvuldig gekozen om ervoor te zorgen dat het bord krachtig maar ook intuïtief in gebruik was. Dit bord kan potentieel gevaarlijk zijn als er storingen optreden, dus betrouwbaarheid is een zeer belangrijke factor.
Het batterijpakket bestaat uit 20 afzonderlijke 18650 lithium-ioncellen die aan elkaar zijn gepuntlast om een 42v-pakket te vormen. 2 cellen zijn parallel gelast en 10 in serie; de cellen die ik gebruikte waren Sony VTC6. Ik heb een puntlasapparaat gebruikt om de nikkelen lipjes te lassen om het pakket te vormen, omdat solderen te veel warmte veroorzaakt die de cel kan beschadigen.
De stroom van de batterijbehuizing werd overgebracht naar de snelheidsregelaarkast met behulp van een platte gevlochten kabel die net onder de griptape aan de bovenzijde van het deck liep. Hierdoor konden de kabels 'verborgen' worden en elimineerde de noodzaak om kabels aan de onderkant te leggen die er lelijk uit zouden zien.
Omdat dit een dual-motor board is, zijn er twee snelheidsregelaars nodig om elke motor onafhankelijk te regelen. Ik heb de VESC-snelheidscontroller gebruikt voor deze build, een controller die speciaal is ontworpen voor elektrische skateboards, wat hem zeer betrouwbaar maakt voor dit gebruik.
De gebruikte motoren zijn 170kv 5065 out-runners die elk 2200W kunnen produceren, wat veel vermogen is voor dit bord. Met de huidige gearing setup is de maximale snelheid van de boards rond de 35 MPH, en accelereert zeer snel.
De laatste fase was het maken van een afstandsbediening om het bord te bedienen. Vanwege de eenvoudigere bediening kreeg een draadloos systeem de voorkeur. Het was echter belangrijk om een hoge transmissiebetrouwbaarheid te garanderen, aangezien een communicatiestoring ernstige veiligheidsproblemen kan veroorzaken, vooral bij hoge snelheden. Na een paar radiotransmissieprotocollen te hebben getest, besloot ik dat 2,4 GHz-radiofrequentie de meest betrouwbare zou zijn voor dit project. Ik gebruikte een standaard RC-autozender, maar verkleinde het formaat aanzienlijk door de elektronica over te brengen naar een kleine draagbare behuizing die 3D-geprint was.
Stap 5: Voltooide bord- en promovideo
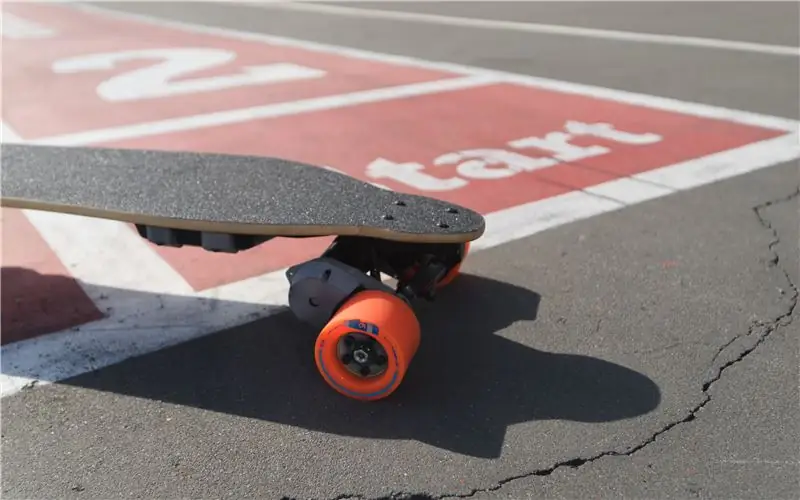
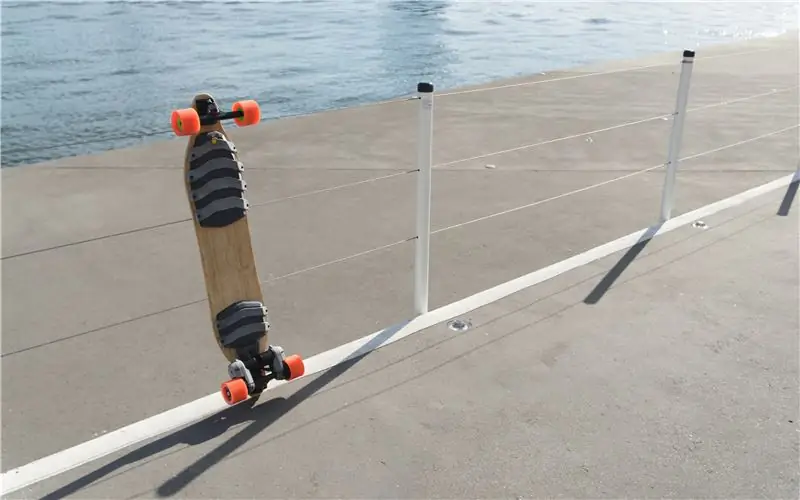
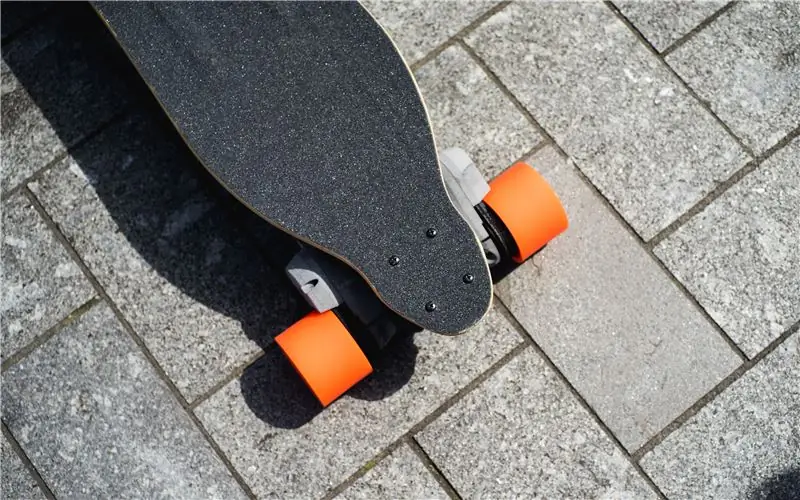
Het project is nu klaar! We hebben een behoorlijk geweldige video gemaakt van het bord in actie, je kunt het hieronder bekijken. Grote dank aan 3D Hubs voor het toestaan van mij om dit project te doen - bekijk ze hier voor al uw 3D-afdrukbehoeften! 3dhubs.com
Aanbevolen:
DIY elektrisch longboard! 7 stappen (met afbeeldingen)
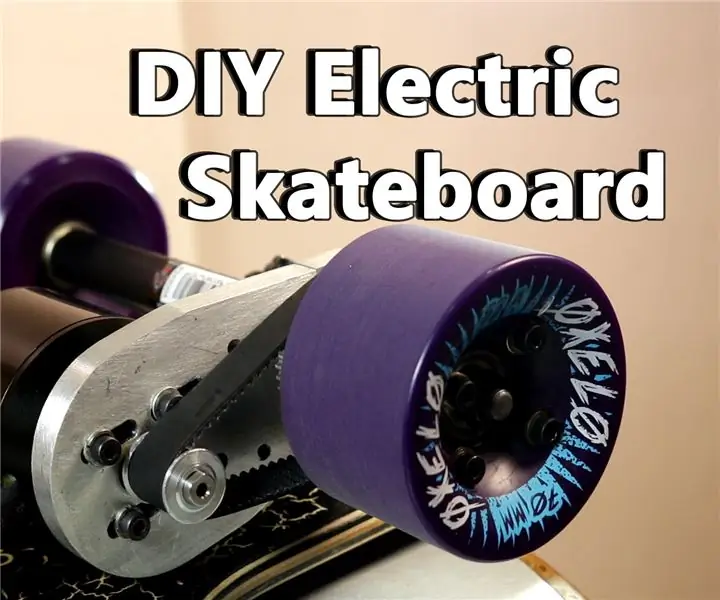
DIY Elektrisch Longboard!: Hallo, mede-makers die er zijn, in deze gids laat ik je zien hoe je een doe-het-zelf elektrisch skateboard maakt met een relatief klein budget. Het bord dat ik heb gebouwd, kan snelheden bereiken van ongeveer 40 km/u (26 mph) en ongeveer 18 km rennen. Hierboven vindt u een videogids en een paar pi
Elektrisch longboard: 6 stappen
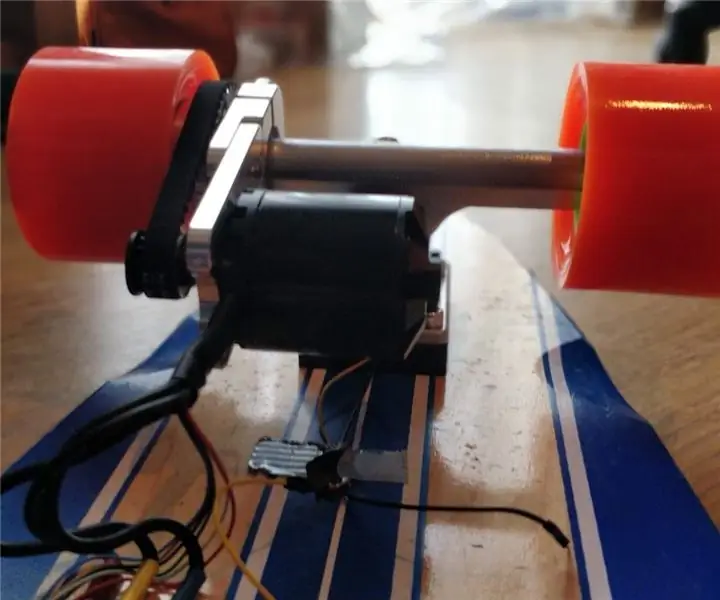
Elektrisch longboard: in deze instructable gaan we een elektrisch longboard maken met een Arduino Uno en een Raspberry Pi
Speedboard: elektrisch skateboard: 5 stappen
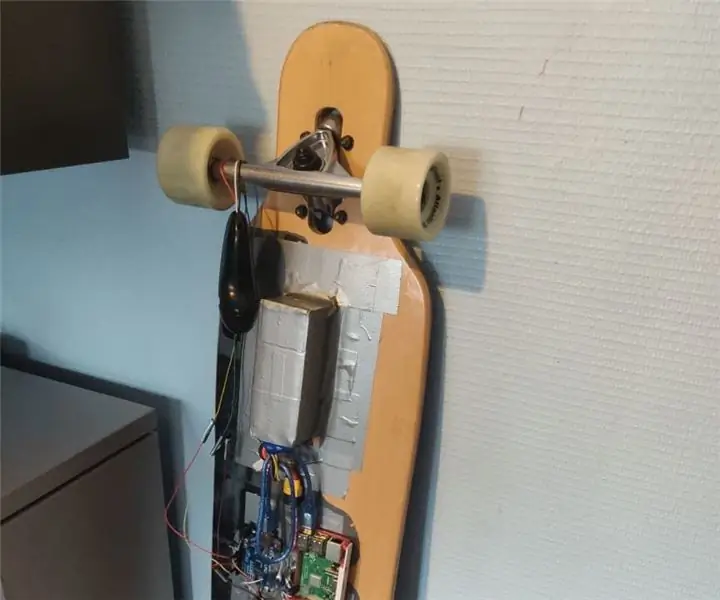
Speedboard: Elektrisch Skateboard: Hallo! Ik ben een MCT College Student uit Howest in België. Vandaag zal ik je een stapsgewijze handleiding geven over hoe je een elektrisch skateboard kunt maken met een Raspberry Pi en Arduino. Ik werd geïnspireerd om dit project te maken door een beroemde youtuber genaamd Casey Neistat
Afstandsbediening voor elektrisch skateboard: 7 stappen
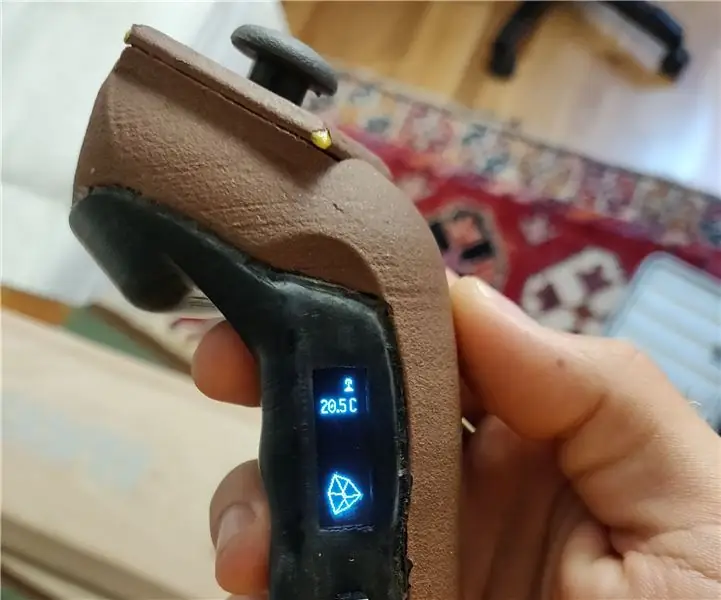
Elektrisch skateboard-afstandsbediening: maak een afstandsbediening voor elektrisch skateboard, in JAVASCRIPT! Doe mee aan mijn reis, hopelijk leer je iets. Dit zal geen stapsgewijze zelfstudie zijn. Het zal meer een showcase zijn van wat ik heb gebruikt, hoe ik het heb gedaan en ik weet zeker dat jij het ook kunt doen. Ik raad het zelfs aan
Diy elektrisch skateboard: 14 stappen (met afbeeldingen)
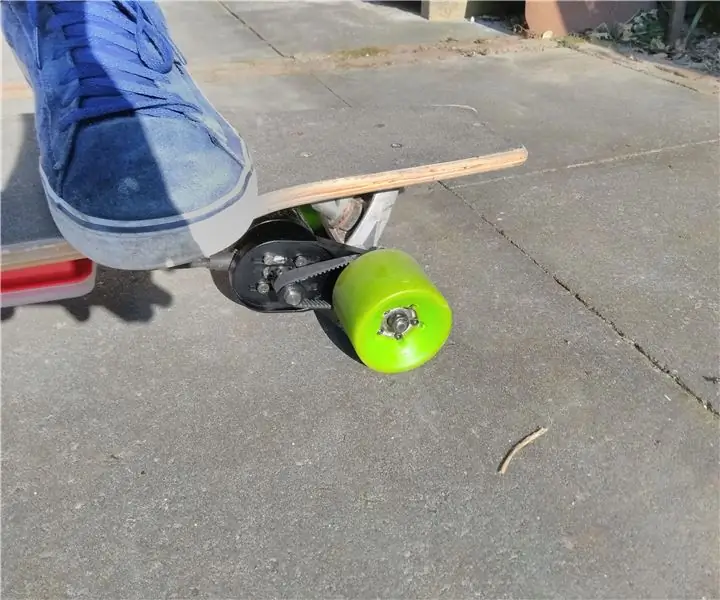
Diy elektrisch skateboard: na 2 jaar onderzoek heb ik mijn eerste elektrische skateboard gebouwd. Sinds ik een instructie heb gezien over hoe je je eigen elektrische skateboard kunt bouwen, ben ik verliefd geworden op doe-het-zelf elektrische skateboards. Je eigen elektrische skateboard maken is een vorm van m